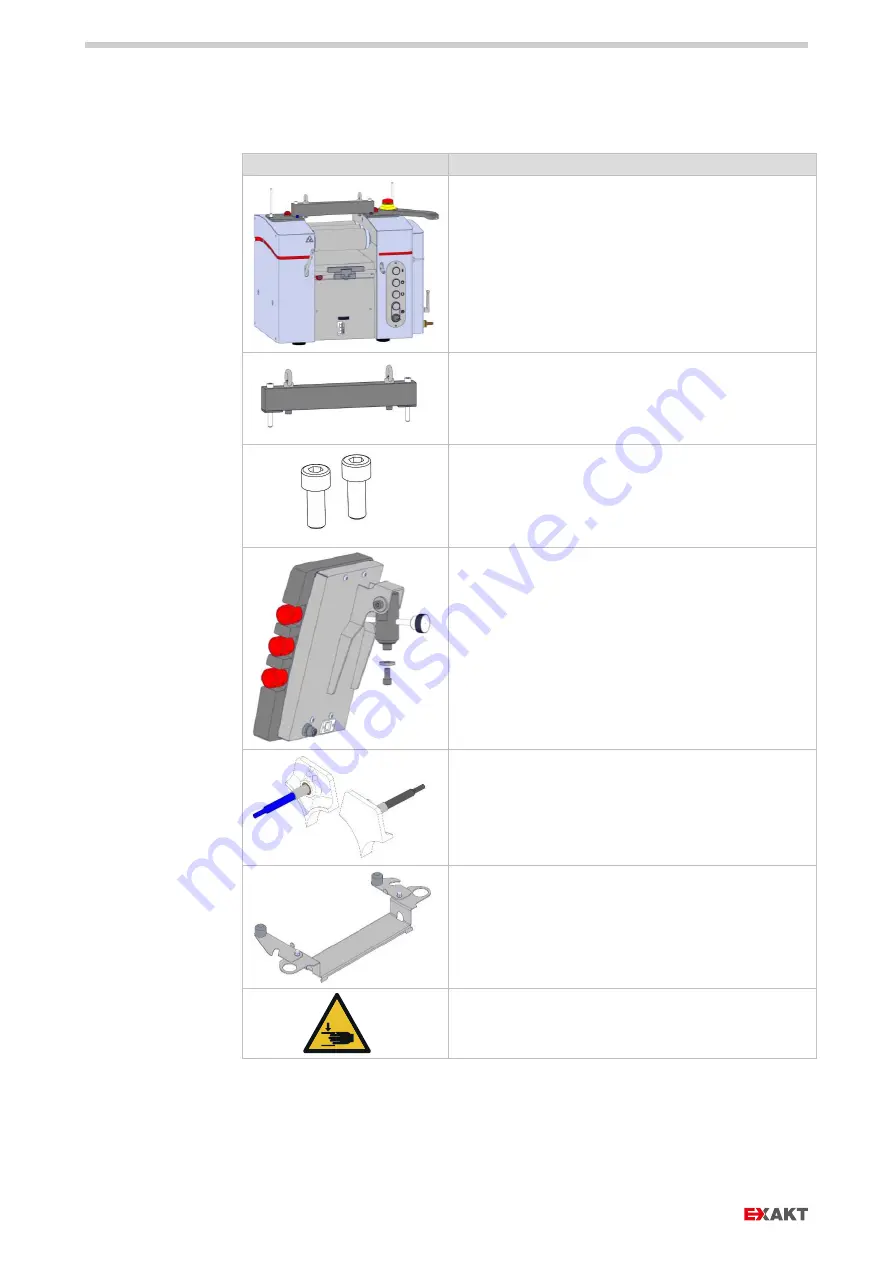
Unit description
44
Edition 09/2016
7.11. SCOPE OF DELIVERY
Symbol
Meaning
Base unit
(
roller material: either
- hard chrome plated steel
- tungsten carbide coated steel
- aluminum oxide
- silicon carbide
Load traverse (installed for delivery)
(To lift the machine and to secure it in the
transport box).
Keep lifting gear after installation!
Socket head screws M8x20
(are required after removing the load traverse,
see chapter
9.2
Dismounting the load traverse).
Operating unit with holder
Plastic guides (at customer's option)
Cleaning guard
Safety device nip gap, various - at customer's
option, but at least one