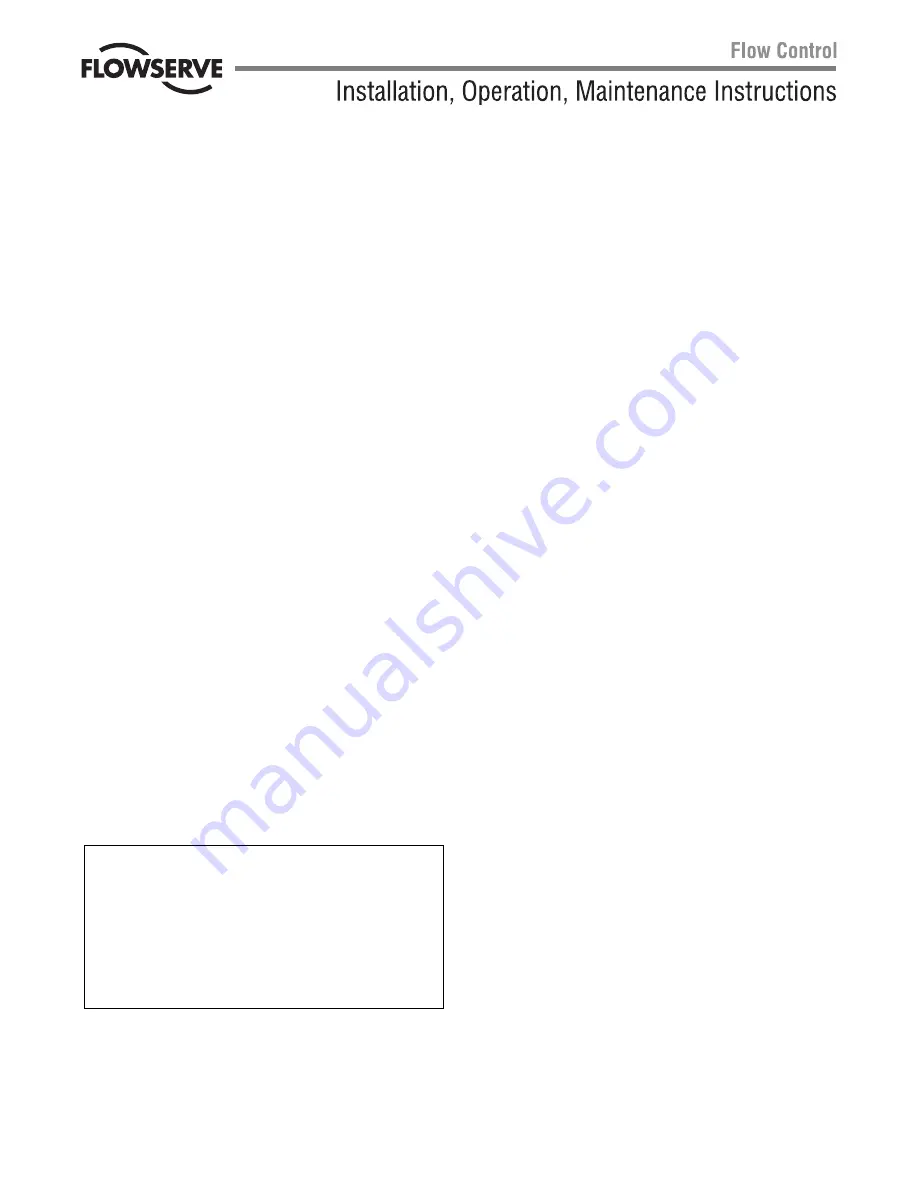
37-1
Orig. 5/97
Valtek No. 35190
Valdisk 150
Control Valves
NOTE: Selecting the proper fastener material is the
responsibility of the customer. Typically, the supplier
does not know what the valve service conditions or
environment may be. ValtekÔs standard bolting material
is B7/2H. B8 (stainless steel) is optional for applications
above 800
O
F and with stainless steel or alloy body
valves. The customer therefore must consider the
materialÕs resistance to stress corrosion cracking in
addition to general corrosion. As with any mechanical
equipment, periodic inspection and maintenance is
required. For more information about fastener materi-
als, contact your local Valtek representative or factory.
Unpacking
1. While unpacking the valve, check the packing list
against the materials received. Lists describing the
valve and accessories are included in each shipping
container.
2. When lifting the valve from the shipping container,
position lifting straps to avoid damage to tubing and
mounted accessories. Most Valdisk 150 valves
may be lifted by the actuator lifting ring. If no lifting
ring is provided, lift the valve using lifting straps or
hook through the yoke legs and outer end of the
body.
3. In the event of shipping damage, contact your ship-
per immediately.
4. Should any problem arise, contact your Valtek rep-
resentative.
GENERAL INFORMATION
The following instructions are designed to assist in
unpacking, installing, operating and performing mainte-
nance as required on Valdisk 150 butterfly valves.
Product users and maintenance personnel should thor-
oughly review this bulletin prior to working on the valve.
Separate maintenance instructions cover additional fea-
tures (such as positioners, special accessories, fail-
safe systems,etc.)
This publication does not contain information on install-
ing, maintaining, troubleshooting, calibrating, and oper-
ating Valtek actuators or positioners. Refer to the
appropriate Valtek Installation, Operation, Maintenance
Instructions when this information is required.
To avoid possible injury to personnel or damage
to valve parts, WARNING and CAUTION notes
must be strictly adhered to. Modifying this prod-
uct, substituting nonfactory parts, or using
maintenance procedures other than outlined
could drastically affect performance, be hazard-
ous to personnel and equipment, and may void
existing warranties.
WARNING: Standard industry safety practices must
be adhered to when working on this, or any other,
process control product. Specifically, personal
protective and lifting devices must be used as war-
ranted.