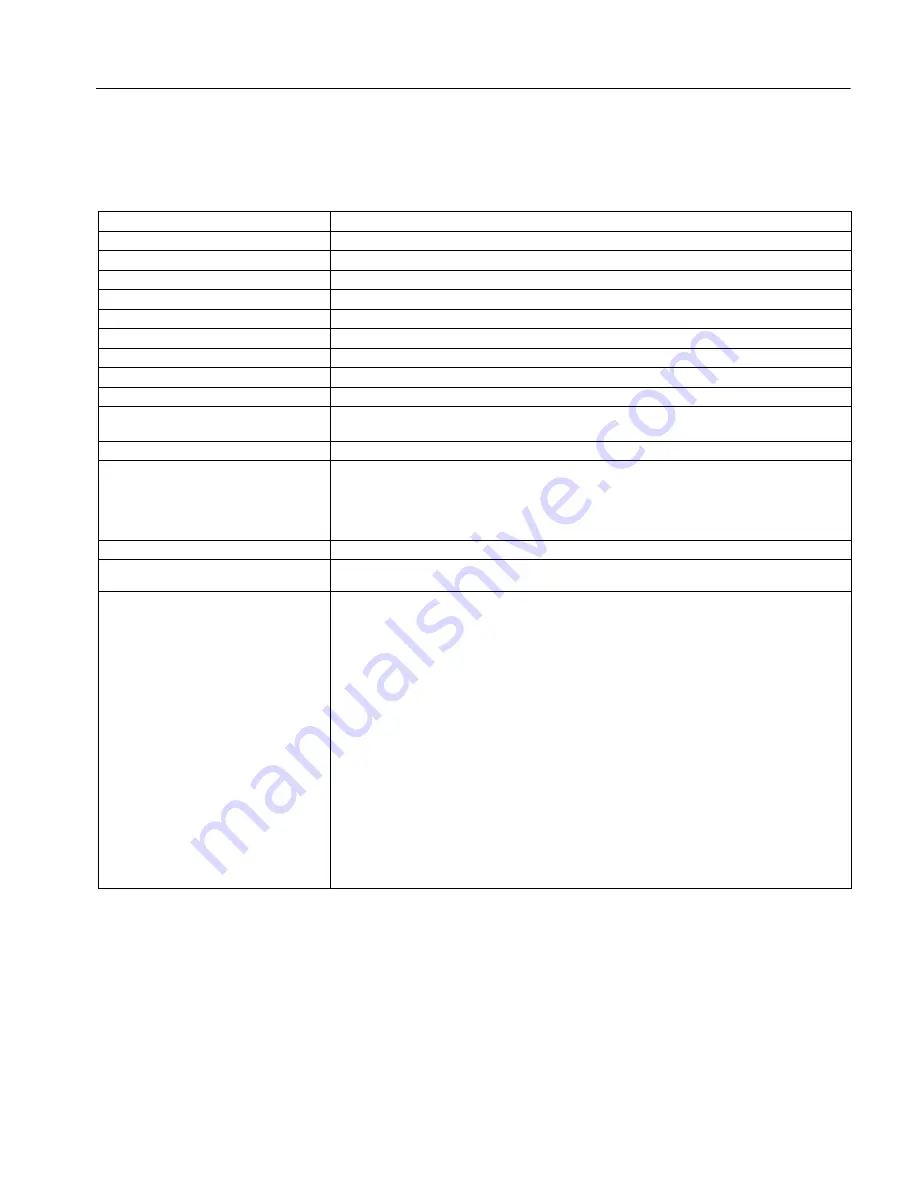
Dry-well Calibrator
Specifications and Environmental Conditions
3
Specifications and Environmental Conditions
Specifications
Table 1. Specifications
Range
-10 °C to 122 °C (14 °F to 252 °F) at an ambient of 23 °C
Accuracy
±0.25 °C
Stability
±0.05 °C
Resolution
0.1 °C or °F
Well-to-Well Uniformity
±0.2 °C with sensors of similar size at equal depths within wells
Heating Times
ambient to 100 °C: 10 minutes
Stabilization
7 minutes
Cooling Times
ambient to 0 °C: 10 minutes
Well Depth
102 mm (4 inches)
Removable Inserts
See
Power Requirements
Power Rates
100 to 240 V ac, 50/60 Hz, 90 VA; or 12 V dc, 2.6 A
Size
100 mm H x 152 mm W x 175 mm D (4 in x 6 in x 6.9 in)
Environmental Conditions
Operation Temperature Range
Ambient Relative Humidity
Ambient Pressure
Altitude
5 to 50 °C (41 to 122 °F)
0 to 80 % RH for temperatures up to 30 ºC, 0 to 50 % RH for temperatures 30 to 50 °C
75 kPa to 106 kPa
<2000 m
Weight
4 lb (1.8 kg)
Safety
Mains
IEC 61010-1: Overvoltage Category II, Pollution Degree 2
Additional
IEC 61010-2-010 (Heating)
Electromagnetic Compatibility (EMC)
International................................. IEC 61326-1: Basic Electromagnetic Environment
CISPR 11: Group 1, Class A
Group 1: Equipment has intentionally generated and/or uses conductively-coupled radio
frequency energy that is necessary for the internal function of the equipment itself.
Class A: Equipment is suitable for use in all establishments other than domestic and those
directly connected to a low-voltage power supply network that supplies buildings used for
domestic purposes. There may be potential difficulties in ensuring electromagnetic
compatibility in other environments due to conducted and radiated disturbances.
Caution: This equipment is not intended for use in residential environments and may not
provide adequate protection to radio reception in such environments.
Emissions that exceed the levels required by CISPR 11 can occur when the equipment is
connected to a test object.
The equipment may not meet the immunity requirements of this standard when test leads
and/or test probes are connected.
Korea (KCC) ............................... Class A Equipment (Industrial, Broadcasting, &
Communication Equipment)
Class A: Equipment meets requirements for industrial electromagnetic wave equipment and
the seller or user should take notice of it. This equipment is intended for use in business
environments and not to be used in homes.
USA (FCC).................................. 47 CFR 15 subpart B. This product is considered an exempt
device per clause 15.103.