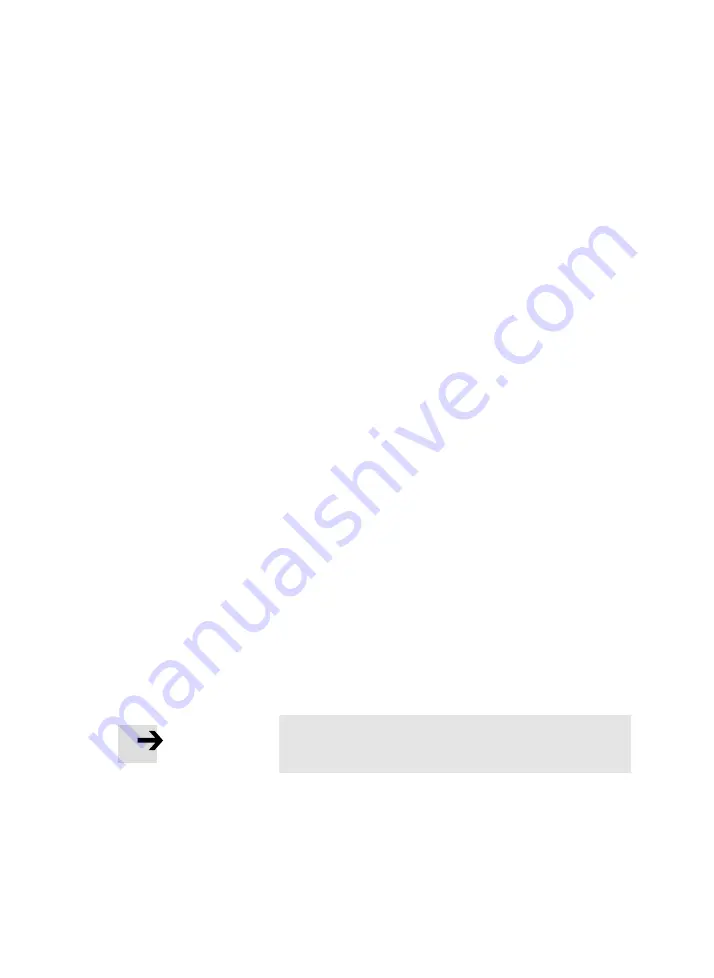
4. Commissioning
4−5
Festo P.BE−CPX−CMA X−SYS−EN en 0908NH
4.1.2
Installing the Festo Configuration Tool and FCT CMAX plug−in
The Festo Configuration Tool (FCT) is the software platform for
configuring and commissioning different components and
devices from Festo.
The FCT consists of the following components:
A framework as program start and entry point with uni
form project and data management for all supported
types of devices.
A plug−in for each of the special demands of each device
type (e.g. CMAX) with the necessary descriptions and
dialogs. The plug−ins are managed and started from the
framework.
The CMAX plug−in for the Festo Configuration Tool helps to
carry out all the steps necessary for commissioning a CMAX.
With the CMAX plug−in CMAX for the Festo Configuration Tool,
you can carry out most parameterisations offline, i.e. without
the CMAX having to be connected to the PC, e.g. for prepar
ing the actual commissioning while the system is being de
signed.
Installing the FCT
The FCT is installed using an installation program on your PC
under Windows 2000, XP or Vista. The CMAX plug−in is in
stalled on your PC together with the installation program of
the FCT.
Note
Administrator rights are required for installing the FCT.
Summary of Contents for CPX-CMAX-C1-1
Page 2: ......
Page 22: ...Contents and general safety instructions XX Festo P BE CPX CMAX SYS EN en 0908NH...
Page 23: ...CMAX system overview 1 1 Festo P BE CPX CMAX SYS EN en 0908NH Chapter 1...
Page 31: ...Fitting and pneumatic installation 2 1 Festo P BE CPX CMAX SYS EN en 0908NH Chapter 2...
Page 60: ...2 Fitting and pneumatic installation 2 30 Festo P BE CPX CMAX SYS EN en 0908NH...
Page 61: ...Electrical installation 3 1 Festo P BE CPX CMAX SYS EN en 0908NH Chapter 3...
Page 79: ...Commissioning 4 1 Festo P BE CPX CMAX SYS EN en 0908NH Chapter 4...
Page 122: ...4 Commissioning 4 44 Festo P BE CPX CMAX SYS EN en 0908NH...
Page 123: ...Diagnostics and error handling 5 1 Festo P BE CPX CMAX SYS EN en 0908NH Chapter 5...
Page 163: ...Technical appendix A 1 Festo P BE CPX CMAX SYS EN en 0908NH Appendix A...
Page 176: ...A Technical appendix A 14 Festo P BE CPX CMAX SYS EN en 0908NH...