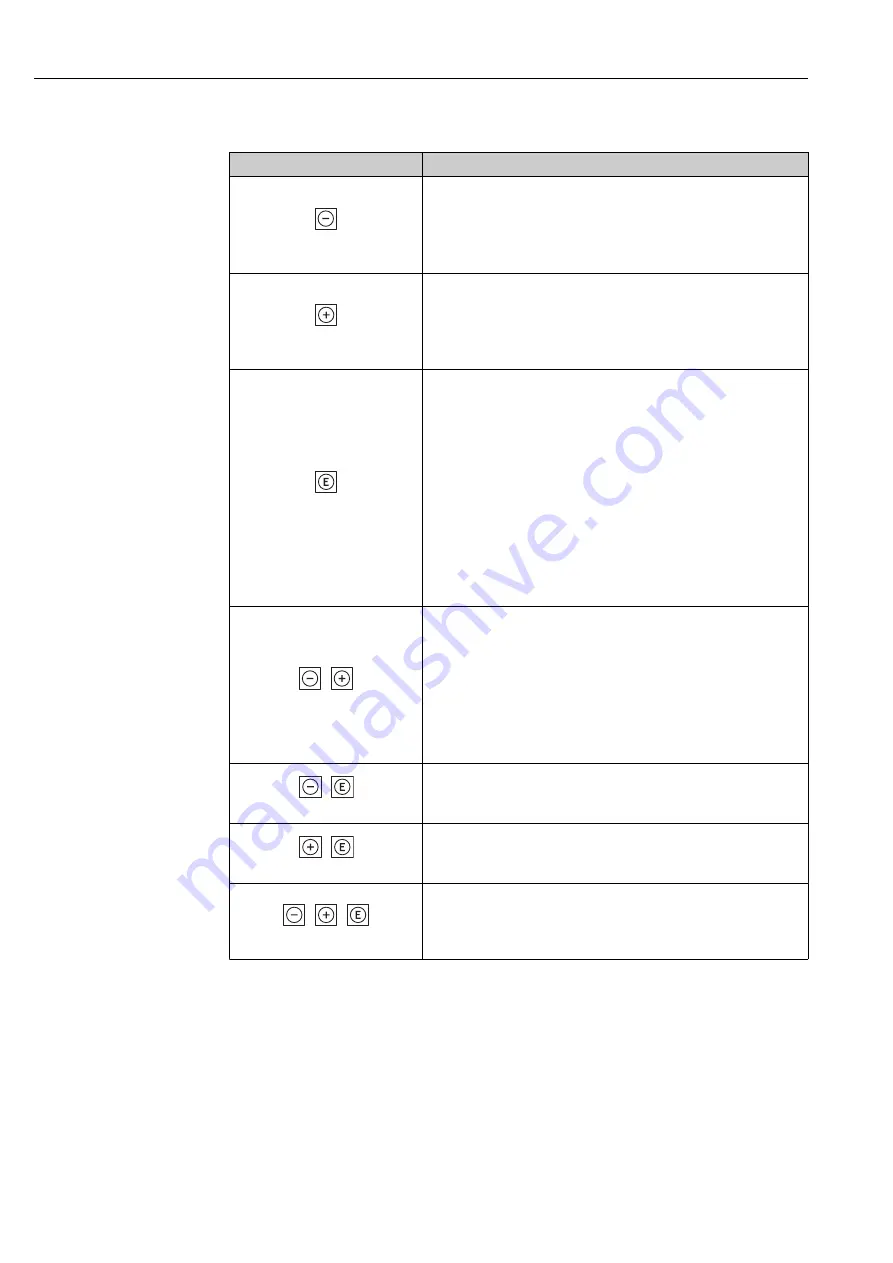
Operation options
Micropilot FMR56, FMR57 FOUNDATION Fieldbus
56
Hauser
8.3.2
Operating elements
Key
Meaning
A0013969
Minus key
For menu, submenu
Moves the selection bar upwards in a picklist.
For text and numeric editor
In the input mask, moves the selection bar to the left (backwards).
A0013970
Plus key
For menu, submenu
Moves the selection bar downwards in a picklist.
For text and numeric editor
In the input mask, moves the selection bar to the right (forwards).
A0013952
Enter key
For measured value display
• Pressing the key briefly opens the operating menu.
• Pressing the key for 2 s opens the context menu.
For menu, submenu
• Pressing the key briefly
Opens the selected menu, submenu or parameter.
• Pressing the key for 2 s for parameter:
If present, opens the help text for the function of the parameter.
For text and numeric editor
• Pressing the key briefly
– Opens the selected group.
– Carries out the selected action.
• Pressing the key for 2 s confirms the edited parameter value.
+
A0013971
Escape key combination (press keys simultaneously)
For menu, submenu
• Pressing the key briefly
– Exits the current menu level and takes you to the next higher level.
– If help text is open, closes the help text of the parameter.
• Pressing the key for 2 s returns you to the measured value display
("home position").
For text and numeric editor
Closes the text or numeric editor without applying changes.
+
A0013953
Minus/Enter key combination (press and hold down the keys
simultaneously)
Reduces the contrast (brighter setting).
+
A0013954
Plus/Enter key combination (press and hold down the keys
simultaneously)
Increases the contrast (darker setting).
+
+
A0013955
Minus/Plus/Enter key combination (press and hold down the keys
simultaneously)
For measured value display
Enables or disables the keypad lock.
Summary of Contents for Micropilot FMR56
Page 197: ......
Page 198: ...www addresses endress com 71344036 71344036 ...