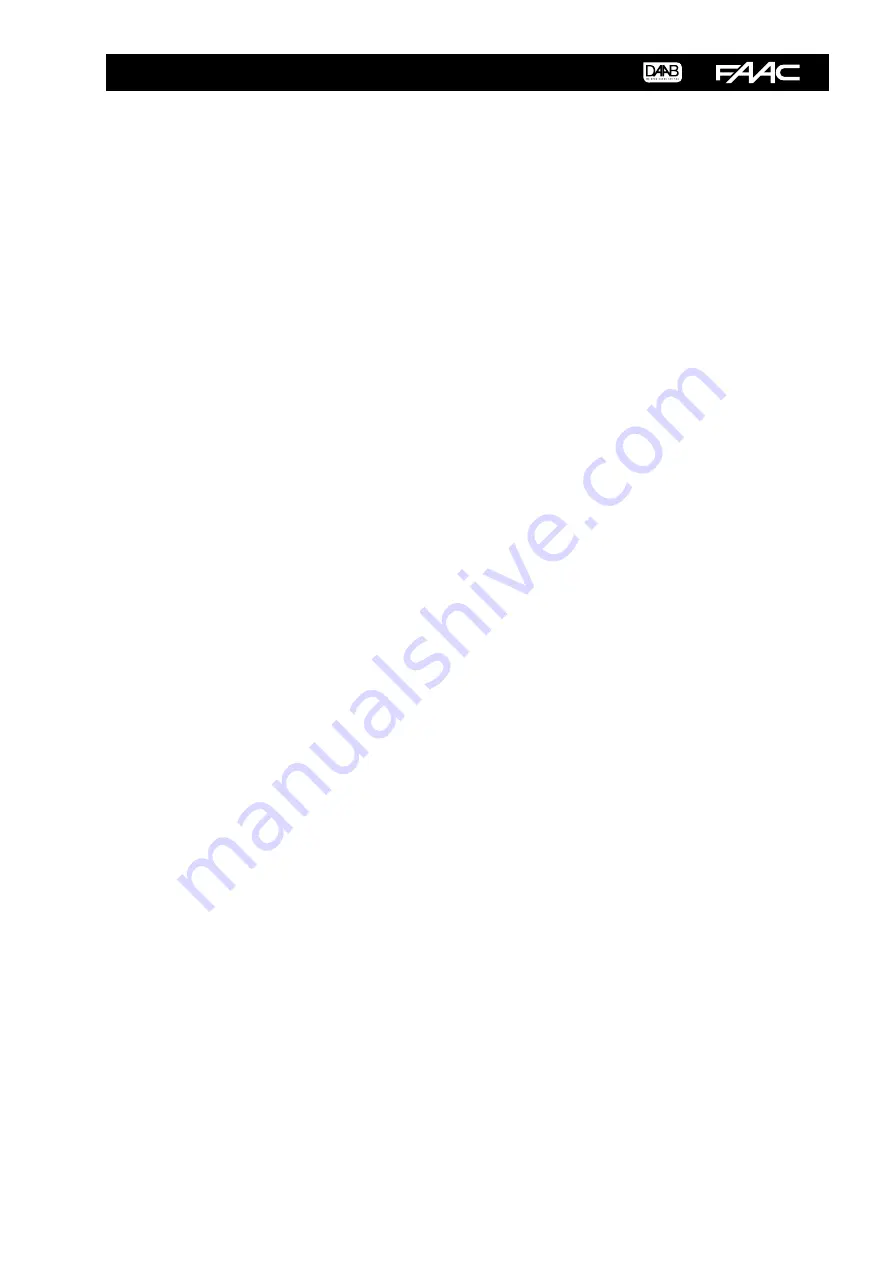
21
Instruction manual version 1 for software version 4.04
INSTRUCTION MANUAL FOR DAAB EP104 CONTROL BOARD
•
Set the value as the closed position in channel L113 for motor 1 and L123 for motor 2.
•
Run the motor (hold-to-run) to the fully open position.
•
Read the value in L111 for motor 1 and L121 for motor 2 and enter the respective values in L112 for motor 1 and
L122 for motor 2.
•
The limit switches are now configured and the motors will stop at the specified degrees. Note that some fine tuning
may be necessary depending on the type of the door and if there is motor slippage.
Mechanical limit switches (microswitches)
If conventional mechanical limit switches are used, the unit is configured as follows.
•
Set channel L001 to option 2 for mechanical limit switch.
•
Set channel L002 to option 2 for mechanical limit switch if there are two motors.
•
Adjust the limit switch ridges so they match the open and closed position of the door. The easiest way to do this is to
move the door to the end position and adjust the ridge to it activates the limit switch.
•
Fine adjustment is possible using the run-on times in channels C421, C422, C431 and C432.
Timer control (without limit switches)
Motor winders without a limit switch can use timer control instead. With timer control, you measure the actual opening
time of the door and set the automatic control unit to operate the motors for that length of time. The configure the unit for
timer control, use the following channel settings.
•
Set L001 to 3 for timer control.
•
Set L002 to 3 for timer control if there are two motors.
•
Run the motor (hold-to-run) to the fully closed position, then run the motor to the fully open position.
•
Read channel L211 for motor 1 and make a note of the value.
•
Read channel L221 for motor 2 (if there is one) and make a note of the value.
•
Set a time that is 20% longer than the time in channel L212 for motor 1 and L222 for motor 2.
• Direction of rotation of motors
To reduce the risk of injury or damage, the door must be decoupled during commissioning.
Check that the motor is running in the right direction by pressing the open and close buttons on the automatic control unit.
If the direction of rotation is wrong, change the phase sequence of the motor, see "Connection – high current".
• Setting the internal motor protection
Read the current consumption of each motor during hold-to-run operation – from channel C251 for motor 1 and C261 for
motor 2 – then set the motor current in channels C252 and C253 for motor 1 and channels C262 and C263 for motor 2. A
value of 0.0 means that the motor protection will not be tested – the intention is to use external contactors.
• Type of power supply
Only change this setting in high current installations with no neutral or a single-phase power supply.
Check that the correct type is installed using the value in channel C202.
The initial setting is 0, which means a supply voltage of N+PE. For other options, see the channel reference.
Checking the phase sequence for 3x230 V without neutral
If there is no neutral, the load guard takes two phases as reference points, so the phase sequence must be correct.
To check that the phase sequence is correct, decouple the motor winder to allow the motor to run without load. With the
motor running, read the value in channel C271 for motor 1 and C281 for motor 2 – the value should be about 0.20. If the
phase sequence is incorrect, the value is about 0.95 and the load guard is activated.
See "Connection – high current" to find out how to correct an incorrect phase sequence.
Summary of Contents for DAAB EP104
Page 74: ......