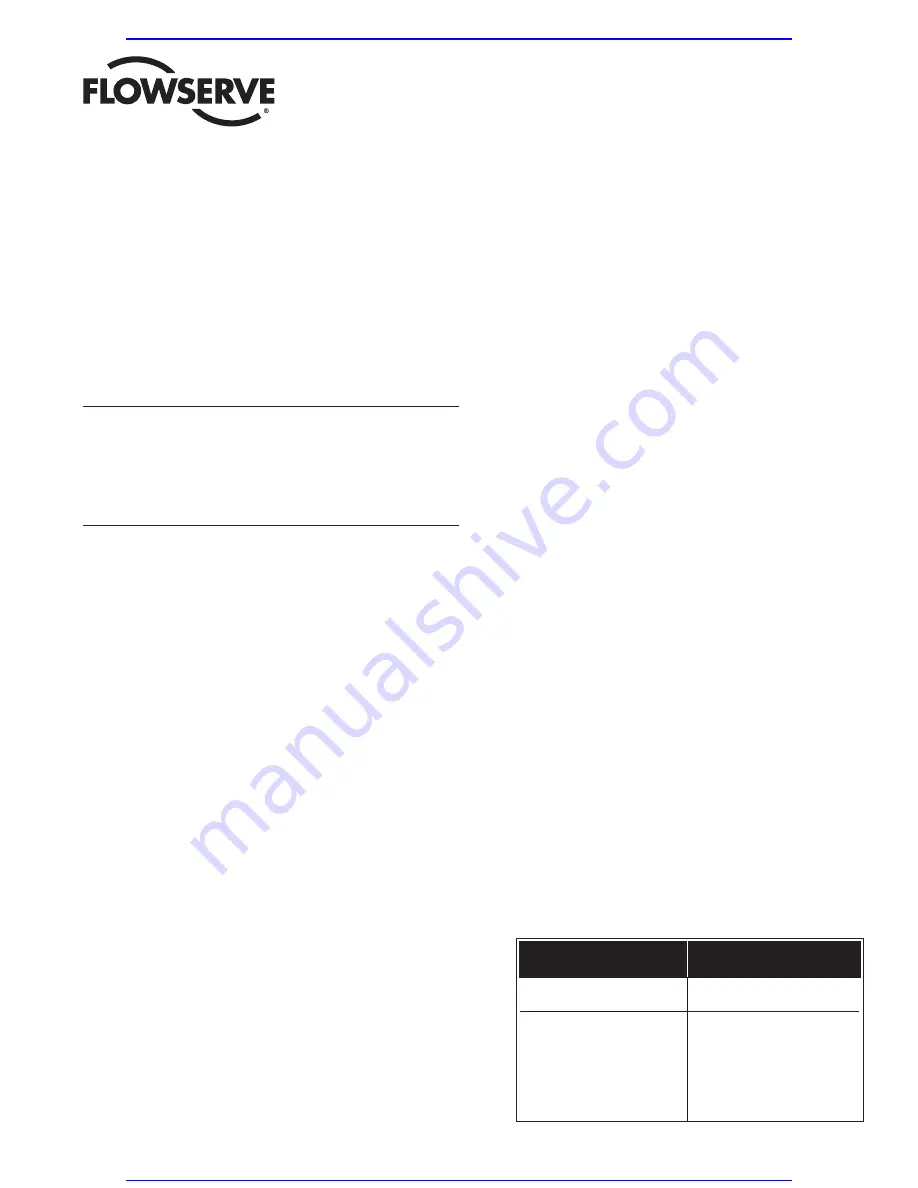
Worcester Controls
CAUTION: Flowserve recommends that all products which must be
stored prior to installation be stored indoors, in an environment
suitable for human occupancy. Do not store product in areas where
exposure to relative humidity above 85%, acid or alkali fumes, radi-
ation above normal background, ultraviolet light, or temperatures
above 120°F or below 40°F may occur. Do not store within 50 feet of
any source of ozone.
