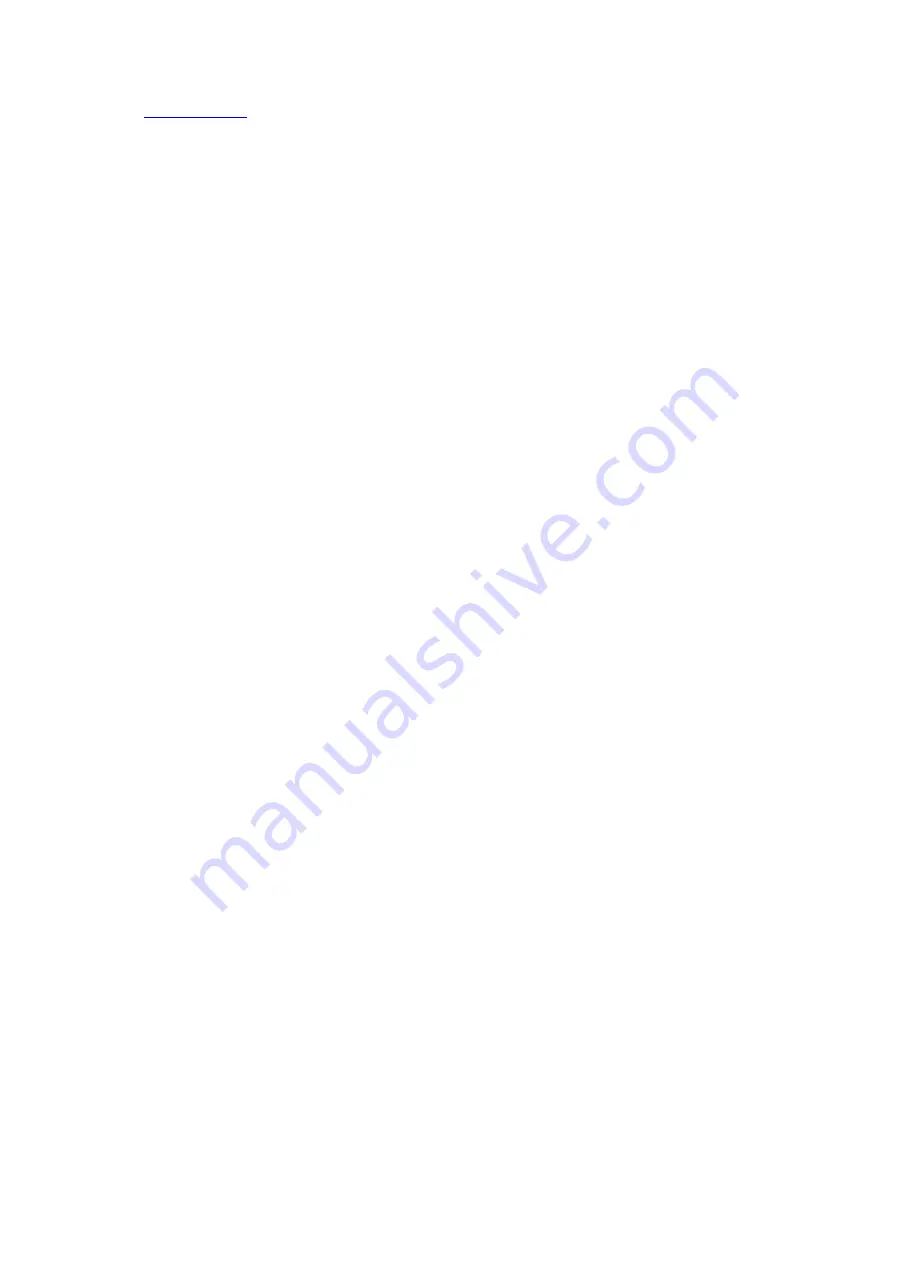
PINPOINT TEST A: THE ENGINE DOES NOT CRANK OR THE RELAY CLICKS
A1: CHECK THE BATTERY CONNECTIONS......................................................
A2: CHECK THE BATTERY VOLTAGE ...............................................................
A3: CHECK SWITCHED POWER SUPPLY TO THE SOLENOID........................
A4: CHECK B+ TO THE STARTER .....................................................................
A5: CHECK THE STARTER GROUND CIRCUIT.................................................
A6: CHECK B+ TO STARTER RELAY.................................................................
A7: CHECK RELAY GROUND CIRCUIT..............................................................
A8: CHECK RELAY SWITCHING CIRCUIT .........................................................
A10: CHECK CIRCUIT 30 (RD) CONTINUITY .....................................................
A11: CHECK THE IGNITION SWITCH ................................................................
A12: CHECK CIRCUIT 50 (GY) CONTINUITY .....................................................
A13: CHECK THE CONTINUITY OF CIRCUIT 50 (GY/BK) .................................
A14: CHECK CIRCUIT 50 (GY/BK) FOR SHORT TO GROUND..........................
A15: CHECK CIRCUIT 30 (RD) FOR SHORT TO GROUND ...............................
A16: CHECK CIRCUIT 50 FOR SHORT TO GROUND........................................
PINPOINT TEST B: THE ENGINE CRANKS SLOWLY
B1: CHECK THE BATTERY VOLTAGE ...............................................................
B2: CHECK THE SUPPLY TO STARTER............................................................
B3: CHECK THE STARTER GROUND CIRCUIT.................................................
PINPOINT TEST C: UNUSUAL STARTER MOTOR NOISE
C1: CHECK THE STARTER MOUNTING ............................................................
C2: CHECK THE STARTER DRIVE ....................................................................