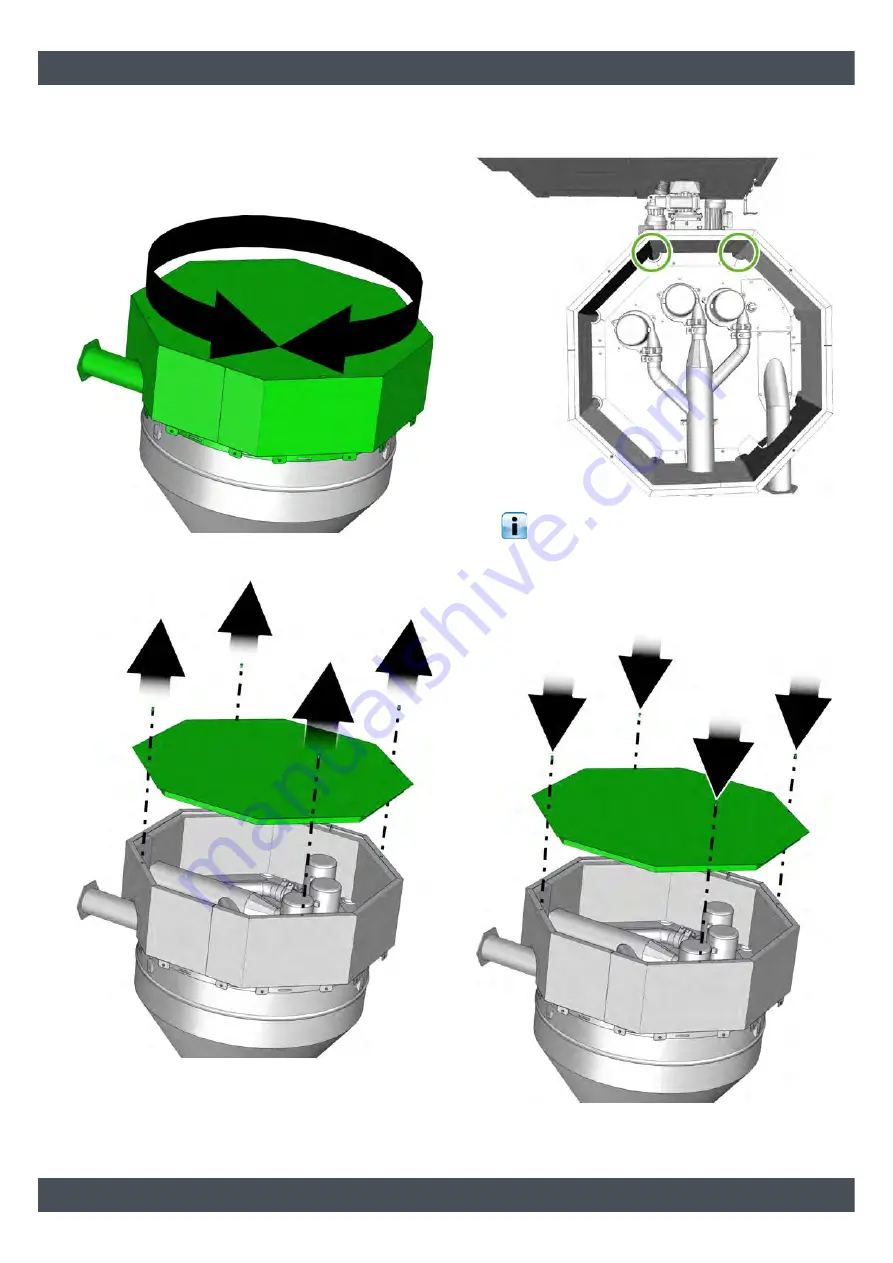
Installation
Installing the suction compartment
17
8.5
Installing the suction
compartment
1. Turn the cover in 45° steps to align the suction
connection and return connection.
2. Remove the 4 M5 x 10 screws from the top of the
cover and remove the panel.
3. Connect the cables for the aspirator and the fill
level sensor with the appropriate extensions.
Find the shortest way to the [HE-C2] circuit
board and run the connection cables
downwards through this opening to the circuit
board.
4. Mount the panel with 4 M5 x 10 screws to the top
of the cover.
Summary of Contents for HACK 130-200
Page 23: ...Configuration Installing a configuration 23 ...
Page 42: ...42 www eta co at Appendix 15 Appendix ...
Page 46: ...www eta co at ...
Page 47: ......
Page 48: ...www eta co at ...