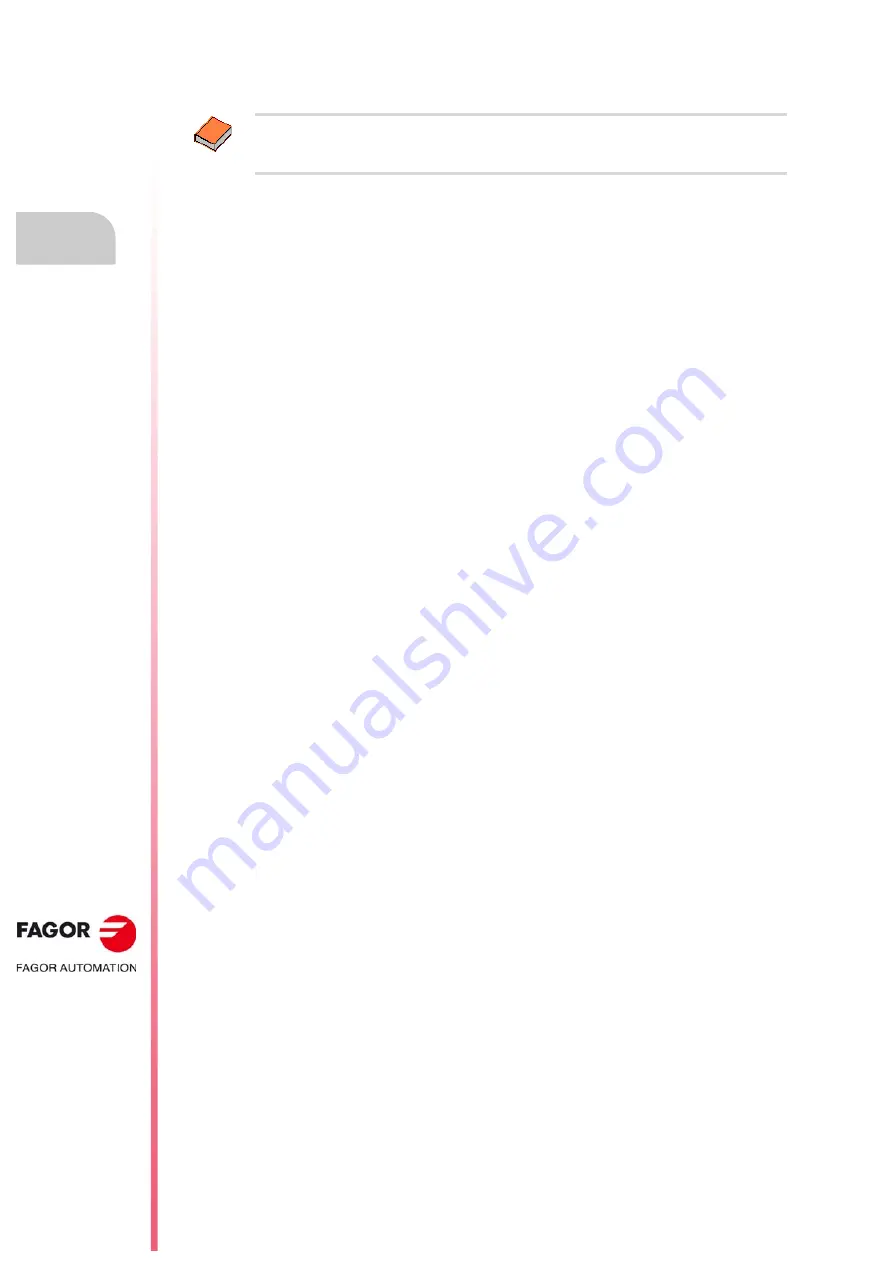
Programming manual.
CNC 8070
22.
STATEMENTS AN
D INSTRUCTIONS
Pro
g
ramming statements
·424·
(R
EF
: 1709)
22.1.20 Movements of independent axes
The CNC has the possibility of executing independent positioning and synchronization. For
this type of movements, each CNC axis has an independent interpolator that keeps track
of the current position on its own without depending on the tracking of the general interpolator
of the CNC.
It is possible to execute an independent movement and general movement simultaneously.
The result will be the sum of the two interpolators.
The CNC stores up to a maximum of two independent-motion instructions per axis. The rest
of instructions sent when there are two pending execution imply a wait from the part-program.
Treatment of a rotary axis as an infinite axis.
Axis synchronization permits treating a rotary axis as an infinite axis making it possible to
increase the feedback count of the axis indefinitely (without limits) regardless of the value
of the module. This type of axis is activated when programming by adding the prefix ACCU
to the name of the master axis. From the moment this is programmed, the CNC uses the
variable V.A.ACCUDIST.xn that may be initialized at any time to follow up on the axis.
This feature is useful, for example, for a rotary axis or encoder that moves an endless
conveyor belt on where the part is. The infinite axis treatment allows synchronizing the
coordinate of the conveyor belt with an external event and, this way, count the moving
distance of the part beyond the value of the module of the rotary axis that moves the belt.
Restrictions for the independent axes
Any axis of the channel may be moved independently using the associated instructions.
However, this function presents the following restrictions.
• A spindle can only move independently when set in axis mode with the instruction
#CAX
. However, it can always be the master of a synchronization.
• A rotary axis may be of any module, but the lower limit must always be zero.
• A Hirth axis cannot move independently.
Synchronizing the interpolators
In order for the incremental movements to take the real coordinate of the machine into
account, each interpolator must be synchronized with that real coordinate. The
synchronization is done from the part-program using the instruction
#SYNC POS
.
Resetting the CNC synchronizes the theoretical coordinates of both interpolators with the
real coordinate. These synchronizations will only be necessary when inserting instructions
of both types of interpolators.
Every time the program is initiated or an MDI block is executed, the coordinate of the general
interpolator of the CNC is synchronized and every new independent instruction (without any
one pending) also synchronizes the coordinate of the independent interpolator.
Influence of the movements in block preparation
None of these blocks interrupt block preparation, but they do interrupt the interpolation.
Therefore, it will not blend two blocks, there will be an intermediate one.
This function has a specific manual. This manual that you are reading now only offers some information
about this function. Refer to the specific documentation to obtain further information regarding the
requirements and operation of the independent axes.
Summary of Contents for 8070 BL
Page 1: ... Ref 1709 8070 CNC Programming manual ...
Page 8: ...BLANK PAGE 8 ...
Page 12: ...BLANK PAGE 12 ...
Page 14: ...BLANK PAGE 14 ...
Page 26: ...BLANK PAGE 26 ...
Page 28: ...BLANK PAGE 28 ...
Page 30: ...BLANK PAGE 30 ...
Page 60: ...Programming manual CNC 8070 2 MACHINE OVERVIEW Home search 60 REF 1709 ...
Page 72: ...Programming manual CNC 8070 3 COORDINATE SYSTEM Coordinate programming 72 REF 1709 ...
Page 96: ...Programming manual CNC 8070 5 ORIGIN SELECTION Polar origin preset G30 96 REF 1709 ...
Page 178: ...Programming manual CNC 8070 9 TOOL PATH CONTROL MANUAL INTERVENTION Variables 178 REF 1709 ...
Page 304: ...Programming manual CNC 8070 16 C AXIS Machining of the turning side of the part 304 REF 1709 ...
Page 442: ...Programming manual CNC 8070 23 CNC VARIABLES 442 REF 1709 ...
Page 443: ...Programming manual CNC 8070 443 User notes REF 1709 ...