A. INSTALLATION
1. Valve is designed for flow in either direction. Use care to exclude
pipe sealants from valve cavity.
2. When installing CPT 44 or CPT 51/52 flanged valves, use
standard gaskets suitable for the specific service and tighten the
flange bolts or studs evenly. On CPT 44 wafer valves it is
recommended to leave the ball in the open position while
installing, to eliminate possibility of damaging ball finish.
3. CPT 44 Weld End Valves (SW, BW):
NOTES
: Prior to welding, THOROUGHLY CLEAN ALL JOINT
SURFACES to prevent contamination.
Valves with “AG”, “GG”, “PG”, “RG”, and “XG” seat/body seal
combinations and V67 option code are compatible with welding
temperatures. Therefore, these valves are weld-as-is and do not have
to be disassembled to be welded in line. These valves will have a red
welding tag attached. If these valves are disassembled, the graphite
coated stainless steel gasket body seals (code “G”), and the seat back
seals (used with “A” or “G” seats only) must be replaced. When
welding these valves, the valve must be open to prevent adhesion of
weld spatter to the ball. Use STICK or MIG welding, and allow valve
and joint to cool to the touch between passes.
For All Other Weld End Valves:
a. Tack weld the valve in place.
b. Remove actuator and all four body nuts and bolts and place
the valve in the open position.
c. Remove center section from between pipe ends by separating
the pipe ends from the body by at least
!?8
" to allow locating
diameter on the back of the metal characterized seat (inserted
into oversized pipe end bore) to clear pipe end flange.
d. With valve in closed position, remove seats, seat back seal(s),
body seals and ball. Return the body to its original position
and temporarily secure it with two bolts diagonally opposite
each other.
e. Weld valve in line. If gas welding is used, do not play flame on
valve body.
f. Allow valve to cool. Remove body and, with stem in the closed
position, replace ball, seats and install new seat back seal(s),
which are shipped separately from valve. Do not reuse old seat
back seal(s). The characterized seat has a “V” or “Slot” cut in it
for improved flow control, and must be properly oriented to
function. A locating pin is provided in the body, and a groove
in the seat, to assure that proper alignment is accomplished.
The seat must fit properly and not jam on the pin. The opposite
seat has a standard round port in it.
g. Open the valve and replace body seals, or add new body seals, if
they were shipped separately from the valve. Temporary Buna
body seals, if found in the valve as received, are not to be reused.
(If coated stainless steel “S” gasket body seals are used [Code M
or G], install them with wide flange facing the body [see view A-A
on page 6]). Before putting the center section between the pipe
ends, make sure that the seat back seal is centered on the back of
the seat. If it is not, it could be damaged or cause the valve to leak.
h. Place center section between pipe ends by separating the pipe
ends from the body by at least
A?k
" to allow locating diameter
on the back of the metal characterized seat (for insertion into
oversized pipe end bore) to clear pipe end flange. Replace
actuator and body bolts and nuts. Tighten and torque the body
bolts evenly and diagonally opposite each other, alternating in
a criss-cross pattern to the following torque figures:
17812-N
Metal Characterized-seated Control Valve
1
/
4
" – 4" CPT 44 and
1
/
2
" – 4" CPT 51/52
Installation, Operation and Maintenance Instructions
Carbon Steel
Stainless Steel and
Bolts
Alloy 20 Bolts
Bolt Bolt
Diameter
in-lb
ft-lb
Diameter
in-lb
ft-lb
!?4
"
96-120
8-10
!?4
"
72-94
6-8
%?16
"
156-204
13-17
%?16
"
120-144
10-12
#?8
"
216-264
18-22
#?8
"
192-216
16-18
/?16
"
480-540
40-45
/?16
"
336-384
28-32
!?2
"
720-780
60-65
!?2
"
504-552
42-46
Visit www.boighill.com to request a quote.
Visit www.boighill.com to request a quote.