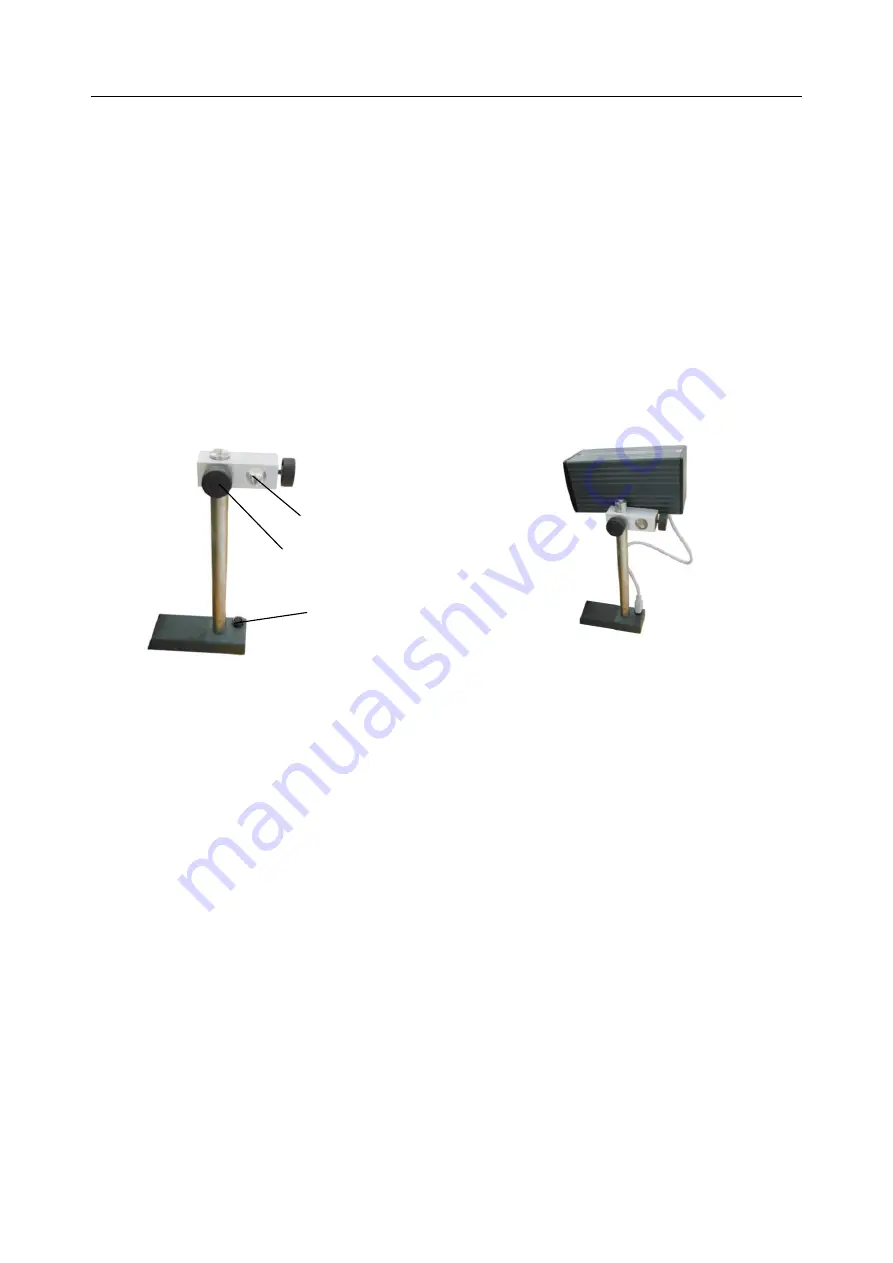
BGA ETA-H15 OPERATION MANUAL
Page5
6. Install and Connect System
6.1 Place System
*
Unwrap the packing of the unit, then take out BGA ETA-H15 Main Unit and put it on the horizontal
worktable.
6.2
Install RPC
1. Unscrew RPC Fixing Knob on the RPC Fixing Bracket and install RPC in the Bracket, tighten knob.
2. Put the plug of RPC connecting wire into Camera Socket.
3. RPC’s position can be adjusted. Unscrew fixing knob in corresponding direction and then adjust. RPC can
be moved up and down or turned.
6.3 System Connecting
*
* Please check whether the supply voltage accords with the rated voltage on the system nameplate.
* Please check whether all switches are turned off.
* Connect the video cord of outside Indicator or Monitor to the VIDEO-OUT socket.
* Connect IR camera
(
RPC
)
to IR camera socket.
* Connect control box to socket.
* Connect ground line to ground hole.
After all above steps, insert power plug into power sockets, and turn on switch.
Install RPC herein.
RPC Fixing Knob
RPC Fixing Bracket
Camera
Socket
RPC
(Reflow Process Camera)
Summary of Contents for BGA ETA-H15
Page 2: ......