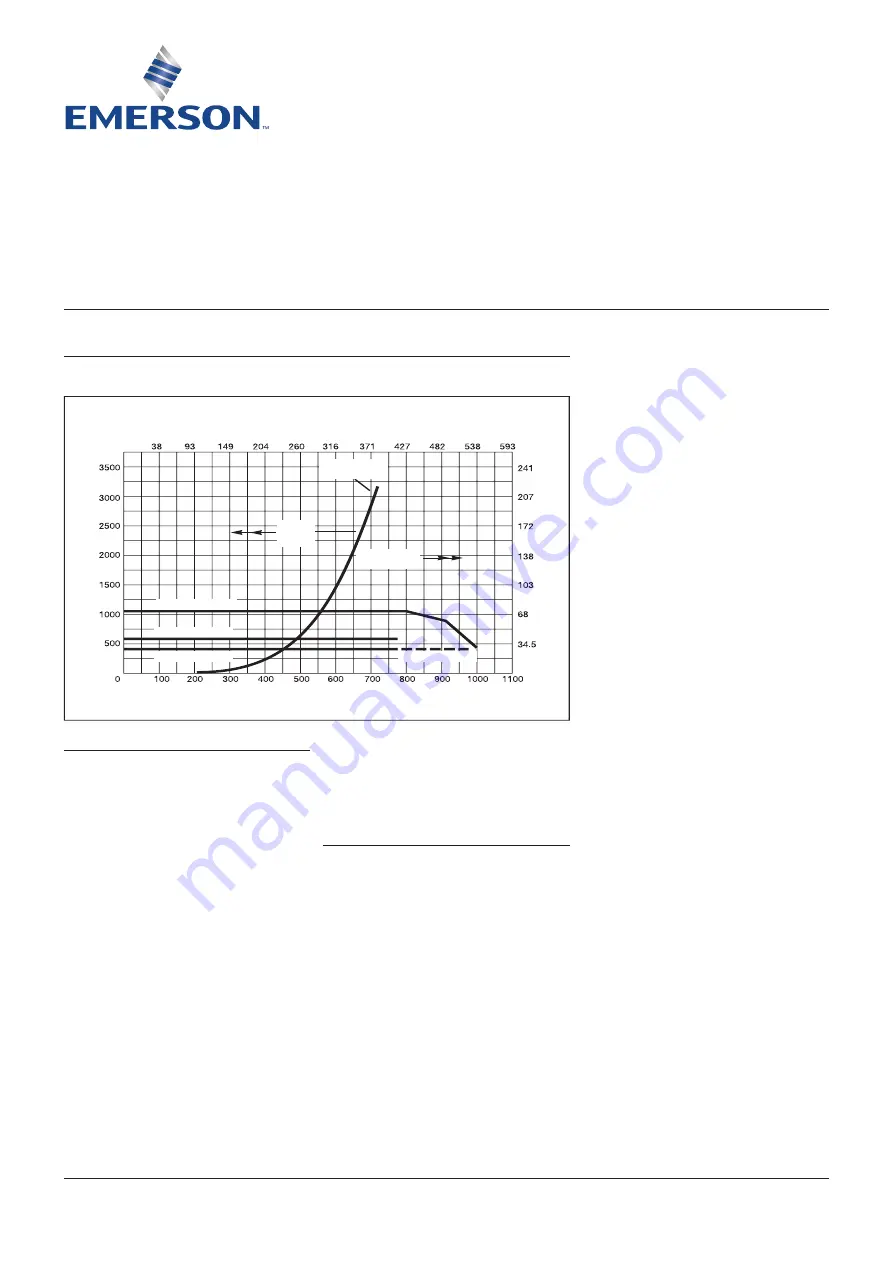
VCIOM-09534-EN 18/09
Emerson.com/FinalControl
© 2018 Emerson. All Rights Reserved.
YarwaY
SERiES 400 intEgRAl StRAinERimpulSE
®
InstructIon, operatIon and maIntenance manual
Before installation these instructions must be fully read and understood
BaCk prEssurE lIMIts
piston valve traps rated to 400 psig (28 bar)
(incl.) are factory set to operate from 20
psig (1.4 bar) to maximum rated pressure.
maximum allowable back pressure at trap
outlet equals 40% of pressure at trap inlet.
(Based on absolute pressure.)
piston Valve traps rated to 600 psig (42 bar)
(incl.) are factory set to operate from 40
psig (2.8 bar) to 600 psig (42 bar). maximum
allowable back pressure at trap outlet equals
25% of pressure at trap inlet. (Based on
absolute pressure.)
Note:
the traps operate over the specified
ranges without adjustment.
piston Valve traps may be adjusted to operate
between 10 psig (.7 bar) and the minimums
stated above by removing the split washer (see
disassembly section.) Back pressures higher
than the percentages stated above will cause
the traps to blow open. Where normal system
back pressures are high, removal of the split
washer will also permit operation against back
pressures up to 55% of pressure at trap inlet.
(Based on absolute pressure.)
ratINgs
Operating pressure ranges
Disc valve traps rated to 600 psig (42 bar) (incl.)
operate from 4 psig (.28 bar) to maximum rated
pressure. maximum allowable back pressure
at trap outlet is 60% of pressure at trap inlet.
(Based on absolute pressure.)
sErIEs NuMBErs
to determine the size, series number, and
pressure temperature rating refer to the
nameplate on the trap body.
mAX. tEmpERAtuRE (C)
m
AX.
pRESS
u
RE, bar
mAX. tEmpERAtuRE (F)
m
AX.
pRESS
u
RE, psi
SAtuRAtiOn
CuRVE
All
SupERHEAt
All
liQuiD
pHASE
SERiES 460
SERiES 461
SERiES 441
SERiES 440