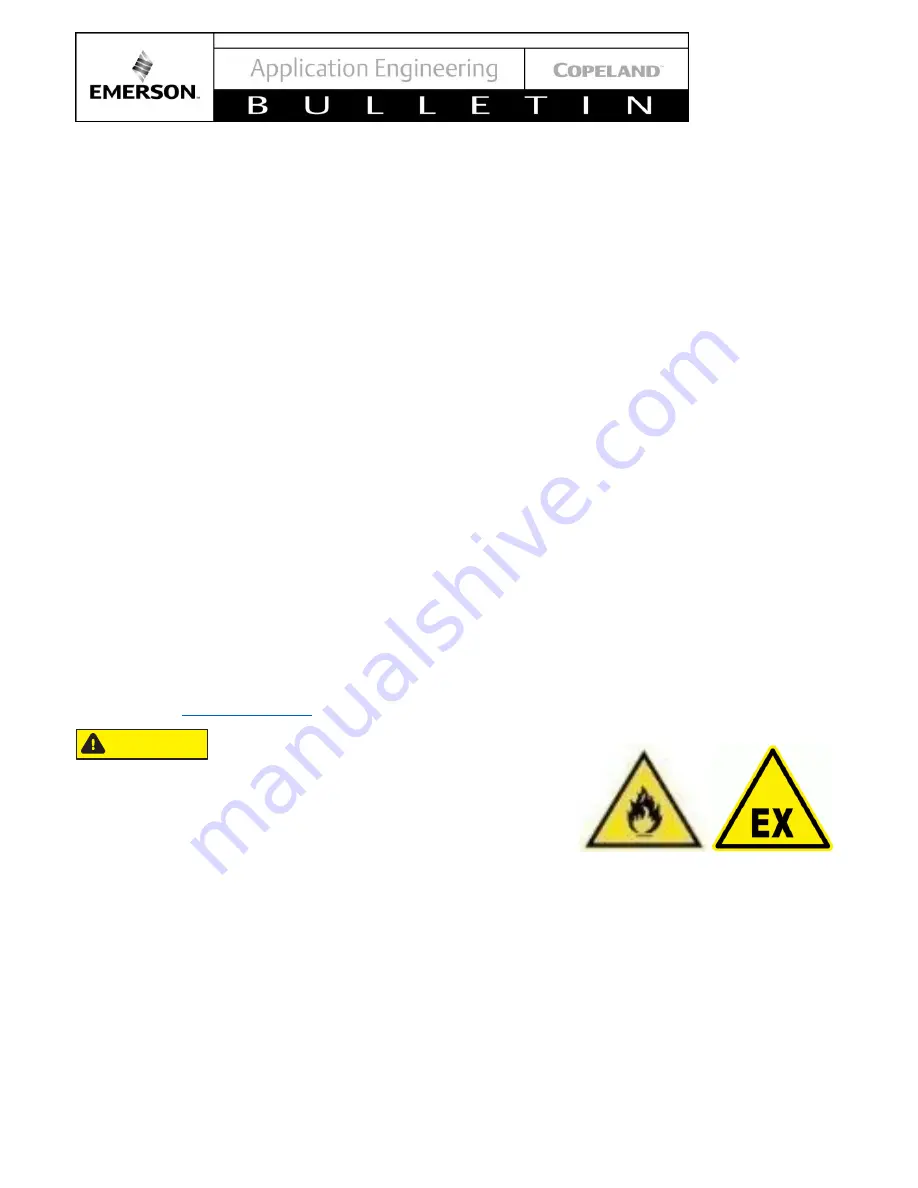
© 2018 Emerson Climate Technologies, Inc.
21
AE4-1431 R1
In the case of an R290 compressor replacement the oil
must be drained out of the compressor and the
compressor should be flushed with dry nitrogen.
DO
NOT close the stubs with plugs.
In the case of a motor burnout, most of contaminated oil
will be removed with the compressor. The rest of the oil
is cleaned using suction and liquid line filter driers. A
100% activated alumina suction line filter drier is
recommended but it must be removed after 72 hours.
6.3.2. Start-up of a new or replacement
compressor
Rapid charging only on the suction side of a scroll-
equipped system can occasionally result in a temporary
no-start condition for the compressor. The reason for
this is that, if the flanks of the scrolls happen to be in a
sealed position, rapid pressurization of the low side
without opposing high-side pressure can cause the
scrolls to seal axially. As a result, until the pressures
eventually equalize, the scrolls can be held tightly
together preventing rotation.
The charge should be
done on the high-pressure side of the system.
Before system start-up, allow the pressures to
equalize.
Follow instructions detailed about tagging and
locking out on
section on Pg. 5.
Do not start the compressor while the system is in a
deep vacuum. Internal arcing may occur when a Scroll
compressor is started in a vacuum causing burnout of
the internal lead connections.
6.3.3. Compressor return procedure
To return a compressor to Emerson for analysis, the
procedure below shall be followed:
•
During the entire working procedure continuously
check if the ambient atmosphere is explosive. If
explosive atmosphere is detected ensure proper
ventilation of the working space and immediately
cut-off the power supply.
•
Resume working after the atmosphere is no longer
dangerous.
•
Recover the refrigerant from the system using a
suitable recovery unit.
•
Do not allow the recovery unit to recover below
atmospheric pressure. Make sure the low-pressure
switch that stops the recovery process is not set
below 7 PSIG.
•
At this pressure, some refrigerant will still be in the
system. Therefore, before opening the system,
pressurize to 15 PSIG with dry nitrogen.
•
Open the system with a cutting tool and flush the
entire system with dry nitrogen.
•
Disassemble the compressor with a cutting tool.
Drain and recover compressor oil properly. Flush
the compressor with dry nitrogen for a few minutes.
•
The compressor should be returned free of oil and
with connections open - do not close connections
with plugs.
•
Properly collect and secure the oil. Provide
information about the quantity of oil drained from the
compressor and its color. Ideally, send a good
picture.
•
Dispose of the oil according to local rules and
regulations.
•
Use a proper cardboard box package when
preparing the compressor for shipment. Place
warning icons on each side and on the top of the
box:
Mention the following message on the box:
"Warning!
Hydrocarbon
compressor
for
analysis".
•
The compressor shipment must be kept in the
upright position
– mark it accordingly.
•
If more than one compressor is returned, each
compressor has to be packed individually.
NOTE: Check with your transport company to
ensure compliance with all requirements for such a
shipment.
CAUTION