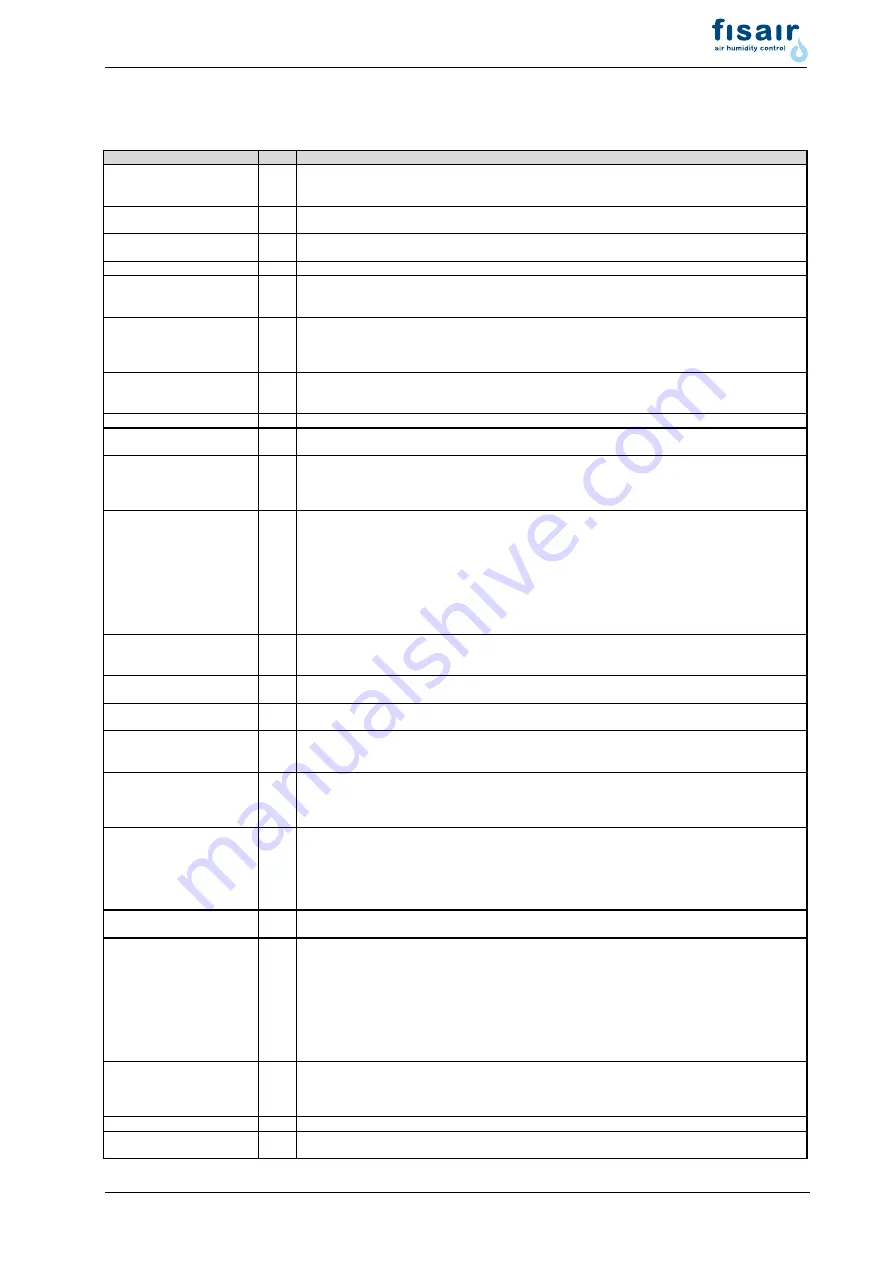
Page 88
8. Glossary
Term
[Index] Explanation
Actual value
1
The actual value is the measured value of a physical quantity, which is compared with the
Set
value [3]
during the control process and may give rise to a readjustment, if required.
Relative humidity (r.h.)
2
The relative humidity (r.h.) describes the maximum percentage of moisture which the ambient air can hold at
a certain temperature.
Set value
3
The set value of a physical quantity (e.g. the
r. h. [2
] ) is the set target for a control process.
Steam output
4
The steam output calculated from the electrical power consumption in kg/h.
Demand
5
The demand describes the dimensionless control signal processed by the control system which is
converted into a proportional
Internal actuator signal [42]
for the power control for steam generation.
