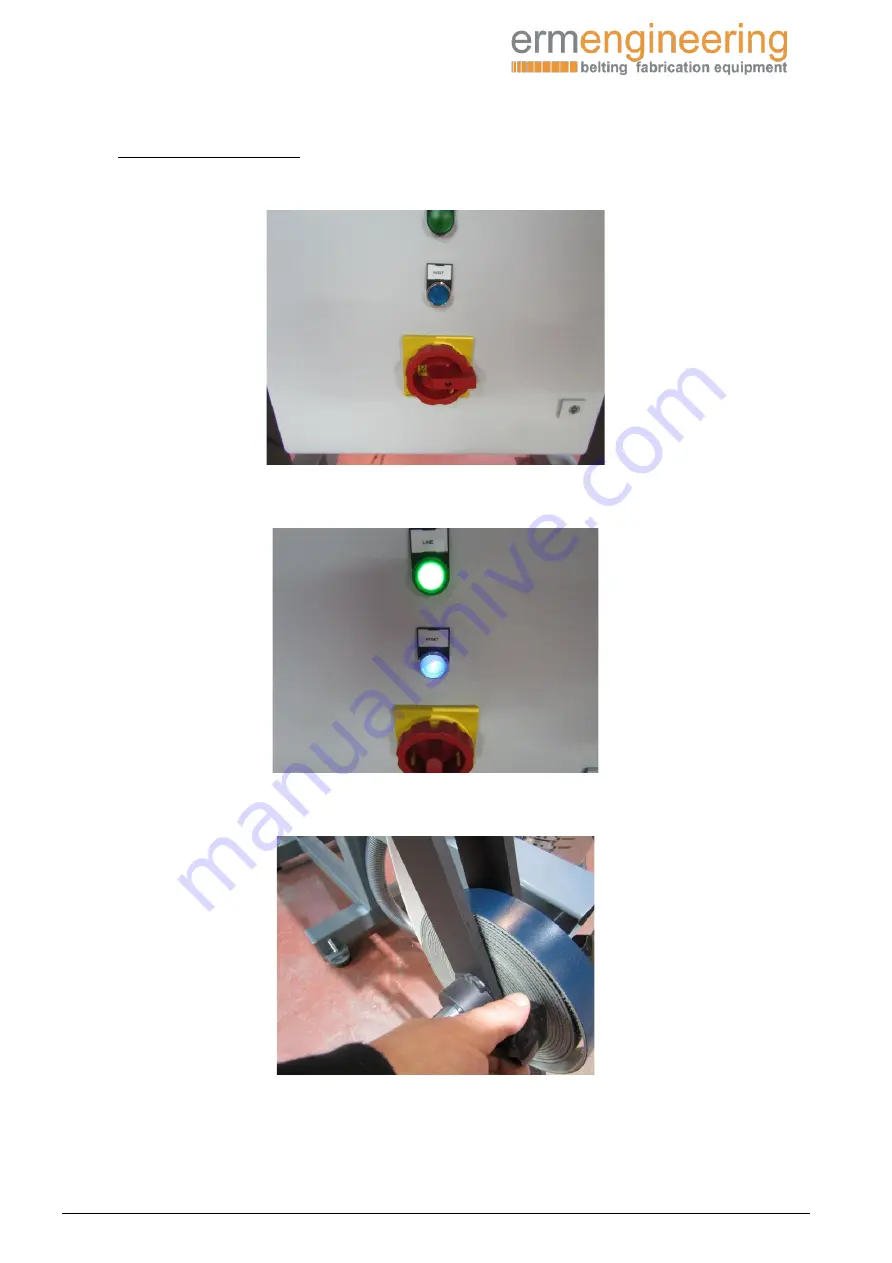
Use and maintenance manual
Longitudinal profile welding
Model: LRWG-100
_______________________________________________________________________________________________________________________
P a g . 7
-
Using instructions:
Turn on the control box using the general circuit breaker:
After turning on, restart the machine pressing the blue button RESET:
Load the slab in the back shaft and fix the guides:
Pass the belt across the table, pulling up the grinder protection until welding pulley: