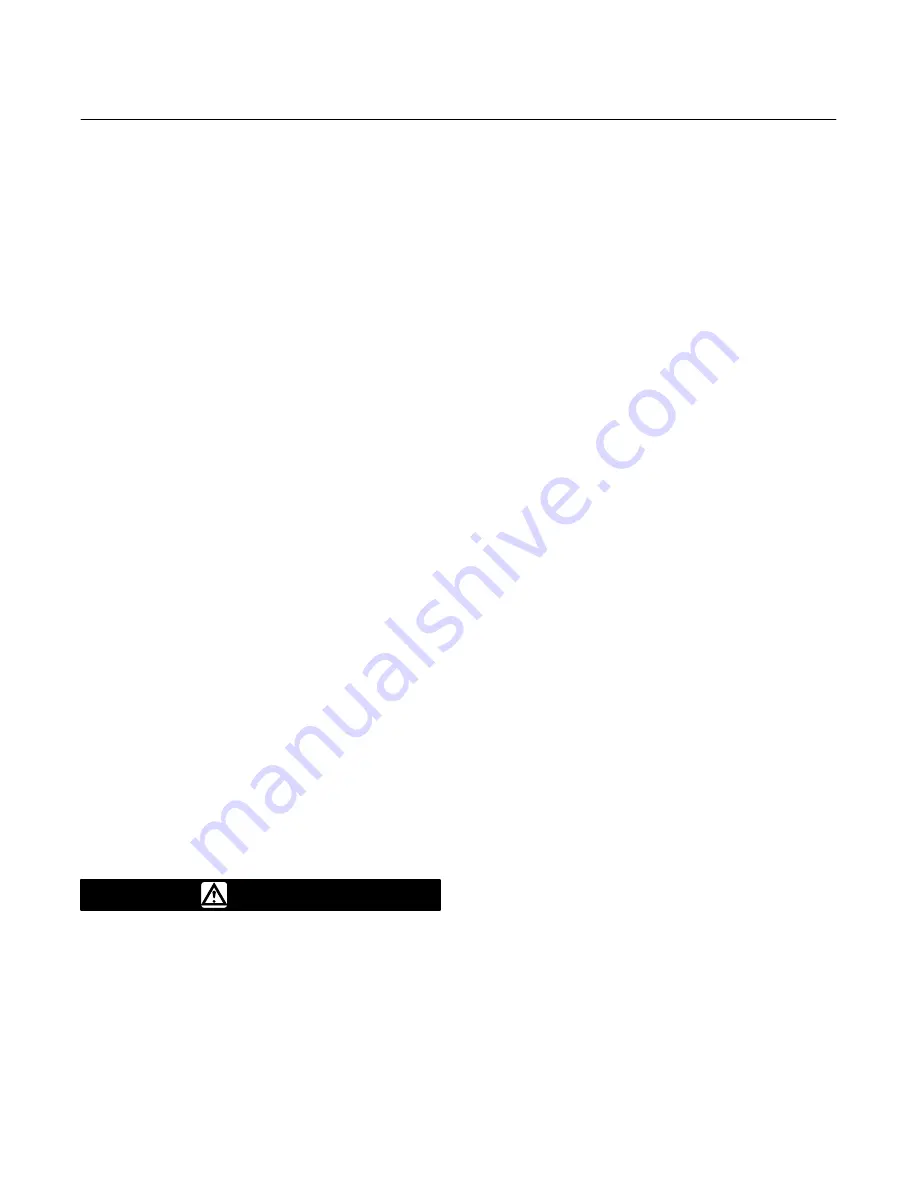
Type 2500
Instruction Manual
Form 1013
December 2005
24
pressure or completely closes the relay valve for full
exhaust of the output pressure, allowing no
in-between throttling.
For a direct-acting controller, as long as the process
variable remains above the switch point, the flapper
does not depress the plunger of the Bourdon tube
valve. In this condition, the Bourdon tube valve
remains closed, providing full loading pressure to the
Bourdon tube. This loading pressure moves the
Bourdon tube away from the flapper. Also, in this
condition, full loading pressure is on the upper
diaphragm of the relay. The loading pressure moves
the diaphragm down, closing the exhaust end and
opening the inlet end of the relay valve, allowing full
output pressure.
When the process level sufficiently decreases, the
flapper pushes in the plunger of the Bourdon tube
valve enough to release the loading pressure and
seal the inner Bourdon tube channel (see figure 13).
This decrease in the loading pressure moves the
Bourdon tube toward the flapper, producing the snap
action. Also, this decrease in loading pressure
allows relay spring pressure to move the large
diaphragm up, closing the inlet end and opening the
exhaust end of the relay valve, allowing full exhaust
of the output pressure. This control action continues
until a sensor level change moves the flapper away
from the plunger, permitting the Bourdon tube valve
to close, restoring loading pressure to the pneumatic
circuit. Reverse-acting controllers produce the
opposite effect.
Maintenance
The 2500 and 2503 Series controllers/transmitters
work in combination with 249 Series displacers.
Refer to figure 16 for key number locations, unless
otherwise indicated.
WARNING
Always wear protective clothing,
gloves, and eyewear when performing
any maintenance operations to avoid
personal injury.
When replacing the sensor assembly,
the displacer may retain process fluid
or pressure. Personal injury or
property damage may occur due to
sudden release of the pressure.
Contact with hazardous fluid, fire, or
explosion can be caused by
puncturing, heating, or repairing a
displacer that is retaining process
pressure or fluid. This danger may not
be readily apparent when
disassembling the sensor assembly or
removing the displacer. Before
disassembling the sensor or removing
the displacer, observe the more
specific warning provided in the
sensor instruction manual.
When disconnecting any of the
pneumatic connections, natural gas, if
used as the supply medium, will seep
from the unit and any connected
equipment into the surrounding
atmosphere. Personal injury or
property damage may result from fire
or explosion if preventative measures
are not taken, such as adequate
ventilation and the removal of any
nearby ignition sources.
Check with your process or safety
engineer for any additional measures
that must be taken to protect against
process media.
Troubleshooting
When troubleshooting, open loop conditions must
exist unless otherwise stated. When monitoring the
process variable, use the most accurate level
indicating device available. The output signal
measuring device should have corresponding
accuracy.
Table 7 lists some common operating faults, their
probable causes, and corrective action.