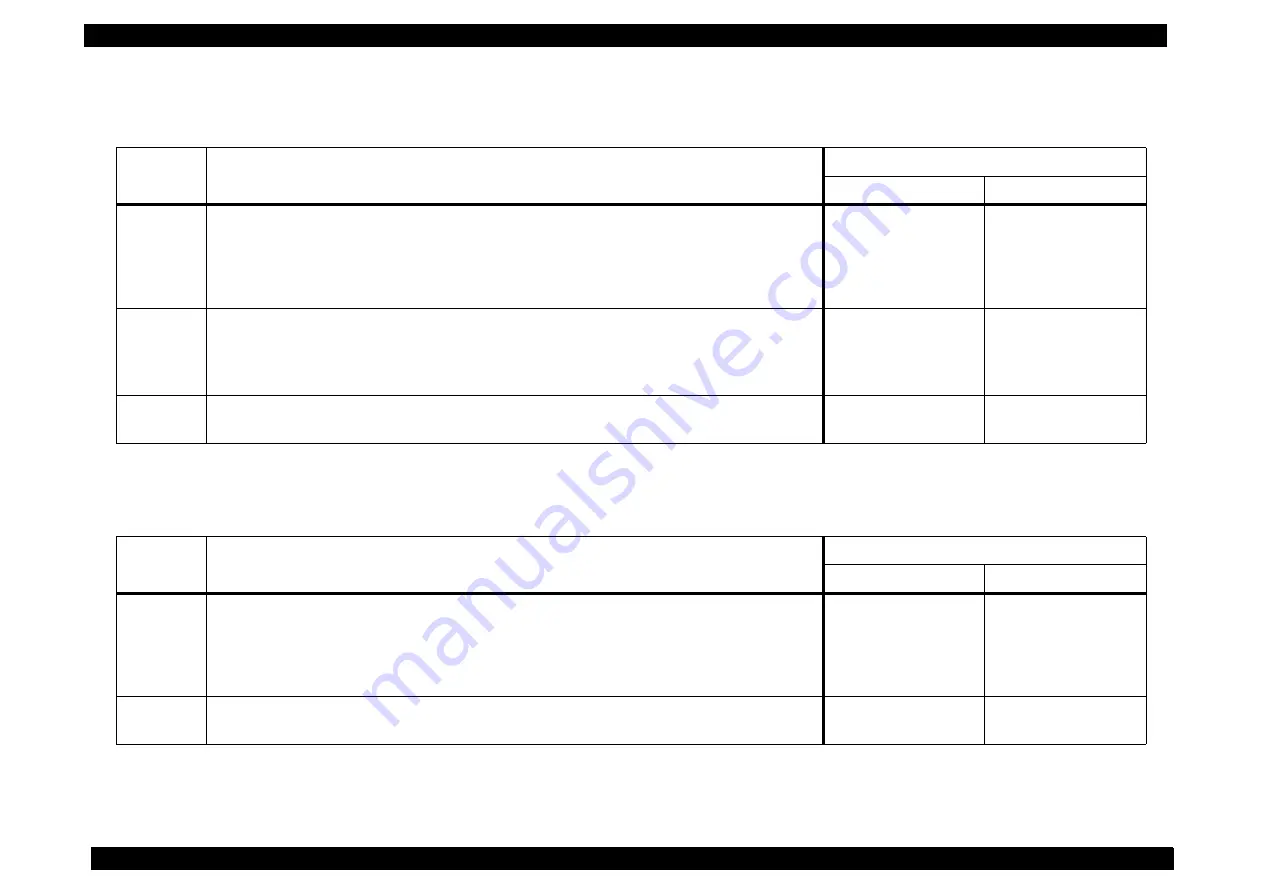
EPSON AcuLaser C8500
Revision C
Troubleshooting
Level 1 FIP (Fault Isolation Procedure)
5-78
FIP-1.51 CONTROLLER PWB-Related to Other Hardware Errors
FIP-1.51 CONTROLLER PWB-Related to Other Hardware Errors
FIP-1.51 CONTROLLER PWB-Related to Other Hardware Errors
FIP-1.51 CONTROLLER PWB-Related to Other Hardware Errors
FIP-1.52 SRAM (IC 25) Initialization Error
FIP-1.52 SRAM (IC 25) Initialization Error
FIP-1.52 SRAM (IC 25) Initialization Error
FIP-1.52 SRAM (IC 25) Initialization Error
Step
Check
Treatment
Yes
No
1
*Initial setting
• Remove all of the option units related to electricity and modules.
Bring everything back to normal status.
• Check if all connectors are properly connected to the CONTROLLER PWB.
• Re-insert the DIMM.
Replace and remount
the concerned part(s).
Go to step 2.
2
*MCU PWB initialization
• By using the Diag Command, execute “Slave Initialize”.
• Turn the power on and off.
• Does the printer operate properly?
Problem solved.
Go to step 3.
3
*Related unit Replacement
Replace the CONTROLLER PWB.
Replace and remount
the concerned part(s).
Problem solved.
Step
Check
Treatment
Yes
No
1
*Initial setting
• Remove all of the option units related to electricity and modules.
Bring everything back to normal status.
• Check if all connectors are properly connected to the CONTROLLER PWB.
• Re-insert the DIMM.
Replace and remount
the concerned part(s).
Go to step 2.
2
*Related unit Replacement
Replace the CONTROLLER PWB.
Replace and remount
the concerned part(s).
Problem solved.
Summary of Contents for AcuLaser C8500
Page 12: ......
Page 21: ...C H A P T E R 1 PRODUCTDESCRIPTIONS ...
Page 78: ...C H A P T E R 2 OPERATINGPRINCIPLES ...
Page 108: ...EPSON AcuLaser C8500 Revision C Operating Principles 2 31 Figure 2 38 Xerographics II ...
Page 110: ...EPSON AcuLaser C8500 Revision C Operating Principles 2 33 Figure 2 39 Development ...
Page 118: ...EPSON AcuLaser C8500 Revision C Operating Principles 2 41 Figure 2 45 Drive ...
Page 120: ...EPSON AcuLaser C8500 Revision C Operating Principles 2 43 Figure 2 46 Electrical ...
Page 153: ...C H A P T E R 3 DISASSEMBLY ASSEMBLY ADJUSTMENT ...
Page 269: ...C H A P T E R 4 DIAGNOSTICS ...
Page 353: ...C H A P T E R 5 TROUBLESHOOTING ...
Page 480: ...C H A P T E R 6 MAINTENANCE ...
Page 503: ...C H A P T E R 7 APPENDIX ...
Page 564: ......
Page 565: ......
Page 566: ......
Page 567: ......
Page 568: ......
Page 569: ......
Page 570: ......