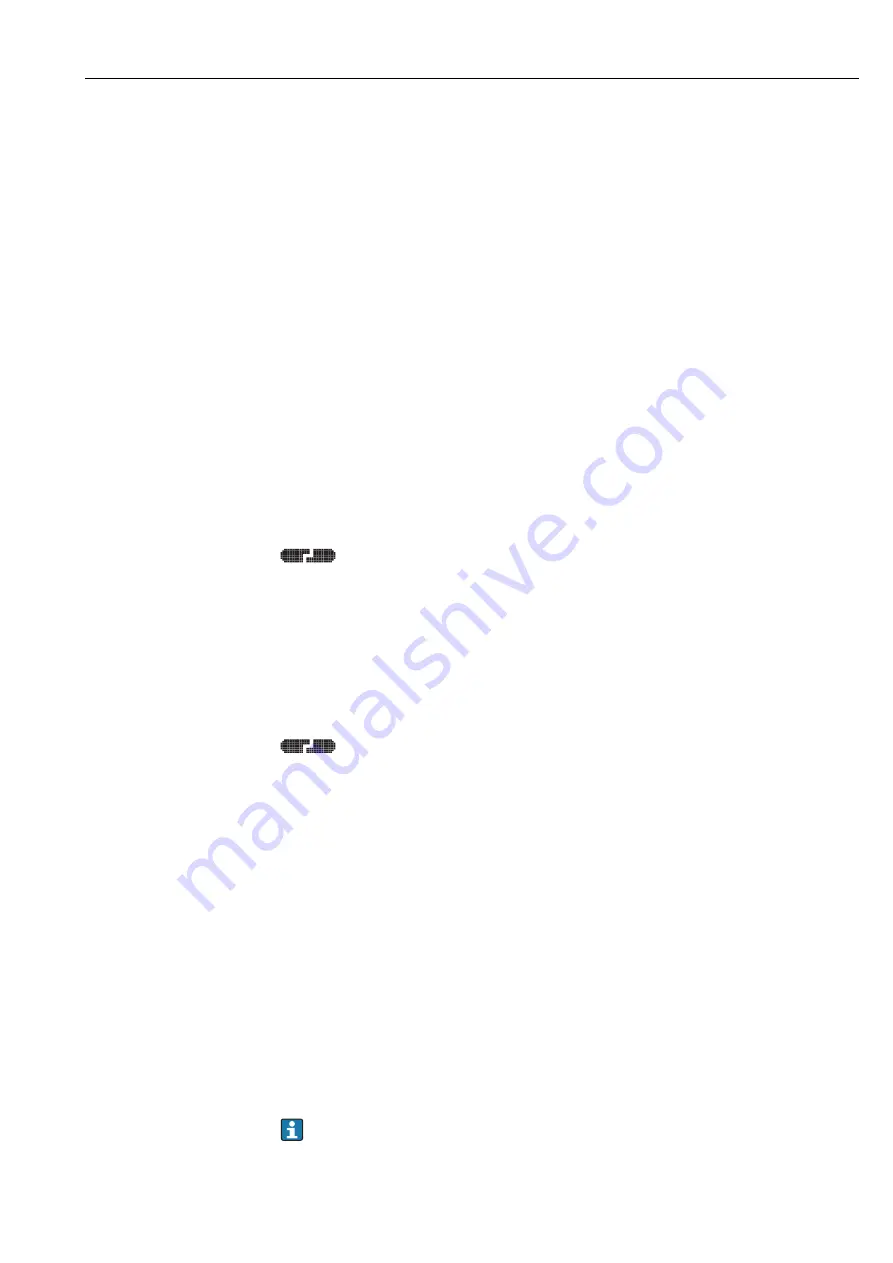
Prosonic S FMU95 PROFIBUS DP
Diagnostics and troubleshooting
Hauser
63
10.2 Overview of diagnostic information
10.2.1 Error signal
Displaying errors that occur during commissioning or operation:
•
Local display
:
• Error symbol
• Error code
• Error description
•
Cyclic data telegram
Status that is transmitted with the measured value.
•
Operating menu
:
System informat. → Error list → Actual error
10.2.2 List of the last errors
Operating menu
:
System informat. → Error list → Last error
10.2.3 Types of error
Alarm (A)
lit permanently.
The value of the output signal is defined by the
Output on alarm → Output N
parameter:
•
Min
: –10 %
•
Max
: 110 %
•
Hold
: the last value is held.
•
User specific
: defined in the
Output value N
parameter.
The status of the output value of the affected AI blocks is BAD.
Warning (W)
flashes.
• The device continues to measure.
• The operating status LED flashes red.
• An error message is displayed.
• The status of the output value of the affected AI blocks is UNCERTAIN.
10.2.4 Influence of errors on the status byte of the output signal
The following table indicates which status the block output values adopt when an error
occurs. There are three possible status values: GOOD, UNCERTAIN and BAD. The status is
passed on to the next block. If several status values coincide, the stronger value overwrites
the weaker value according to the following order:
• BAD overwrites UNCERTAIN and GOOD.
• UNCERTAIN overwrites GOOD.
• GOOD does not overwrite any other status.
Therefore the strongest status value is supplied to the AI Block output. This status value is
transmitted to the PLC along with the measured value.
Error in the Sensor Block (US N)
Each Sensor Block (US N) has two outputs: one for the measured distance D, and one
for the sensor temperature T.