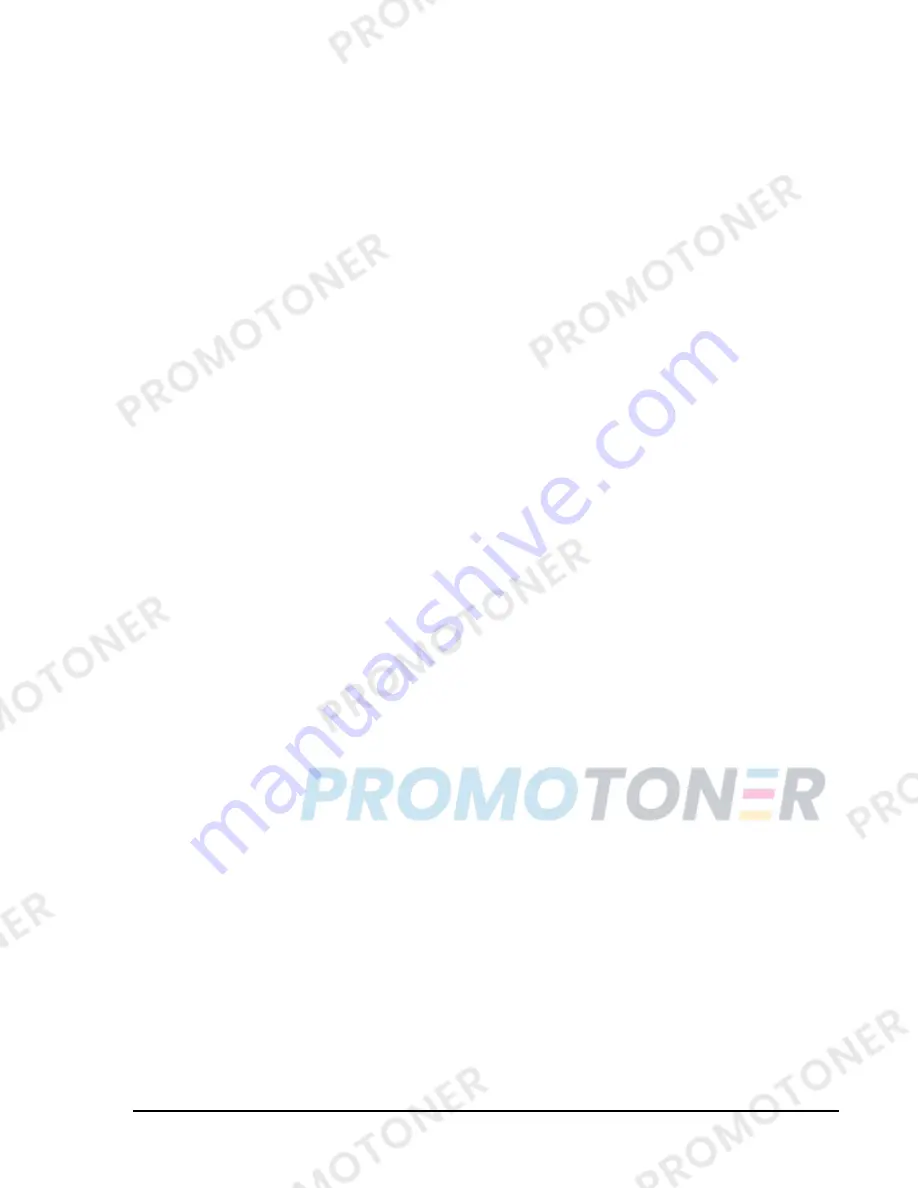
CADJET 2
i
CADJET
®
2
Service Manual
Copyright
1995
ENCAD
®
, Inc.
All rights reserved.
ENCAD
is a registered trademark of
ENCAD, Inc.
Trademark application for
CADJET 2
is pending.
HP-GL
,
HP-GL/2
, and
HP RTL
are registered trademarks of Hewlett-
Packard Company.
AutoCAD
is a registered trademark of AutoDesk, Inc.
Other trademarks and registered trademarks are the property of their
respective owners.
No part of this manual may be copied or distributed, transmitted,
transcribed, stored in a retrieval system, or translated in any human or
computing language, in any form or by any means, electronic,
mechanical, magnetic or otherwise, or disclosed to a third party without
the express written permission of
ENCAD, Inc.
, 6059 Cornerstone
Court West, San Diego, CA 92121, U.S.A.
Summary of Contents for CADJET 2
Page 5: ...CADJET 2 v PRINTING HISTORY 1st Edition September 18 1995...
Page 37: ...General Information CADJET 2 1 11 Figure Chapter 1 1 Front View Cover Closed...
Page 38: ...General Information 1 12 CADJET 2 Figure Chapter 1 2 Front View Cover Open...
Page 116: ...Troubleshooting 4 30 CADJET 2 Figure Chapter 4 3 Parallel and Serial Loop Back Tests...
Page 139: ...Troubleshooting CADJET 2 4 53 Figure Chapter 4 7 Black Cartridge Flex Dimple Pattern...
Page 158: ...Disassembly Assembly CADJET 2 5 5 Figure Chapter 5 1 CADJET 2 Hardware Kit Assembly...
Page 159: ...Disassembly Assembly 5 6 CADJET 2 Figure Chapter 5 2 CADJET 2 Final Assembly Tools...
Page 161: ...Disassembly Assembly 5 8 CADJET 2 Figure Chapter 5 3 Preparing the Plotter for Shipping...
Page 168: ...Disassembly Assembly CADJET 2 5 15 Figure Chapter 5 6 MPCB Connectors...
Page 173: ...Disassembly Assembly 5 20 CADJET 2 Figure Chapter 5 9 Side View of SIMM Removal...
Page 178: ...Disassembly Assembly CADJET 2 5 25 Figure Chapter 5 12 Compression of Frame Tensioner...
Page 186: ...Disassembly Assembly CADJET 2 5 33 Figure Chapter 5 16 Inside View of Left Side Plate...
Page 213: ...Disassembly Assembly 5 60 CADJET 2 Figure Chapter 5 26 Removing the Lower Drive Shaft Screws...
Page 228: ...Disassembly Assembly CADJET 2 5 75 Figure Chapter 5 31 Cutter Assembly...
Page 253: ...Calibration 6 10 CADJET 2 Figure Chapter 6 2 Inner Stand Off Screws and Turnbuckle...
Page 257: ...Calibration 6 14 CADJET 2 Figure Chapter 6 3 Carriage Height Measurement Fixture...
Page 258: ...Calibration CADJET 2 6 15 Figure Chapter 6 4 Installation of Typical Black Cartridge...
Page 268: ...Calibration CADJET 2 6 25 Table Chapter 6 2 Potentiometer Adjustment Flowchart...
Page 337: ...Replacement Parts List CADJET 2 7 29 Figure Chapter 7 52 Slide Shaft P N 204007 31...
Page 347: ...Appendix A CADJET 2 A 3 Figure Appendix A 1 Cable RS422 Mini DIN8 P N 203977...
Page 355: ...Appendix C CADJET 2 C 6 Figure Appendix C 1 CADJET 2 D Size Final Assembly Drawing...
Page 356: ...Appendix C CADJET 2 C 7 Figure Appendix C 2 CADJET 2 E Size Final Assembly Drawing...