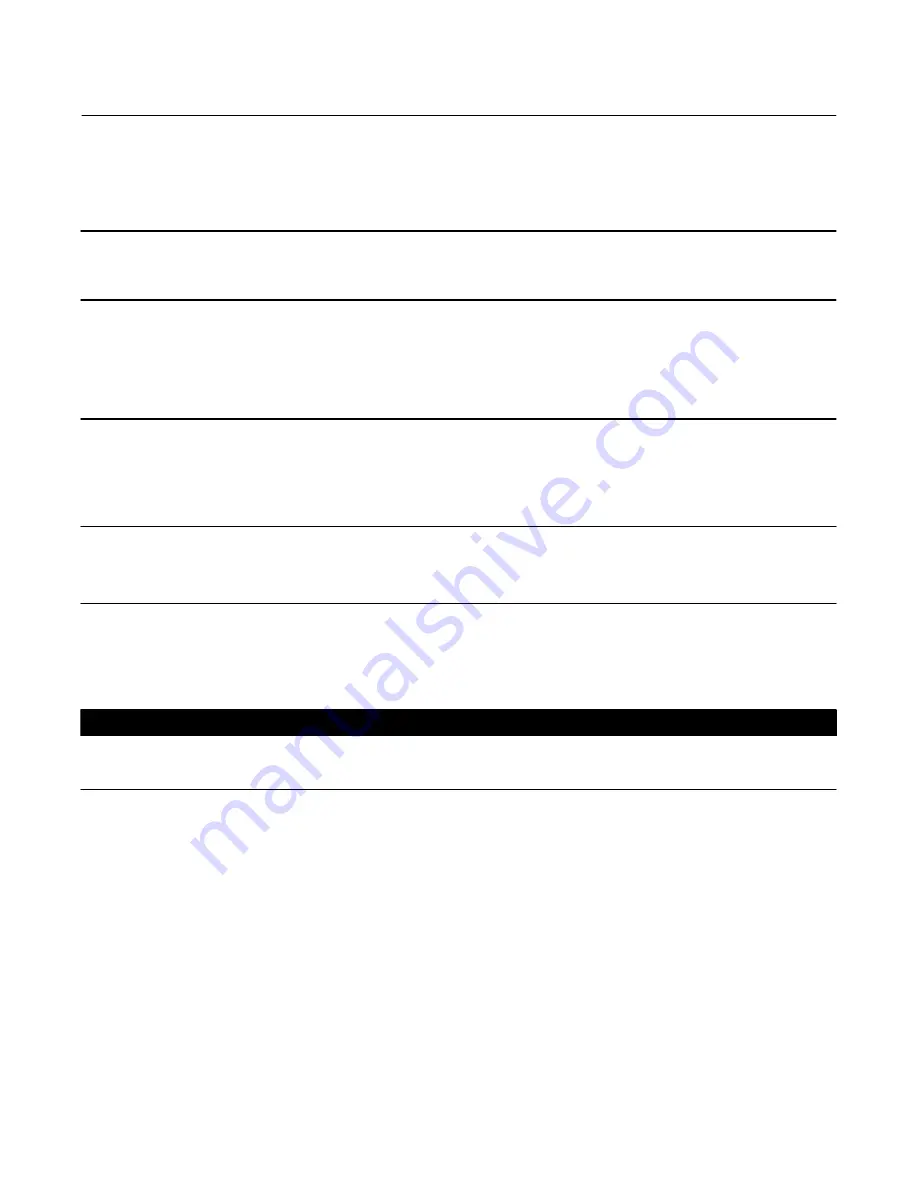
Instruction Manual
D200126X012
2502 Controllers
June 2017
9
Mounting Cageless Sensor
Note
If a stillwell is used, it must be installed plumb so that the displacer does not touch the wall of the stillwell. Should the displacer
touch the wall while the unit is in service, the unit will transmit an erroneous output signal.
Since the displacer hangs inside the vessel, provide a stillwell around the displacer if the liquid is in a state of
continuous agitation to avoid excessive turbulence around the displacer.
Note
Displacers used in an interface level application must be completely submerged during operation. If displacers aren't completely
submerged they will not calibrate or perform properly. To obtain the desired controller sensitivity may require using either a
thin‐wall torque tube, an oversized displacer, or both.
Note
If the controller is not mounted on the sensor, refer to the Installing Controller on Sensor section. This section also provides
instructions for adding a heat insulator to a unit.
Attach a cageless sensor to a flanged connection on the vessel as shown in figure 7. For interface or liquid level
applications, install a gauge glass on the vessel.
CAUTION
If the displacer is to be inserted into the vessel before being attached to the displacer rod, provide a suitable means of
supporting the displacer to prevent it from dropping into the vessel and suffering damage.
To help support a 249BP or 249CP displacer, install the displacer stem and stem end piece, or a threaded rod, into the
1/4 inch‐28 UNF threaded hole in the displacer spud or stem end piece (figure 8). On the 249BP with optional travel
stop, the stem end piece pins will secure the displacer as long as the travel stop plate is installed and the sensor head is
in position.
Side‐Mounted Sensor
If a stillwell is required (figure 7), the displacer must be attached to the displacer rod from inside the vessel. Connect
the displacer as shown in figure 8, locking the assembly with the cotter spring provided. If a stillwell is not required, the
displacer can be attached to the displacer rod before mounting the sensor to the vessel connection. The displacer may
then be swung out horizontally for insertion into the vessel. However, once the sensor is installed and the displacer
drops to a vertical position, the displacer may not be capable of being withdrawn for servicing later. Be sure there is
another access to the displacer to permit swinging it to a horizontal position or to permit disconnecting it from the
displacer rod.