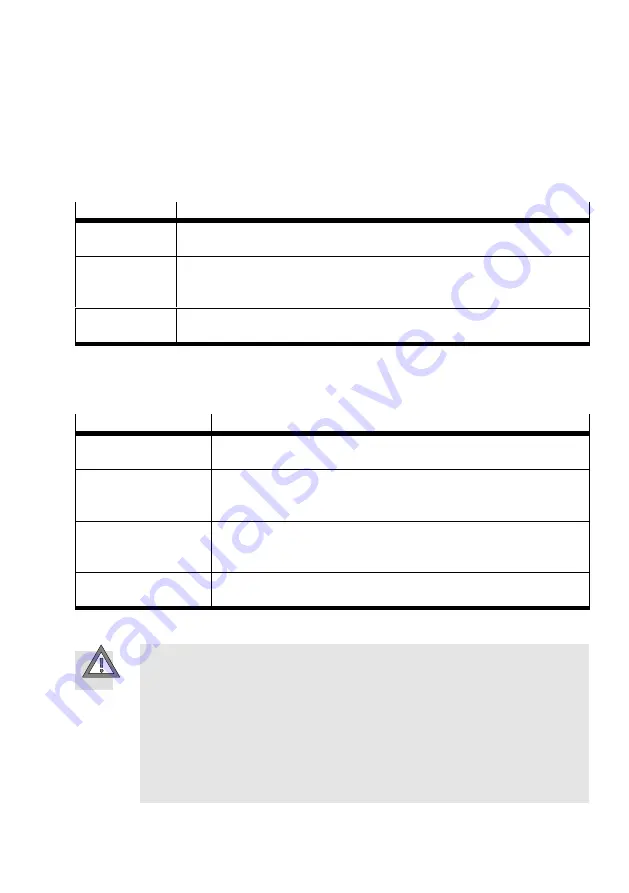
6
Diagnostics
Festo – GDCP-CMMO-ST-EA-SY-EN – 2017-05c – English
125
6.3
Diagnostic messages
6.3.1
Error management
The parameterisable diagnostic messages from the motor controller can be classified with FCT as er
rors, warnings or as information. All diagnostic messages can be parameterised in a way that enables
them to be stored in the diagnostic memory.
Classification
Description
Faults
(Error)
Errors always generate an error response and these must be acknowledged.
Certain errors cannot be acknowledged until their cause has been remedied
Warning
(Warning)
Warnings have no influence on the behaviour of the actuator and do not need to
be acknowledged. The cause of a warning should be eliminated to prevent the
warning from resulting in an error.
information,
(Information)
Information can have an influence on the behaviour of the actuator and do not
need to be acknowledged.
Tab. 6.3
Classifications of diagnostic messages
è
FCT [...][Controller][Error Management]
Error responses can be assigned to some of the errors that influence the stop characteristics and sub
sequent disconnection of the output stage:
Error response
Description
Free run-out
(Free-weeling)
The output stage is switched off. The drive gradually comes to a
standstill.
Quick stop deceleration
(QS deceleration)
The movement is stopped immediately with the parameterised quick-stop
deceleration function. There is the option of shutting down the output
stage.
Satz-Verzögerung
(Deceleration record)
The movement is stopped immediately with the current record for
parameterised deceleration. There is the option of shutting down the
output stage.
End record
(Finish record)
The current set is performed until the target is met (Motion Complete).
There is the option of shutting down the output stage.
Tab. 6.4
Error response
Caution
Injuries as a result of automatic movement of the passive actuators as a result of error
responses that shut down the output stage
During installation of the actuator in an inclined or vertical position, falling loads!
Secure loads through external safety measures (e.g. toothed pawls or moved pivot
pins). This especially applies to vertical axes without automatic locking mechanics,
clamping units or counterbalancing.
Prevent movement of the passive motor in particular with suspended loads or other
external forces, e.g. with a holding brake.