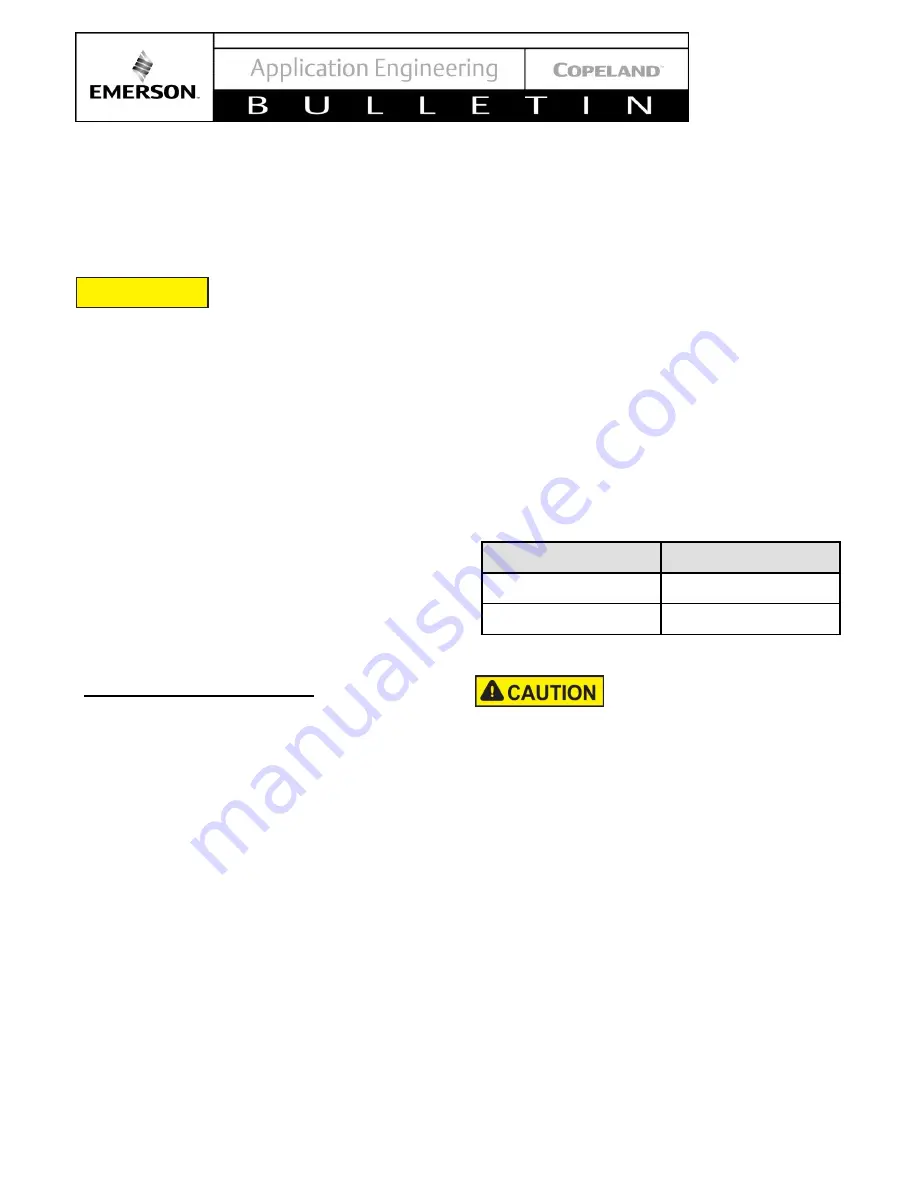
© 2017 Emerson Climate Technologies, Inc.
5
AE4-1372 R4
structure.
The use of standard soft grommets is not
recommended
.
Refer
Safety Relief Valves
In a closed system filled with CO
2
the pressure can rise
above 725 PSIG (50 Bar) under some ambient
conditions. The system must be equipped with safety
relief valves to
ensure that the compressor’s low side
and high side pressures are not exceeded (see below).
If the unit is shut down for service or other reasons, the
pressure will rise due to ambient heat. To prevent the
loss of charge at shut down through the relief valves, it
is recommended to provide additional cooling to keep
the pressure below the maximum standstill pressure of
the suction side. This can be achieved using a small
auxiliary
condensing
unit
connected
to
an
uninterruptable power supply, that removes heat from
the R744 liquid receiver. The auxiliary condensing unit
will not be sufficient to maintain the low-stage system
below the Maximum Allowable Operation Pressure if
there is a load from the evaporators.
Refer to ANSI/ASHRAE Standard 15-2016, Section
9.7.5 and ANSI/ASHRAE 15 appendix C-2016.
ZO Maximum Operating pressures
Suction side
400 PSIG (27.6 Bar)
Discharge side
625 PSIG (43.1 Bar)
The requirements for Copeland Scroll compressors with
CO
2
per Underwriters Laboratory (UL) state that a
system with a CO
2
compressor must be installed with an
approved suction pressure relief valve. ASME high-
pressure relief valves are the only valves currently
approved for use with the Copeland Scroll CO
2
models.
The installation of the above valve must meet the
following criteria:
1. There must be an open flow path from the
compressor suction sump to the relief valve. This
is accomplished by connecting the relief valve to
the correct port on the suction Rotalock valve.
This port is open to the compressor sump no
matter what position the valve stem is located.
The relief valve itself can be remotely located as
long as the path from compressor suction sump
and the valve is always open.
2. This flow path cannot be shut off in any way by a
valve.
represents the correct (a) and incorrect (b) way
to apply the pressure relief valve. Failure to apply the
high-pressure relief valve correctly will void any UL
approval of the system.
The high-pressure relief valve should be located such
that the path between the valve and the low side of the
compressor is always open and cannot be shut off in
any way by a valve.
Note that the valve opens only
once and must be replaced if it opens.
A 500 PSIG (34.5 Bar) high-pressure relief valve kit is
shipped with the compressor. Contact Application
Engineering for alternative pressure relief valves.
ZO compressors have Rotalock valve fittings. Rotalock
shut-off valves are available for the suction as well as
discharge side. Using either straight or angled adaptors
provides a way to convert a Rotalock into a brazing
connection.
Tightening Torques
Torque
Lbs.
Rotalock 1"-1 UNF
60-70 ft.lb.
Rotalock 1"1/4-12 UNF
75-85 ft.lb
High-Pressure Safety Controls
A CO
2
approved ASME safety pressure relief valve(s)
with a setting of 500 PSIG (34.5 Bar) is required to be
pre-installed for standstill conditions.
All sections that can be isolated in the system must have
relief valves pre-installed by the system manufacturer
with a 500 PSIG (34.5 Bar) setting.
These high-pressure cut-outs should have a manual
reset feature.
Additional Requirements:
Low Pressure Cut-Out on Suction Side:
80 PSIG (5.5 bar)
High Pressure Cut-Out on Discharge Side: 625
PSIG (43.1 Bar)
Discharge Temperature Protection
External discharge line thermostat 998-7022-02
Active Oil Management
An OMC CO2 electronic oil level management system
should be used that is suitable for both high and low-
CAUTION