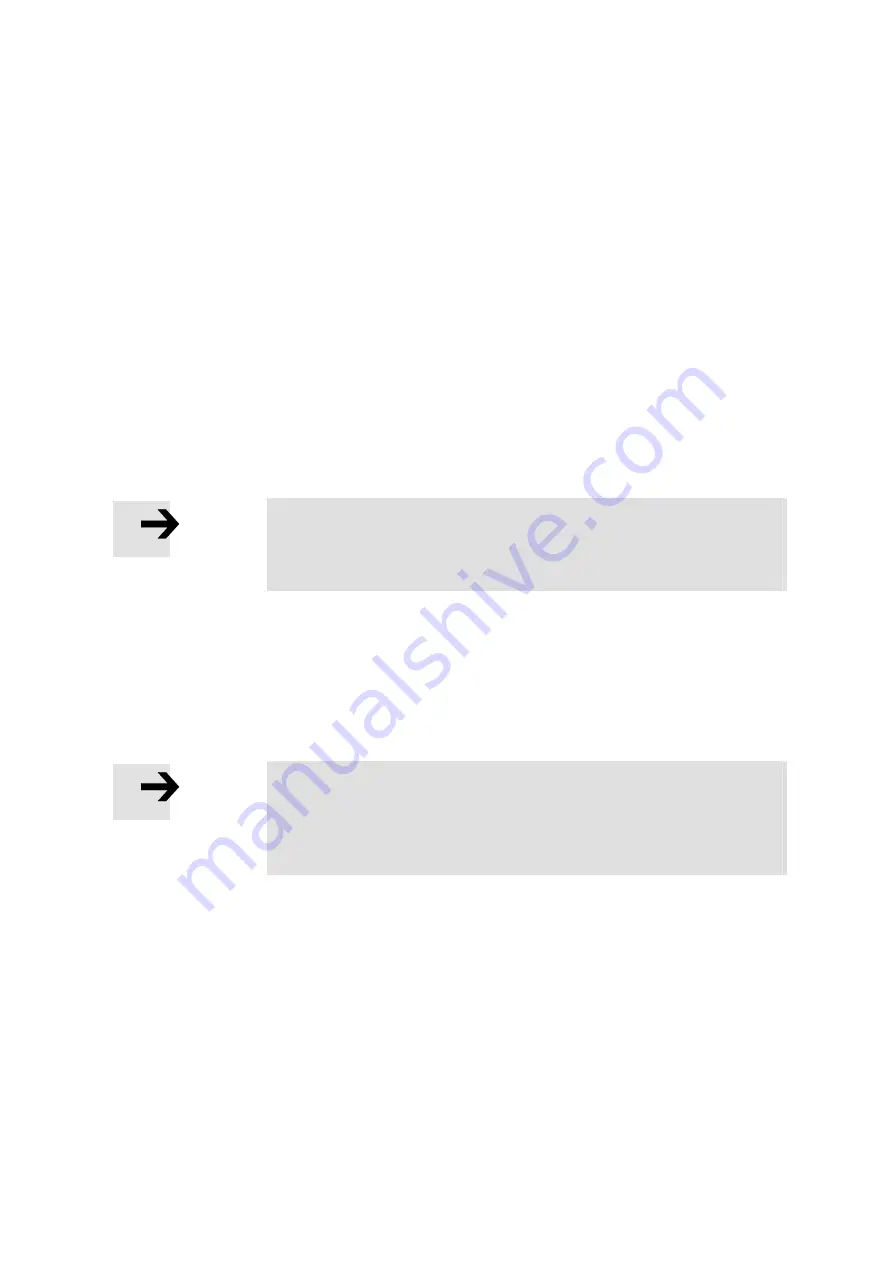
3. Product description
Festo.P.BE-CMMS-ST-G2-HW-EN 1008NH
27
3.3.4
Interfaces for direct synchronous operation
The motor controller permits a master-slave mode, which hereafter is designated
synchronisation. The controller can function either as a master or slave.
If the motor controller works as master, it can provide (RS422) A/B signals to the
increment generator output [X10].
When the motor controller is to operate as a slave, various inputs and signal forms are
available for synchronisation.
[X10] (5V RS422)
A/B, CW/CCW, CLK/DIR
[X1] (24V):
CW/CCW, CLK/DIR.
Using software, the increment generator interface can be configured as both output and
input (master or slave). Additionally, two inputs for the connection of 5V pulse-direction
signals (CLK/DIR), (CW/CCW) are planned on the plug connector.
24 VDC pulse-direction signals are carried out via [X1] DIN2 and DIN3.
Note
5V DC
Pulse-direction signals over [X10] max. 150 kHz
24V DC
Pulse-direction signals over [X1] max. 20 kHz
Output: Generation of increment generator signals [X10]
Based on the encoder data, the motor controller generates the tracking signals A, B as
well as the zero pulse of an increment generator. The number of lines can be set in the
FCT plug-in with values between 32 … 1024. As from FCT plug-in V1.1, values up to 2048
can be set.
Note
For Firmware 1.2.0.1.1:
To avoid rounding errors, the number of lines per revolution should
contain the factor 2
n
. (32, 64 ... ) 1024
Changes to this interface only become effective after a “Reset”.
(download, secure, reset)
An RS422 power driver provides the signals to [X10] differentially.
Input: Processing of frequency signals [X10]
The signals are evaluated optionally as A / B tracking signals of an increment generator or
as pulse / direction signals (CW/CCW or CLK/DIR) of a stepping motor control. The signal
form is selected in the FCT. The number of steps per revolution can be parameterised.
Beyond that, an additional electronic gear can be parameterised.