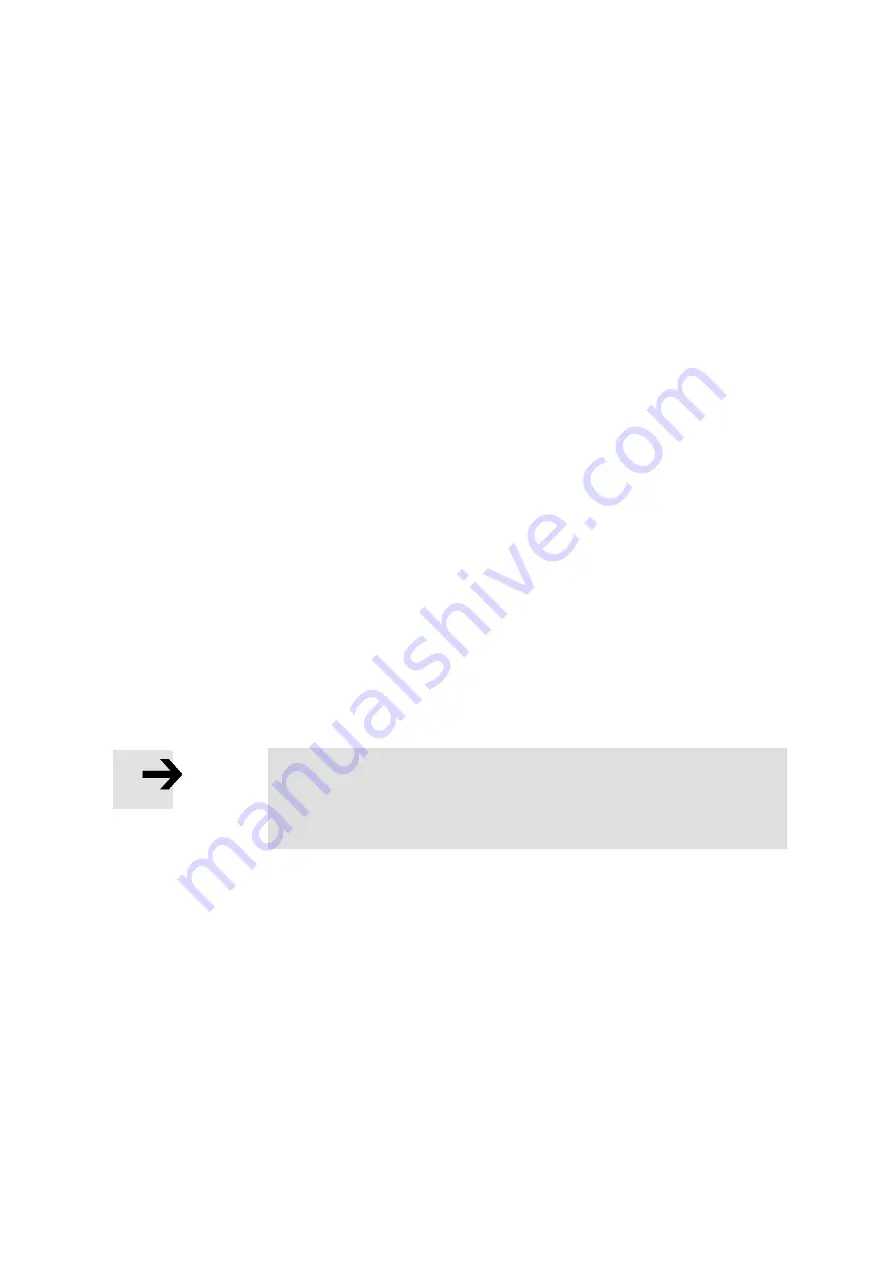
3. Technical specificationsProduct description
Festo.P.BE-CMMS-ST-HW-EN 0903b
39
12.
Command:
=604000:001F
13.
After homing has been ended, the condition of the controller must be reset.
14.
Command:
=604000:000F
Bring controller into "Ready" state.
3.3.7
Multi-firmware strategy
A firmware update can be achieved using any desired customer firmware through the
built-in SD card reader. See chapter 3.3.13 SD memory card.
3.3.8
Incremental sensor input
An optional increment generator mounted on the motor shaft is used to record the actual
speed and position for EMMS-ST series motors. The actual speed is determined based on
the measured rotor position. The rotor position is smoothed via a configurable PT
1
filter.
The position counter for positioning has a data width of 32 bits. The position within a
motor rotation is resolved to max. 16 bits. This results in a maximum possible positioning
range of ±32767 rotations.
3.3.9
Brake chopper
A brake chopper with a braking resistor is integrated in the power output stage. If the
permitted load capacity of the intermediate circuit is exceeded during the energy
recovery, the braking energy may be converted to heat by the internal braking resistor.
The brake chopper is actuated with software control. The internal braking resistor is
protected against overloading via software and hardware.
Note
If the maximum braking energy of the braking resistor is exceeded,
the message "070 – Overvoltage in intermediate circuit" is output
and the end stages switched off.