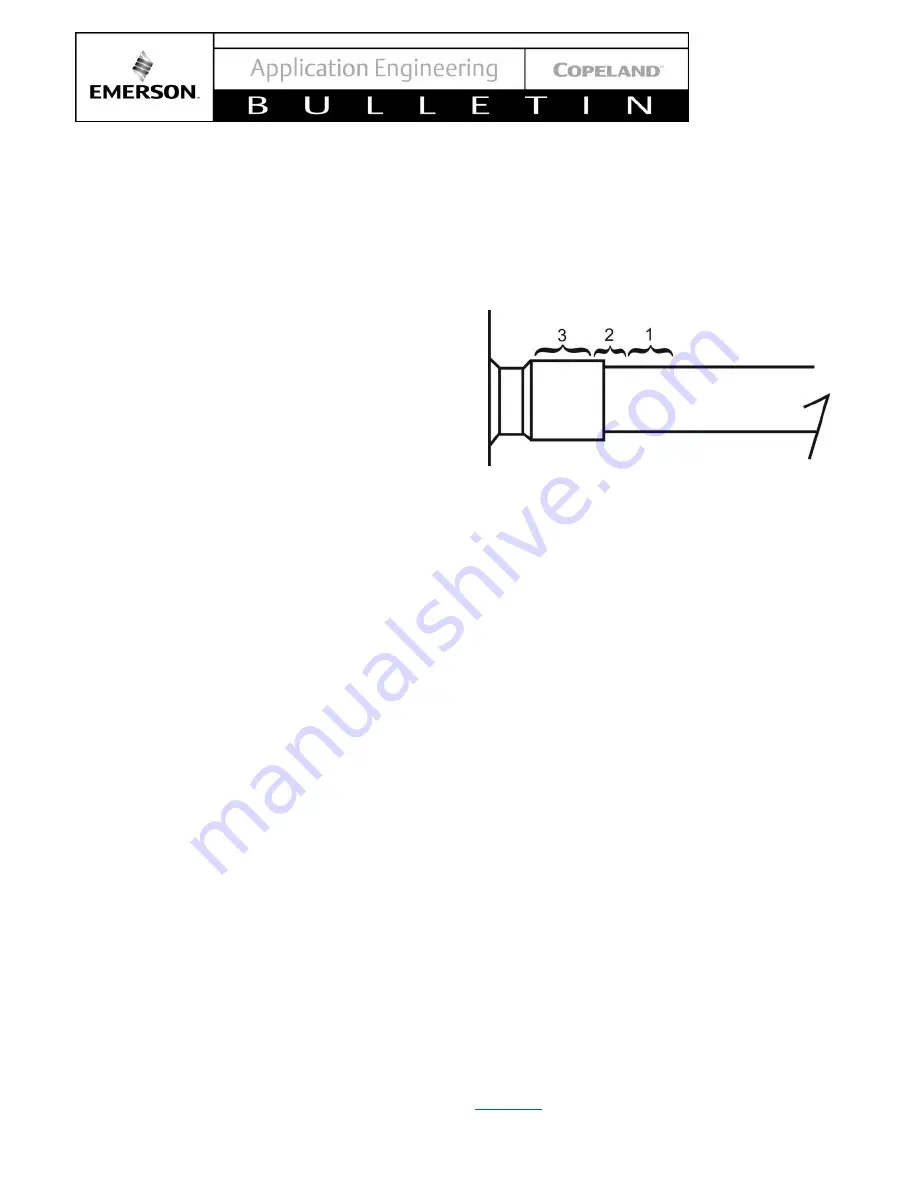
© 2017 Emerson Climate Technologies, Inc.
8
AE4-1372 R4
tube (available from Emerson) and install it in a system
with the longest connecting lines that are approved for
the system. The minimum on time becomes the time
required for oil lost during compressor start-up to return
to the compressor sump and restore a minimal oil level
that will ensure oil pick-up through the crankshaft.
Cycling the compressor for a shorter period than this, for
instance to maintain very tight temperature control, will
result in progressive loss of oil and damage to the
compressor.
ASSEMBLY LINE PROCEDURES
Installing the Compressor
Copeland Scroll compressors leave the factory
dehydrated and with a positive dry air charge. Plugs
should not be removed from the compressor until the
compressor has had sufficient time to warm up if stored
outside and is ready for assembly in the unit. The
suggested warm up time is one hour per 4°F (2K)
difference between outdoor and indoor temperature. It
is suggested that the larger suction plug be removed
first to relieve the internal pressure. Removing the
smaller discharge plug could result in a spray of oil out
of this fitting since some oil accumulates in the head of
the compressor after Emerson’s run test. The inside of
both fittings should be wiped with a lint free cloth to
remove residual oil prior to brazing. A compressor
containing POE oil should never be left open longer than
5 minutes.
Assembly Line Brazing Procedure
Following are
the proper procedures for brazing the
suction and discharge lines to a scroll compressor. It is
important to flow nitrogen through the system while
brazing all joints during the system assembly process.
Nitrogen displaces the air and prevents the formation of
copper oxides in the system. If allowed to form, the
copper oxide flakes can later be swept through the
system and block screens such as those protecting
capillary tubes, thermal expansion valves, and
accumulator oil return holes. Any blockage of oil or
refrigerant may damage the compressor resulting in
failure.
New Installations
•
The copper-coated steel suction tube on scroll
compressors can be brazed in approximately the
same manner as any copper tube.
•
Recommended brazing materials: Any SIL-FOS®
material is recommended, preferably with a
minimum of 5% silver. However, 0% silver is
acceptable.
•
Be sure suction tube fitting I.D. and suction tube
O.D. are clean prior to assembly. If oil film is
present wipe with denatured alcohol, Dichloro-
Trifluoroethane or other suitable solvent.
•
Using a double-tipped torch apply heat in Area 1.
As tube approaches brazing temperature, move
torch flame to Area 2.
Scroll Suction Tube Brazing
•
Heat Area 2 until braze temperature is attained,
moving torch up and down and rotating around
tube as necessary to heat tube evenly. Add braze
material to the joint while moving torch around
joint to flow braze material around circumference.
•
After braze material flows around joint, move
torch to heat Area 3. This will draw the braze
material down into the joint. The time spent
heating Area 3 should be minimal.
•
As with any brazed joint, overheating may be
detrimental to the final result.
‘Hipot’ (AC High Potential) Testing
Copeland Scroll compressors are configured with the
motor down and the pumping components at the top of
the shell. As a result, the motor can be immersed in
refrigerant to a greater extent than hermetic
reciprocating compressors when liquid refrigerant is
present in the shell. In this respect, the scroll is more like
semi-hermetic compressors that have horizontal motors
partially submerged in oil and refrigerant.
When Copeland Scroll compressors are hipot tested
with liquid refrigerant in the shell, they can show higher
levels of leakage current than compressors with the
motor on top. This phenomenon can occur with any
compressor when the motor is immersed in refrigerant.
The level of current leakage does not present any safety
issue. To lower the current leakage reading, the system
should be operated for a brief period of time to
redistribute the refrigerant to a more normal
configuration and the system hipot tested again. See