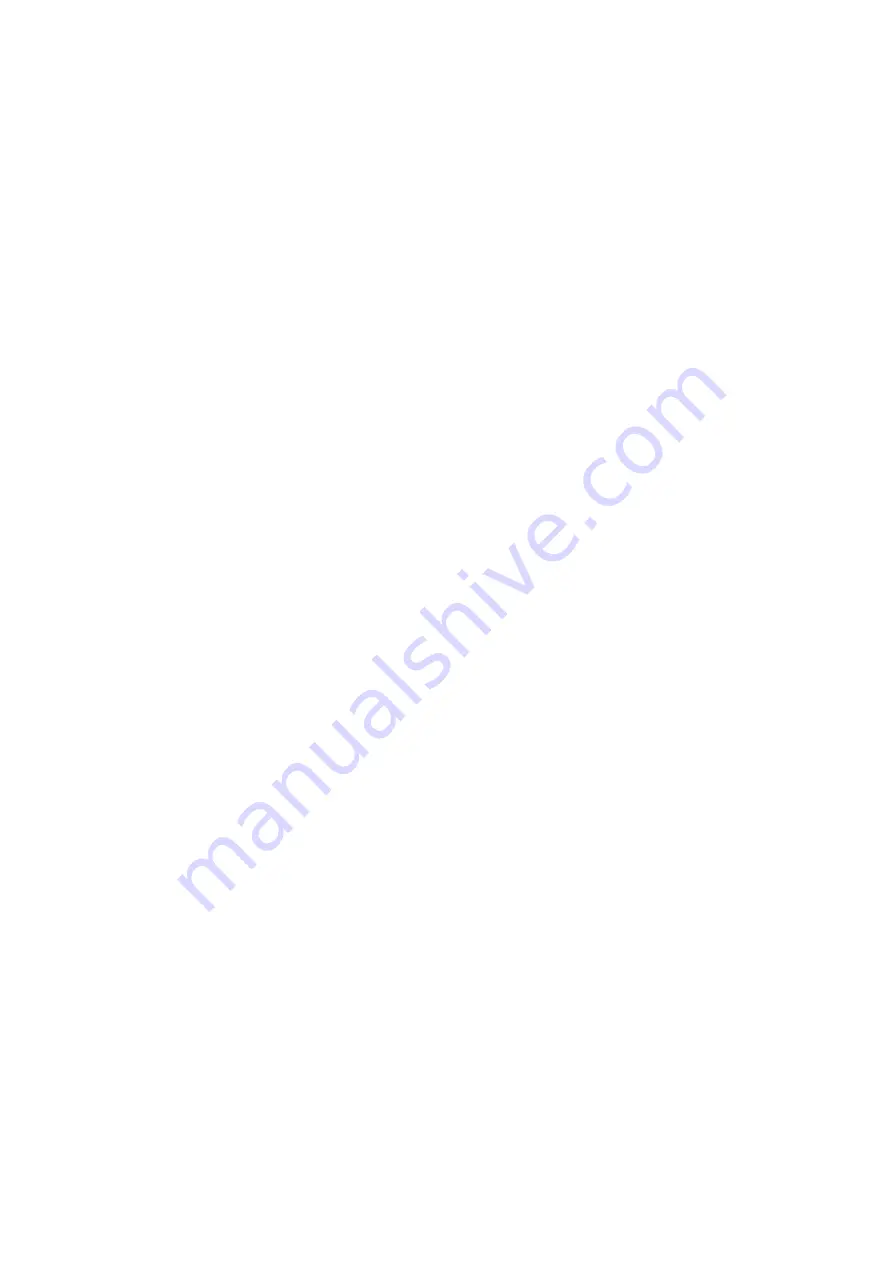
31
There are also certain requirements to the relative positions of two main shafts of conditioner
during the installation. Installation can be carried out according to signs at the shaft end and can also
be done by the qualifies technicians via self-choosing corresponding position.
4.2.4 Installation of the pipeline system
Determine the installation location for pipeline system, preferably not too far away from the
principal machine. A distance too far will cause waste of connection material of pipelines and also
control delay.
Allowed by the fieldconditions, the optimum location of pipeline system is over by and parallel to
the rear side of the principal machine & conditioner, with a sure space about 1m at each side of the
pipeline system to allocate a certain maintenance room at both sides of the pipeline rack.
During installation, ensure that the joint of conditioner steam line on the pipeline system is at the
same side as the steam inlet of conditioner. For the sake of floor cleaning and waste water discharge
in the future, the installation position of pipeline valves should meet the requirements of handy
operation.
(1) Water addition into extruder barrel and conditioner
Water addition to the extruder barrel and conditioner is directly for the materials, which is closely
related to the quality of the expanded products. Therefore, water addition at these two places shall be
controlled quantitatively. Fig.4-6 provides a simplified drawing of water to the extruder barrel and
conditioner. The parts and components inside of the dotted square frame have been included in the
equipment shipment while those outside of the dotted square frame shall be provided and installed by
customer. Parts and components prepared by customer are: water tank, ball valve, strainer, water
pump and pipe connection fittings, etc.
Requirements to purchase and installation are as follows:
Water tank: Water tank prepared by customer shall be of a volume larger than or equal to 1.5m
3
.
It’s better to install a floating ball type automatic water supply device to ensure no water supply break.
A drainage outlet shall be set on the water tank.
Strainer and main water-supply pipeline: specification of water pipe is DN25 in stainless steel.
Water return pipe: specification DN15;
Water pump: Pump head is required within 70~105m with flow rate of about 3t/h. A multistage
pump or a "vortex type boiler feedwater pump " of Model 1.5DB2-0.7AZ is recommended;
Make the connections of all pipelines secure, good looking without leakage, and easy for
maintenance.