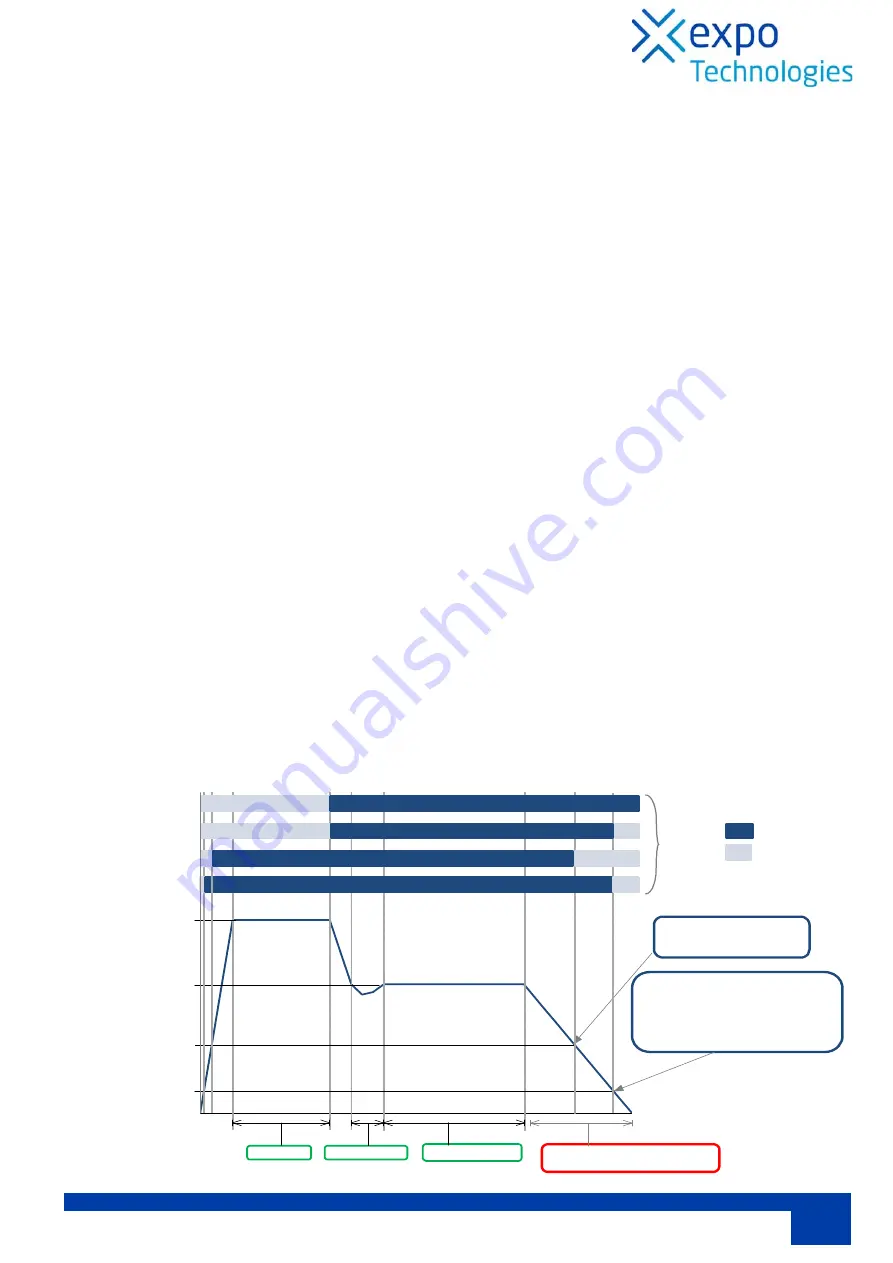
ML434_ES | v11
Page
6
Expo Technologies UK
T: +44 (0) 20 8398 8011
E: [email protected]
Expo Technologies US
T: +1 (440) 247 5314
E:[email protected]
Expo Technologies China
T: +86 532 8906 9858
E: [email protected]
Section 4: Description and Principle of Operation
The MiniPurge
®
system is pneumatic in operation, with electrical interfaces.
Purge and pressurization is a method of protection used in Zone 1 (21) and/or Zone 2 (22) hazardous locations
to ensure that the interior of an enclosure is free of flammable gas. Addition of a MiniPurge
®
system allows
the electrical equipment within the enclosure to be used safely in a hazardous location.
The principle of purge and pressurization is as follows:
• Clean compressed air or inert gas is drawn from a non-hazardous location.
• The interior of the pressurized enclosure is flushed to remove any hazardous gas or dust.
• This is introduced into the pressurized enclosure to keep the internal pressure at least 0.5 mbarg above the
external pressure.
• Whilst pressurized, flammable gas cannot enter the enclosure from the environment.
Prior to switching on the power to the electrical equipment, the enclosure must be purged to remove any
flammable gas that might have entered the enclosure before pressurization. Purging is the process of removal
contaminated air and replacement with air (or inert gas) known to be free from flammable gas. The duration
of this purge process is normally ascertained by performing a purge test.
At the end of the purge cycle the system automatically switches to leakage compensation mode. The Purge
Outlet Valve is closed and the airflow is reduced but remains high enough to compensate for the leakage of
air from the enclosure whilst maintaining the minimum over pressure state.
In the event of pressure failure within the pressurized enclosure the system will raise an alarm in the form of
visual indicators and a volt free contact depending on the specification of the system. The default action on
loss of pressurization is alarm and automatic disconnect of power (A&T - Alarm and Trip). This can be changed
by the customer to Alarm Only (/AO), please refer to section titled Main Components.
The MiniPurge
®
system incorporates a Closed Loop Automatic Pressurization System (CLAPS). This allows the
system to detect a rise or fall of the enclosure’s internal pressure and adjust the leakage compensation rate
accordingly. Pressure variations are more likely during sudden start up of large rotating electrical machines but
can also be caused by changes in running temperature. This system has been specifically designed to maintain
a stable internal pressure within the enclosure.
Pressure characteristics during purge and pressurization of a pressurized enclosure using a MiniPurge
®
system
that incorporates a CLAPS system:
Intermediate Pressure
Sensor Pressure
Power Interlock switch
Alarm &Trip
Purge Time
Machinery Start
Normal Operation
CLAPS Regulator
Pressure
Intermediate switch contacts
open. Intermediate sensor
sends falling pressure signal
Fault Condition - loss of pressure
outside of CLAPS regulation
Minimum Pressure
Sensor Pressure
Purging Pressure
Minimum pressure switch contacts
open. Minimum pressure sensor sends
a low pressure signal.
Alarm indicator shows red (alarm only)
Alarm indicator shows red and power
is disconnected (Alarm and Trip)
Minimum
pressure switch
Intermediate
pressure switch
Power Interlock switch
Alarm Only
Contacts
Active
Inactive