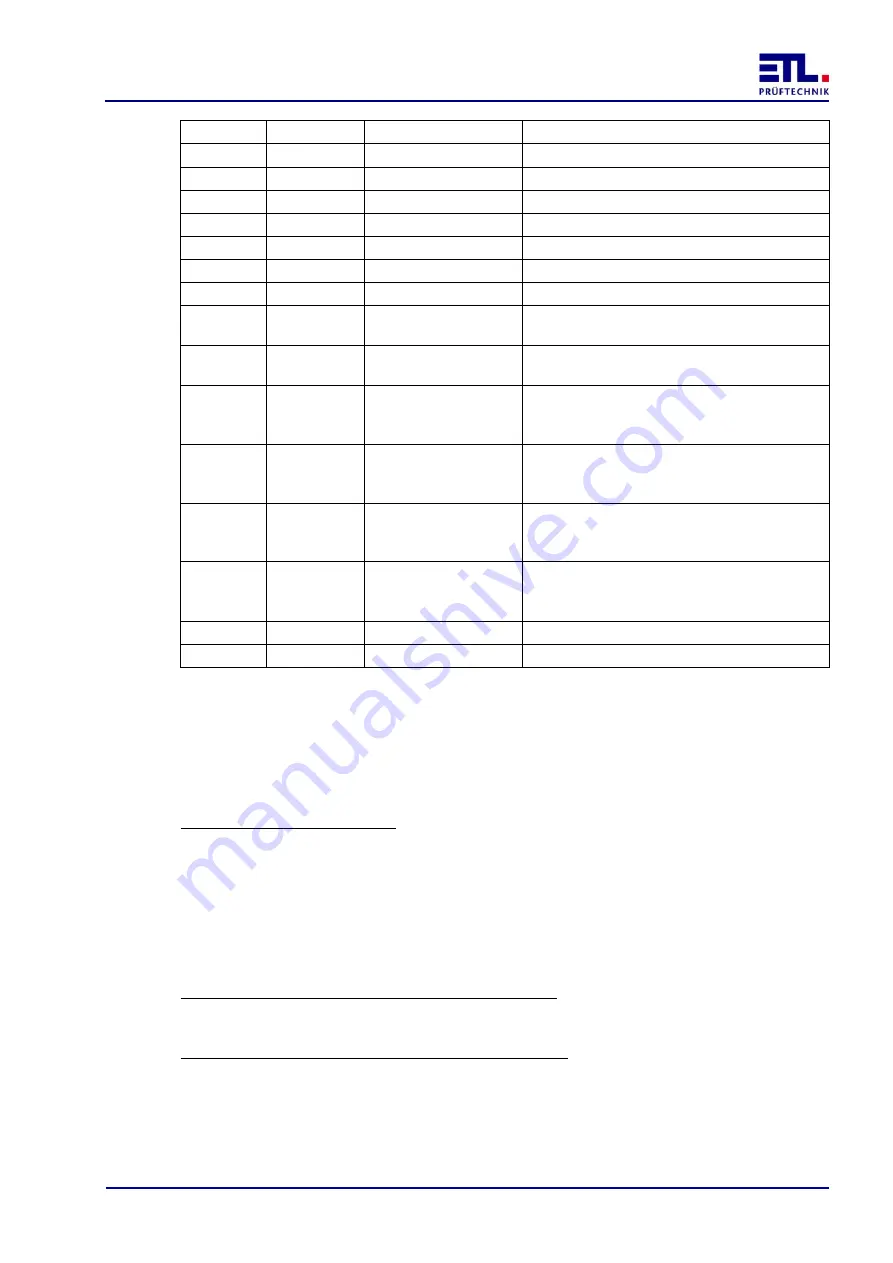
About the Test System
Instruction Manual ATS 400 with SC-NG
Version 4.03
18
PIN
IN/OUT
Designation
Explanation
1
+ 2,5 V
9
+ 5 V
2
GND
10
IN
AD1, AD-Channel 1
0 - 10 V DC, 12 bit resolution
3
IN
AD2, AD-Channel 2
0 - 10 V DC, 12 bit resolution
11
IN
AD3, AD-Channel 3
0 - 10 V DC, 12 bit resolution
4
IN
AD4, AD-Channel 4
0 - 10 V DC, 12 bit resolution
12
OUT
DA1, DA-Channel 1
0 - 10 V DC, analogue output of test
statistics during the test
5
OUT
DA2, DA-Channel 2
0 - 10 V DC, analogue output of test
statistics during the test
13
IN
FREQ 1.0
Frequency input for rotational speed
acquisitation
sensor 1
6
IN
FREQ 1.1
Frequency input for rotational direction
acquisitation
sensor 1
14
IN
FREQ 2.0
Frequency input for rotational speed
acquisitation
sensor 2
7
IN
FREQ 2.1
Frequency input for rotational direction
acquisitation
sensor 2
15
GND
8
IN 3
+ 24 V DC
4.3.5
RS232-Interface
The serial interface RS232 can be used in connection with a commercially available
PC, a log printer (ASCII or tape printer) or a PLC.
The interface is executed as a 9-pole SUB-D plug (male). The exact specification of
the connectivity options are described in the following chapters:
4.3.5.1
PC-Connection via KWP2000
The particularly interference free and data safe connection between PC and test
system is realized via the Keyword Protocol 2000 (KWP 2000).
Matching drivers (LabVIEW, DLL) as well as the complete data management system
ETL DataView 3
are available and described in their separate instruction manuals.
A commercially available null-modem cable is used for the electric connection
between a PC and the test system.
4.3.5.2
Log Printer-Connection via a simple ASCII-Output
Protocol is not implemented yet!
4.3.5.3
PC- or PLC-Connection via a simple ASCII-Protocoll
This is an option available as article 205060.
4.3.6
CAN 1: Interface for the Extension of the Test System
System extensions of the standard test system are realized via the CAN 1-Interface.
So e.g. an external relay matrix can be operated by the test system with a high