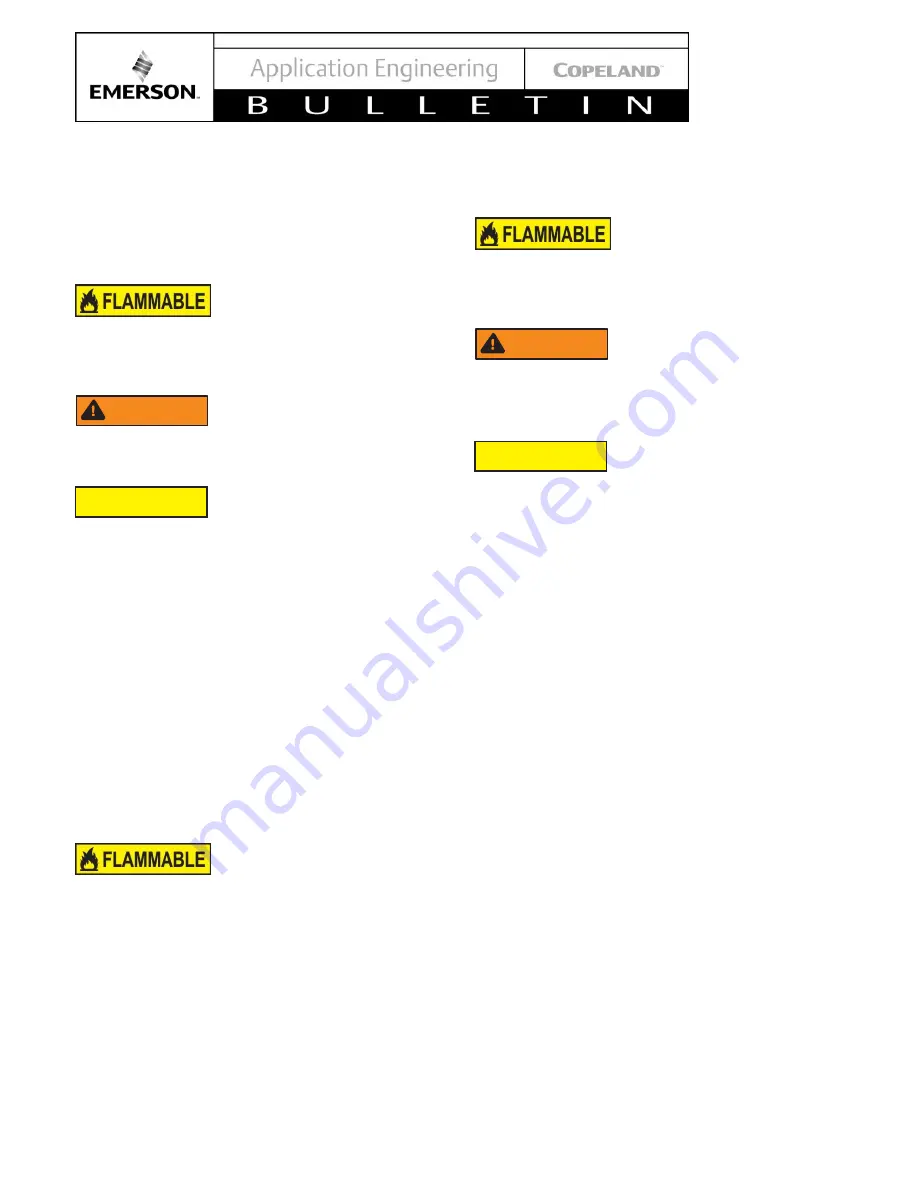
© 2018 Emerson Climate Technologies, Inc.
17
AE4-1431 R1
4.5. Motor protection
Conventional inherent internal line break motor
protection is provided for the ZB*KAU range of
compressors.
4.6. High-potential testing
High potential testing on R290 compressor!
Special
attention should be paid when performing high-potential
testing.
Conductor cables! Electrical shock!
Shut off power
supply before high-potential testing.
Internal arcing! Motor destruction!
Do not carry out
high-voltage or insulation tests if the compressor
housing is under vacuum.
Emerson subjects all Scroll compressors to a high-
voltage test after final assembly. Each motor phase
winding is tested according to EN60335-2-34, IEC
60335-2-34 and UL 60335-2-34 at a differential voltage
of 1000V plus twice the nominal voltage.
Since high-voltage tests lead to premature ageing of the
winding insulation, further additional tests of this nature
are not recommended. However, if it must be done for
any reason, a lower voltage must be used. Disconnect
all electronic devices, e.g., motor protection module, fan
speed control, etc. prior to testing.
The high-potential and/or Megohm resistance
testing must not be done with the compressor
charged with R-290
. These tests can induce an
electrical arc and cause a potential fire/explosion
hazard.
For the same reason, compressors removed from an
R290 system will need to have the oil drained and a
nitrogen purge introduced to flush any remaining
refrigerant from the compressor prior to high-potential
testing and Megohm resistance reading.
5. Starting up & operation
5.1. Compressor tightness test
High pressure! Personal injuries!
Consider personal
safety requirements and refer to test pressures prior to
test.
System explosion! Personal injuries!
Use only dry
nitrogen for leak testing. DO NOT USE other industrial
gases.
System contamination! Bearing malfunction!
Use
only dry nitrogen for leak testing. DO NOT USE other
industrial gases.
The compressor has been leak-pressure tested in the
Emerson factory according to standards EN 14276-1,
EN 60335-2-34, IEC 60335-2-34 and UL60335-2-34.
Therefore, it is not necessary for the system
manufacturer/installer
to
leak-pressure
test
the
compressor on the assembly/system.
Never add refrigerant to the test gas (as leak indicator).
Leak checking at a pressure not to exceed 175 PSIG
should be Ok to verify connections.
5.2. System evacuation
Before the installation is put into commission, it must be
evacuated with a vacuum pump. The vacuum pump and
all tools must be approved for R290/air mixture. The
installation should be evacuated down to 225 microns.
Proper evacuation reduces residual moisture to 50 ppm.
Evacuating the system only on the suction side of a
Scroll compressor can occasionally result in a
temporary no-start condition for the compressor. The
reason for this is that the floating seal could axially seal
with the scroll set, with the higher pressure on the
floating seal. Consequently, until the pressures
equalize, the floating seal and scroll set can be held
tightly together.
WARNING
CAUTION
WARNING
CAUTION