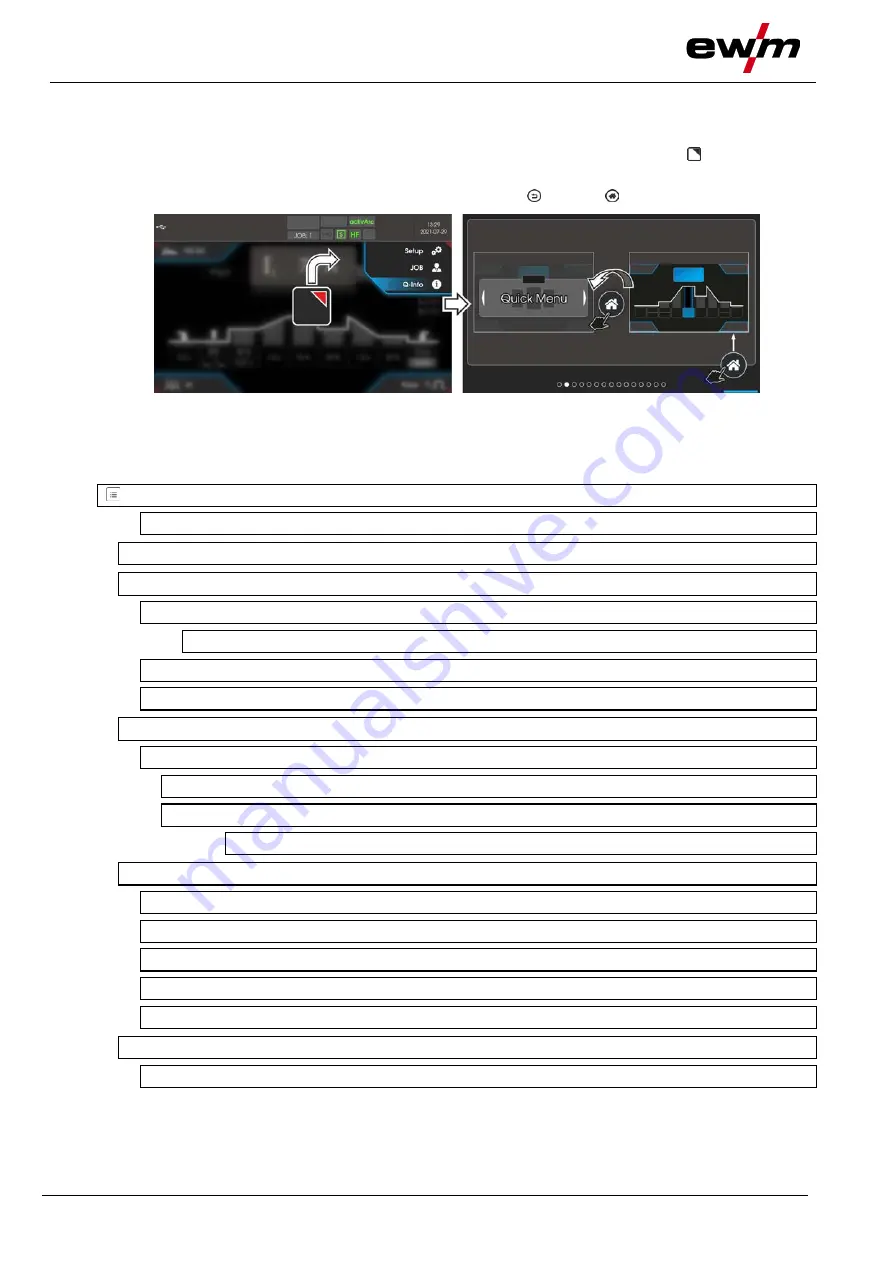
Quick overview
Operator assistance (Q-info)
24
099-00L200-EW501
13.05.2022
4.6 Operator assistance (Q-info)
The graphic user interface provides basic control functions to help guide the user. The sub-menu Q-Info
is located in the Advanced settings menu and can be selected with the push-button OR .
By turning the control button, the different information screens can be navigated.
You can exit the Q
‑
Info menu by pressing the pushbutton Back or Home .
Figure 4-10
4.7 System (main menu)
4.7.1 System information
System information
Errors
> see 7.2 chapter
Warnings
> see 7.1 chapter
Running time
Operating time (resettable)
Arc time (resettable)
Operating time (overall)
Arc time (overall)
System components
ID 4: Expert 3.0
Open-source licenses
Firmware licenses
Change history
Temperatures
Housing inside
Secondary transformer
Secondary heat sink
Coolant return
Primary heatsink
Sensors
Coolant flow