Hygrostat
6
Sensor with switching function for the
Relative humidity (r.h.) [2]
in rooms. The trigger point for the
switching function with potential free contacts can be set mechanically. The hygrostat can be used to control
1 step operation [44]
or in the
Interlock (safety) system [11]
to protect against excess humidity.
Update function
7
The update function provides the control with an update of parameter settings which is stored on an external
USB memory stick. The "Update function" parameter is a read-only value which can be used to read out the
status of the update.
SI system of units
8
The system of units with the temperature specified in °C and the quantity specified in kg.
Imperial system of units
9
The system of units used in the USA with the temperature specified in °F (Fahrenheit) and the quantity
specified in lbs.
Initialisation
10
The control performs a self-test, during which the welcome screen with the software version is displayed.
After the parameter settings and measured values have been read in, the
Main screen [14]
is shown on
the display. During the subsequent start blow-down, the read values can be used to query the device status,
which is "Initialisation" in this phase.
Interlock (safety) system
11
The hardware interlock (safety) system makes it possible to immediately interrupt steam production, e.g.
using an emergency stop button
.
The interlock (safety) system must be closed to operate the unit. The
interlock (safety) system must be implemented on-site with one or several potential free contacts (switched
in series). It is connected to the control at terminals 1 and 2, with terminal 1 carrying 230 VAC as standard.
In a special design (e.g. for the U.S. market), the interlock (safety) system is converted to low voltage
through the additional use of a relay to meet local safety requirements. Instead of terminals 1 and 2 on the
control, a potential free connection of the relevant DIN rail terminals must then be implemented on-site. If the
interlock (safety) system is opened, the status of the unit changes to "Interlock (safety) system open".
Software control command
12
Coded command, which is, for example, sent from the building control system or a PLC via the
Communication interface [13]
to the control. The command set available is listed in separate
Communication interface
13
Serial computer interface for remote control of the unit using, for example, the
Modbus [17]
RTU protocol.
Main screen
14
Screen content during the normal operation of the unit. The main screen includes the main display (in the
middle of the screen) and the status icons (left and right of the main display).
Standby heating
16
So that steam production can be started more quickly, the standby heating keeps the water in the cylinder
warm, if no
Demand [5]
is present. The
Interlock (safety) system [11]
must be closed. Heating and
pause times are adjustable.
Modbus
17
Modbus is a communications protocol for serial data transmission for the remote control of units, which is
Timer function
18
The timer makes it possible to limit the duration of steam production in the short-time range, starting when
steam production is halted (if no demand exists in normal operation), or ECO mode . The timer is triggered
by pressing a button, which must be connected to the
digital input [97]
of the mainboard. In addition, the
Digital function [98]
parameter must be set to "Timer_start". The "0" setting deactivates the timer. "1" or
"2" is used to specify whether the steam is turned off or if there is a return to ECO mode after the timer has
elapsed.
Solenoid valve (SV)
19
The solenoid valves for the water supply to the steam cylinder(s) are labelled with Y1, Y2, Y3 and Y4 in the
circuit diagrams.
Start blow-down
20
The unit performs a
Blow-down [58]
after it was switched off and has been switched on again. The
process varies depending on the unit type. For the
ELDB [77]
it is important that, when the main contac-
tor is first switched, overcurrent due to excessive conductivity of the cylinder water does not occur while
simultanously water level is high. A
Partial blow-down [21]
is therefore used to ensure that the current
does not reach an impermissible value. This procedure is not required for the
HKDB [78]
. The only
checks carried out here are on the functioning of the level control and the blow-down pump, by carrying out a
plausibility check of the measured value of the water level sensor which is transferred in the context of a
partial blow-down [21]
.
Partial blow-down
21
Only part of the cylinder water is pumped off during the
Blow-down [58]
. For the
ELDB [77]
, a partial
blow-down is carried out periodically after 40 solenoid valve operating cycles (fillings), when the standard
setting is left untouched. For the
HKDB [78]
, the frequency of the partial blow-down is determined by the
steam volume.
Full blow-down
22
All of the cylinder water is pumped off during the
Blow-down [58]
.
Dilution
23
A dilution is a
Partial blow-down [21]
, which is caused by excessive conductivity of the cylinder water. For
deconcentration, fresh water is used to top up the cylinder after the partial blow-down.
documentation, which is available from
Fisair
est.
widely used in industry.
Fisair
ls use the MODBUS - RTU (remote terminal unit) variant.
Separate documentation is available upon request from
Fisair.