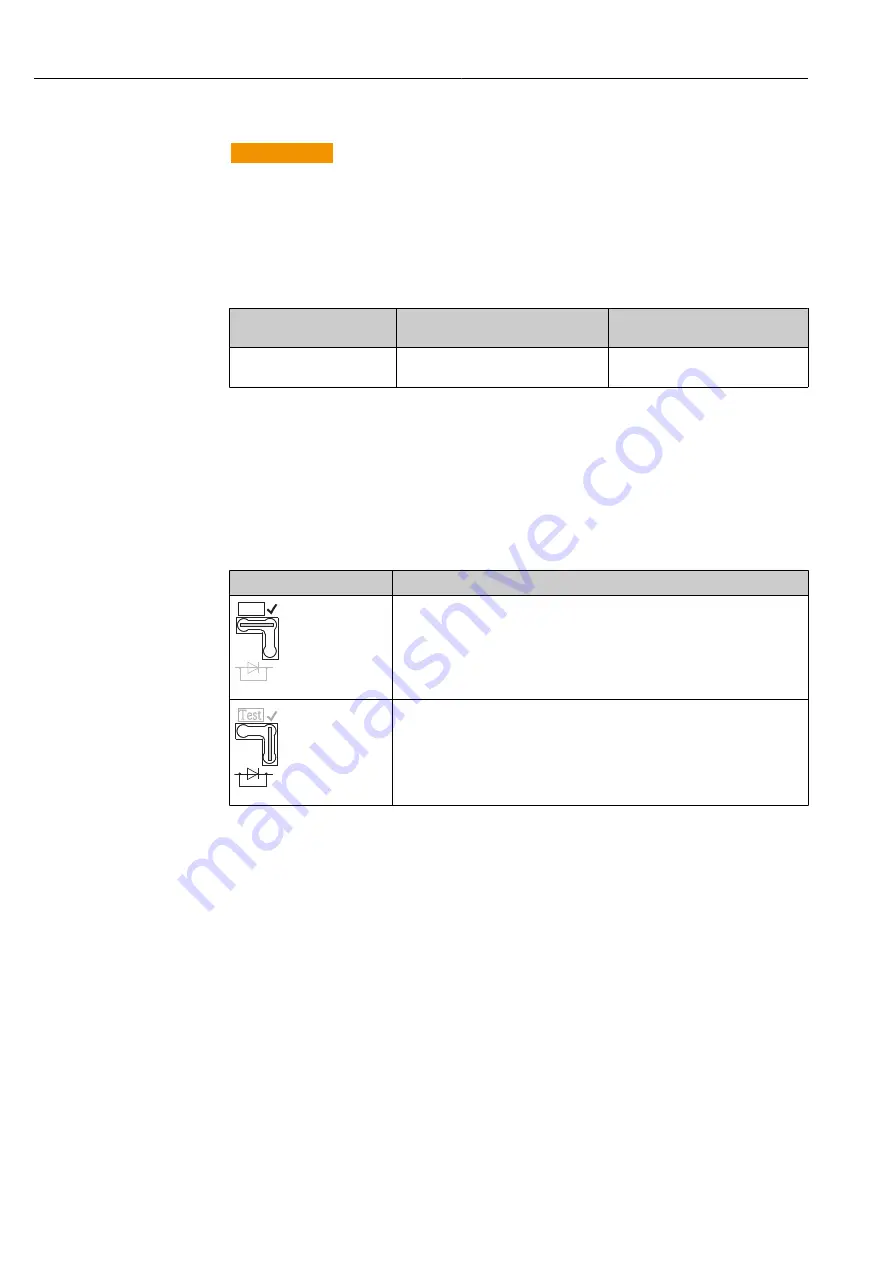
Electrical connection
Deltabar FMD72
22
7.3.2
Supply voltage
!
WARNING
Risk of explosion.
Risk of electric shock and/or explosion!
►
When using the measuring device in hazardous areas, installation must comply with the
corresponding national standards and regulations as well as the Safety Instructions.
►
All explosion protection data are given in separate documentation which is available upon
request. The Ex documentation is supplied as standard with all devices approved for use in
explosion hazardous areas.
Electronic version
Jumper for 4 to 20 mA test signal in
"Test" position (delivery status)
Jumper for 4 to 20 mA test signal in
"Non-test" position
4 to 20 mA HART, version for
non-hazardous areas
13 to 45 V DC
12 to 45 V DC
7.3.3
Measuring a 4 to 20 mA test signal
A 4 to 20 mA test signal may be measured via the positive and test terminal without interrupting
the measurement. The minimum supply voltage of the device can be reduced by simply changing
the position of the jumper. As a result, operation is also possible with a lower supply voltage. To
keep the corresponding measured error below 0.1 %, the current measuring device should exhibit
an internal resistance of
<
0.7
W
. Observe the position of the jumper in accordance with the following
table.
Jumper position for test signal Description
Test
A0016059
• Measurement of 4 to 20 mA test signal via the positive and test terminal: possible.
(Thus, the output current can be measured without interruption via the diode.)
• Delivery status
• Minimum supply voltage: 13 V DC
Test
A0016060
• Measurement of 4 to 20 mA test signal via positive and test terminal: not possible.
• Minimum supply voltage: 12 V DC
7.4
Connection conditions
7.4.1
Cable specification for transmitter connection
• Hauser recommends using twisted, shielded two-wire cables.
• Terminals for core cross-sections 0.5 to 2.5 mm
2
(20 to 14 AWG)
• The cable outer diameter depends on the cable gland used.
Summary of Contents for Deltabar FMD72
Page 2: ......
Page 107: ......
Page 108: ...www endress com worldwide 71191239 71191239 BA01044P 00 EN 02 12 71191239 CCS COSIMA...