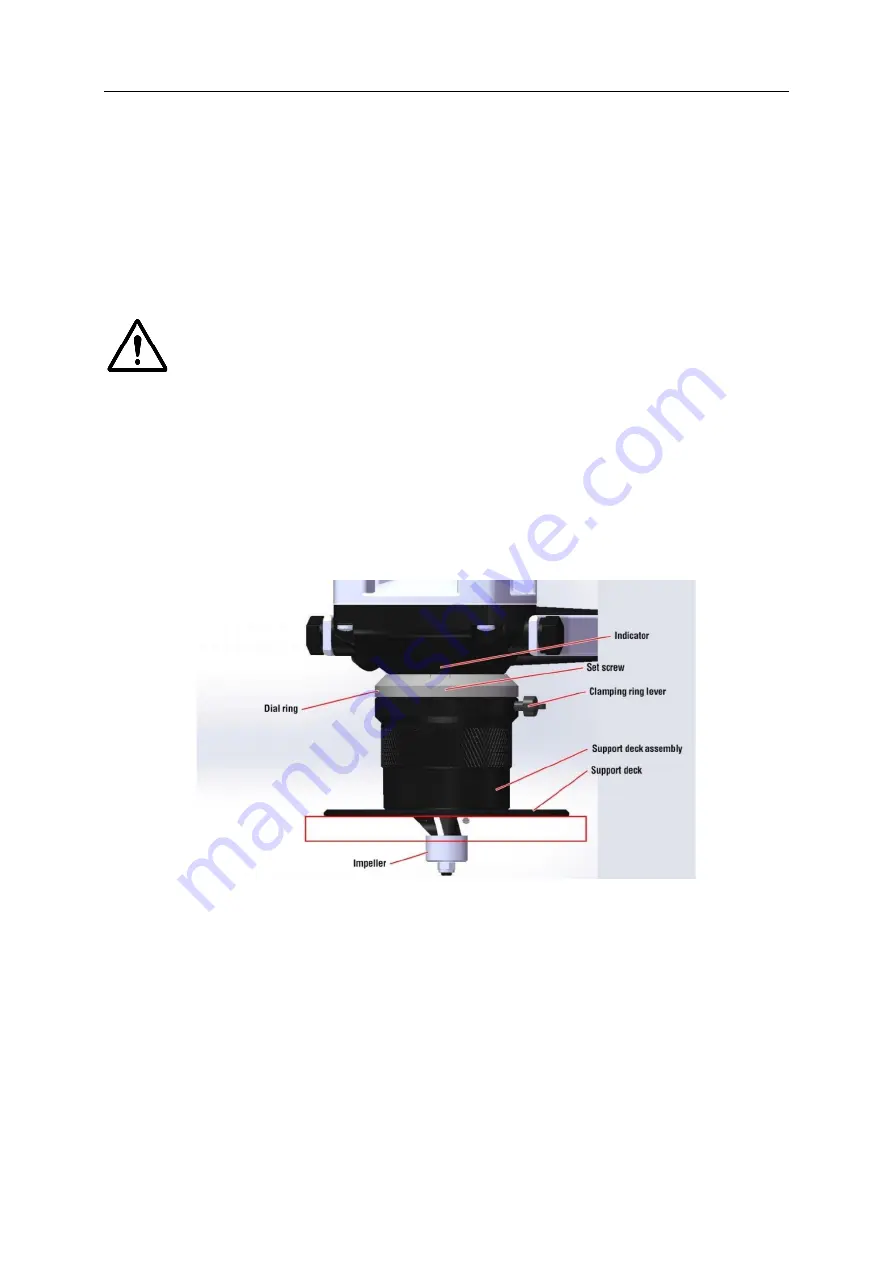
www.euroboor.com
16
3. Preparation & adjustment
3.1 Assembly
WARNING:
To reduce the risk of injury, turn machine off and disconnect from power source
before installing and removing accessories, before adjusting or changing set- ups or when
making repairs. An accidental start-up can cause injury.
Setting bevel depth at zero position
The machine’
s bevel depth is set and delivered at position zero. If the setting is disturbed, the zero
position has to be set again.
[image 2-1]
1.
Loosen the clamping ring lever.
2.
Loosen the support deck assembly until the inserts are below flush level. Keep a steel ruler
square on both the impeller and the support deck.
3.
Slowly adjust the support deck until it touches the cutting plate. This is the zero position.
4.
Lock the clamping ring lever.
5.
Untighten the set screw in the dial ring.
6.
Rotate the dial ring until the zero matches the indicator on the machine.
7.
Retighten the set screw in the dial ring.