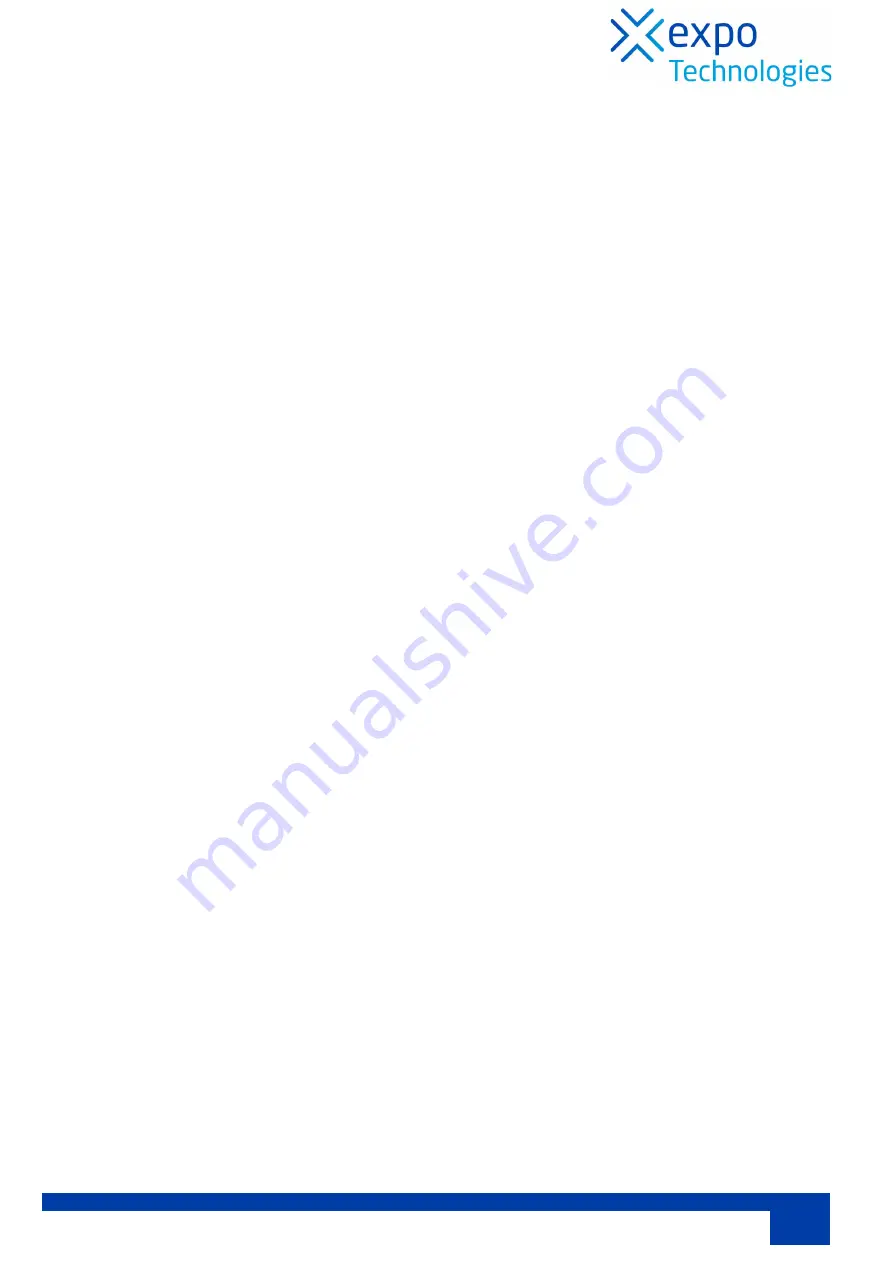
ML548_ES | v3
Page
12
Expo Technologies UK
T: +44 (0) 20 8398 8011
E: [email protected]
Expo Technologies US
T: +1 (440) 247 5314
E:[email protected]
Expo Technologies China
T: +86 532 8906 9858
E: [email protected]
Before connection of the air supply to the purge system, the supply pipe work should
be flushed through with instrument quality air to remove any debris that may remain in the pipes. This must
be carried out for at least 10 seconds for every meter of supply pipe.
Unless a supply shut-off valve has been fitted to the MiniPurge
®
system, an external shut-off valve with the
same, or larger, thread size as the Control Unit inlet fitting should be fitted by the installer to prevent any
restriction of purge flow.
The purge air from the MiniPurge
®
Control Unit should be piped within the pressurized enclosure to ensure
purging of potential dead air spots.
The purge system is fitted with an internal regulator factory set to 4 bar feeding the logic.
Pipe Work
If the MiniPurge
®
is not connected directly to the pressurized enclosure, pipe work and fittings used to connect
the Control Unit to the pressurized enclosure should be either metallic or appropriate to the environment into
which the system is installed. No valve may be fitted in any signal pipe connecting the Control Unit to the
pressurized enclosure. This pipe work must be fitted in accordance with local codes of practice where relevant.
Multiple Enclosures
This system is suitable for the purge and pressurization of the primary pressurized enclosure and its
associated terminal boxes.
Provision and Installation of Alarm Devices
When the pressure inside the pressurized enclosure is above the minimum, the Minimum Pressure Sensor re-
turns a positive (
pressurized
) signal causing the alarm indicator on the control unit to change from
red
to
green
.
When the pressure falls below the minimum permissible the positive (
pressurized
) signal is removed. This ab-
sence of signal indicates a
low pressure alarm
condition and causes the alarm indicator on the control unit
to go from
green
to
red
.
There are volt free (dry) contacts available within the terminal box for remote usage.
The user must make use of this alarm facility in accordance with the local code of practice for Action on Pres-
sure or Flow Failure. Most codes include the following recommendations:
•
Zone 1 Installations:
Alarm and Automatic Trip of Power.
•
Zone 2 Installations:
Alarm Only on pressure or flow failure with power being removed manually.
Power Supplies and their Isolation
All power entering the pressurized enclosure should have a means of isolation. This requirement also applies
to any external power sources that are connected to the equipment such as volt-free (dry) contacts within the
pressurized enclosure. This is commonly achieved using the Power Interlock Switch.
Power Interlock Switch
This switch is a Double Pole Normally Open, double-break switch: it provides two independent contacts that
should be connected in series and used to isolate the power. This can be achieved using switchgear or other
suitable switching device. These contacts are terminated and accessible to the user in the Ex e terminal box.
It is the responsibility of the user to ensure that the switch is only operated within appropriate technical limits.
The switch must be replaced after any short circuit that occurs within the main circuit; the switch is a piece of
encapsulated equipment and as such it is not possible to check the state of the contacts. Technical
modifications to the switch are not permitted.