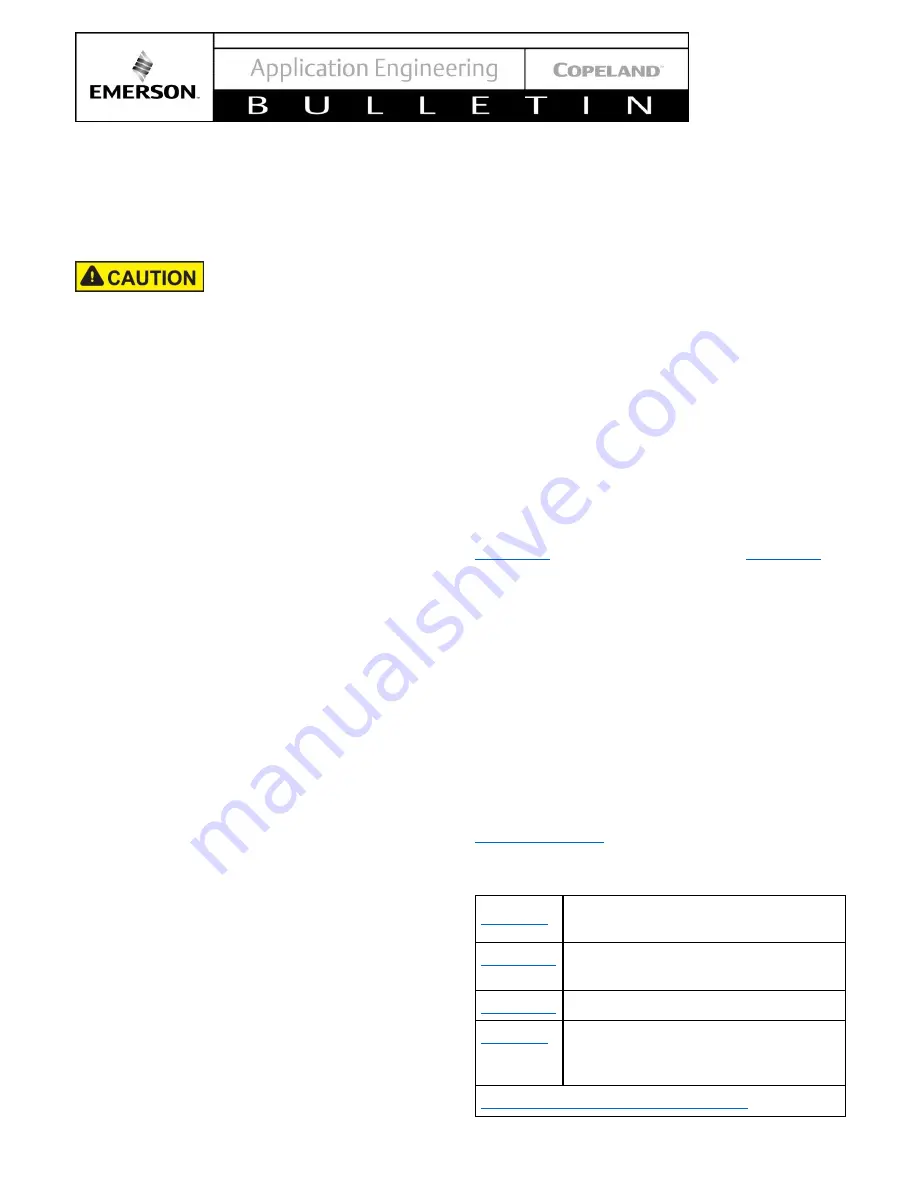
© 2017 Emerson Climate Technologies, Inc.
9
AE4-1372 R4
Under no circumstances should the hipot test be
performed while the compressor is under a vacuum.
MAINTENANCE AND REPAIR
Service Procedures
Copeland Scroll compressor functional check: A
functional compressor test during which the suction
service valve is closed to check how low the compressor
will pull the suction pressure is not a good indication of
how well a compressor is performing. Such a test will
damage a scroll compressor in a few seconds.
The following diagnostic procedure should be used to
evaluate whether a Copeland Scroll compressor is
functioning properly:
1. Proper voltage to the unit should be verified.
2. Determine if the internal motor overload has
opened or if an internal motor short or ground fault
has developed. If the internal overload has
opened, the compressor must be allowed to cool
sufficiently to allow it to reset.
3. Check that the compressor is correctly wired.
4. Proper indoor and outdoor blower/fan operation
should be verified.
5. With service gauges connected to suction and
discharge
pressure
fittings,
turn
on
the
compressor. If suction pressure falls below
normal levels the system is either low on charge
or there is a flow blockage in the system.
6. Three phase compressors
– If suction pressure
does not drop and discharge pressure does not
rise to normal levels, reverse any two of the
compressor power leads and reapply power to
make sure the compressor was not wired to run in
reverse. If pressures still do no move to normal
values, either the reversing valve (if so equipped)
or the compressor is faulty. Reconnect the
compressor leads as originally configured and
use normal diagnostic procedures to check
operation of the reversing valve.
7. To test if the compressor is pumping properly, the
compressor current draw must be compared to
published compressor performance curves using
the operating pressures and voltage of the
system. If the measured average current deviates
more than +/-20% from published values, a faulty
compressor may be indicated. A current
imbalance exceeding 20% of the average on the
three phases of a three-phase compressor should
be investigated further. A more comprehensive
trouble-shooting sequence for compressors and
systems can be found in Section H of the
Electrical Handbook, Form No. 6400
.
8. Before replacing or returning a compressor, be
certain that the compressor is actually defective.
As a minimum, recheck compressors returned
from the field in the shop or depot by testing for a
grounded, open or shorted winding and the ability
to start. The orange tag in the service compressor
box should be filled out and attached to the failed
compressor to be returned. The information on
this tag is captured in our warranty data base.
Compressor Replacement After a Motor Burn
In the case of a motor burn, the majority of contaminated
oil will be removed with the compressor. The rest of the
oil is cleaned with the use of suction and liquid line filter
driers. A 100% activated alumina suction filter drier is
recommended but must be removed after 72 hours. See
for
liquid line filter-drier recommendations. It is highly
recommended that the suction accumulator be replaced
if the system contains one. This is because the
accumulator oil return orifice or screen may be plugged
with debris or may become plugged shortly after a
compressor failure. This will result in starvation of oil to
the replacement compressor and a second failure. The
system contactor should be inspected for pitted/burnt
contacts and replaced if necessary. It is highly
recommended that the run capacitor be replaced when
a single phase compressor is replaced.
General Guidelines and More Information
For general Copeland Scroll compressor and CO
2
refrigerant please log in to Online Product Information at
refer to the Application Engineering
bulletins listed below, or contact your Application
Engineer.
Megaohms
Values
of
Copeland
™
Compressors
Principles of Cleaning Refrigeration
Systems
Application Guidelines for Copeland™
Semi-Hermetic
Compressors
for
Transcritical CO2 Applications
Commercial CO2 Refrigeration Systems
Guide