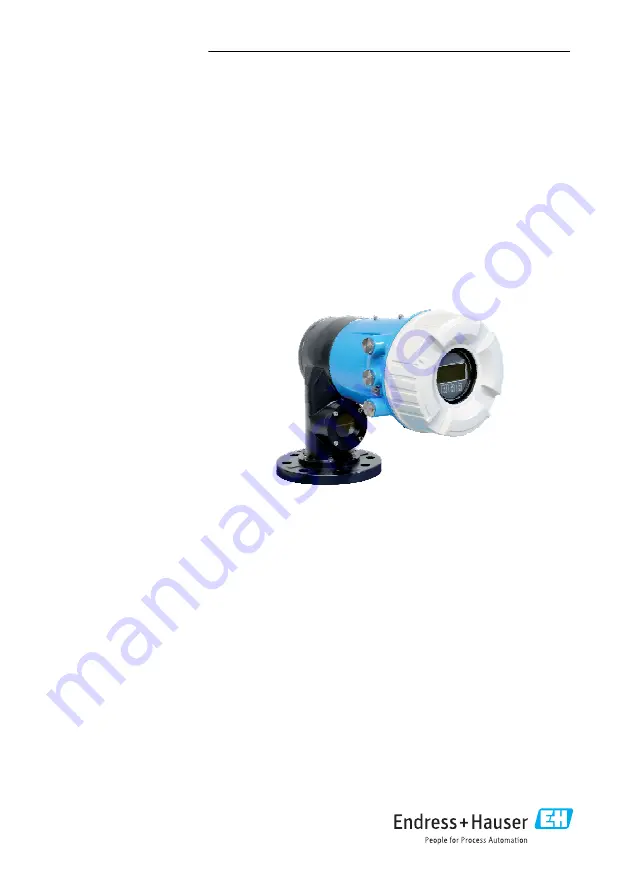
Products
Solutions
Services
Brief Operating Instructions
Proservo NMS80
Tank Gauging
These Instructions are Brief Operating Instructions; they are
not a substitute for the Operating Instructions pertaining to
the device.
Detailed information about the device can be found in the
Operating Instructions and the other documentation:
Available for all device versions via:
• Smart phone/tablet:
Hauser Operations App
KA01200G/00/EN/05.22-00
71593767
2022-11-10