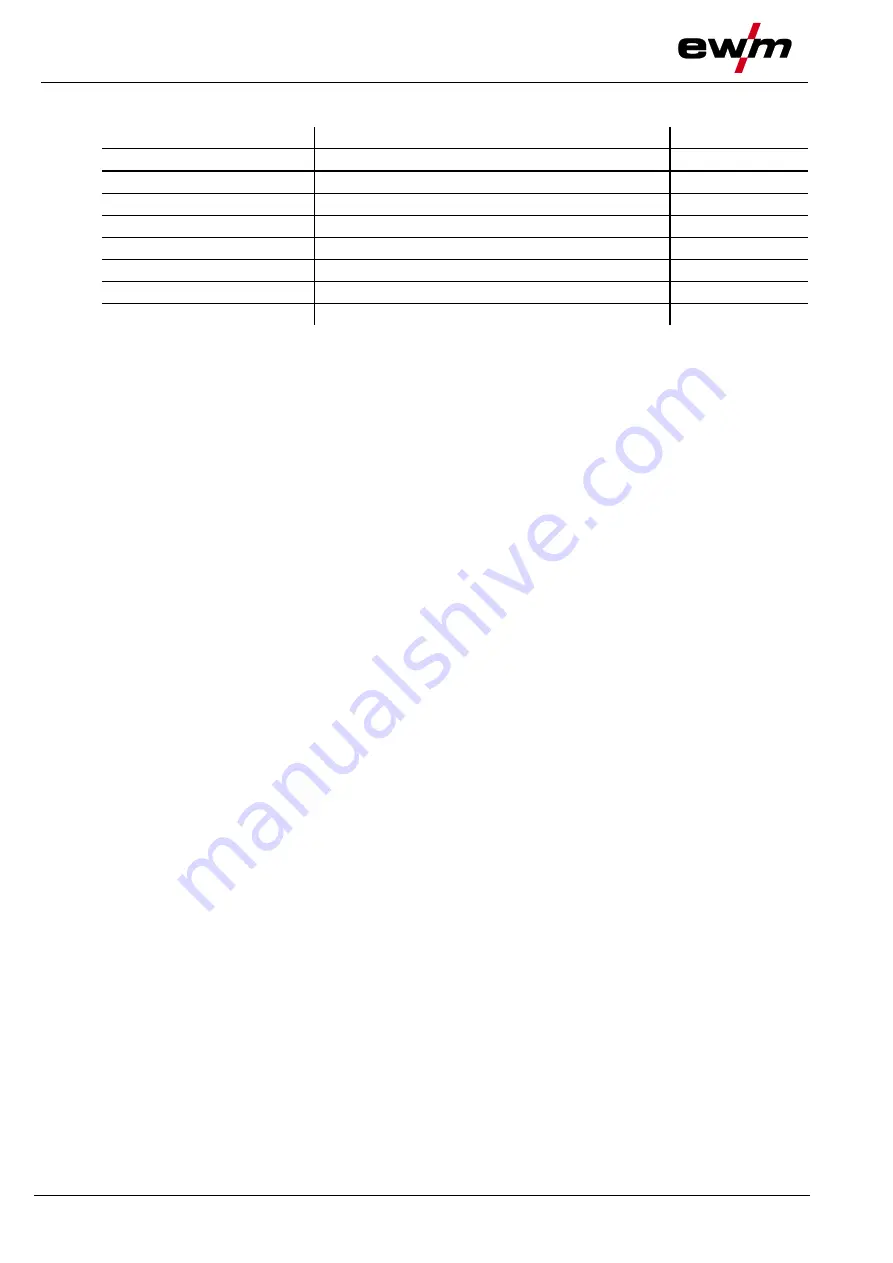
Accessories
General accessories
72
099-005542-EW501
24.03.2020
9.5 General accessories
Type
Designation
Item no.
AK300
Wire spool adapter K300
094-001803-00001
CA D200
Centering adapter for 5-kg spools
094-011803-00000
16A 5POLE/CEE
Mains plug
094-000712-00000
DM 842 Ar/CO2 230bar 30l D Pressure regulator with manometer
394-002910-00030
G1 G1/4 R 3M
Gas hose
094-000010-00003
DSP
Sharpener for liner
094-010427-00000
Cutter
Hose cutter
094-016585-00000
voltConverter 230/400
Voltage converter
090-008800-00502