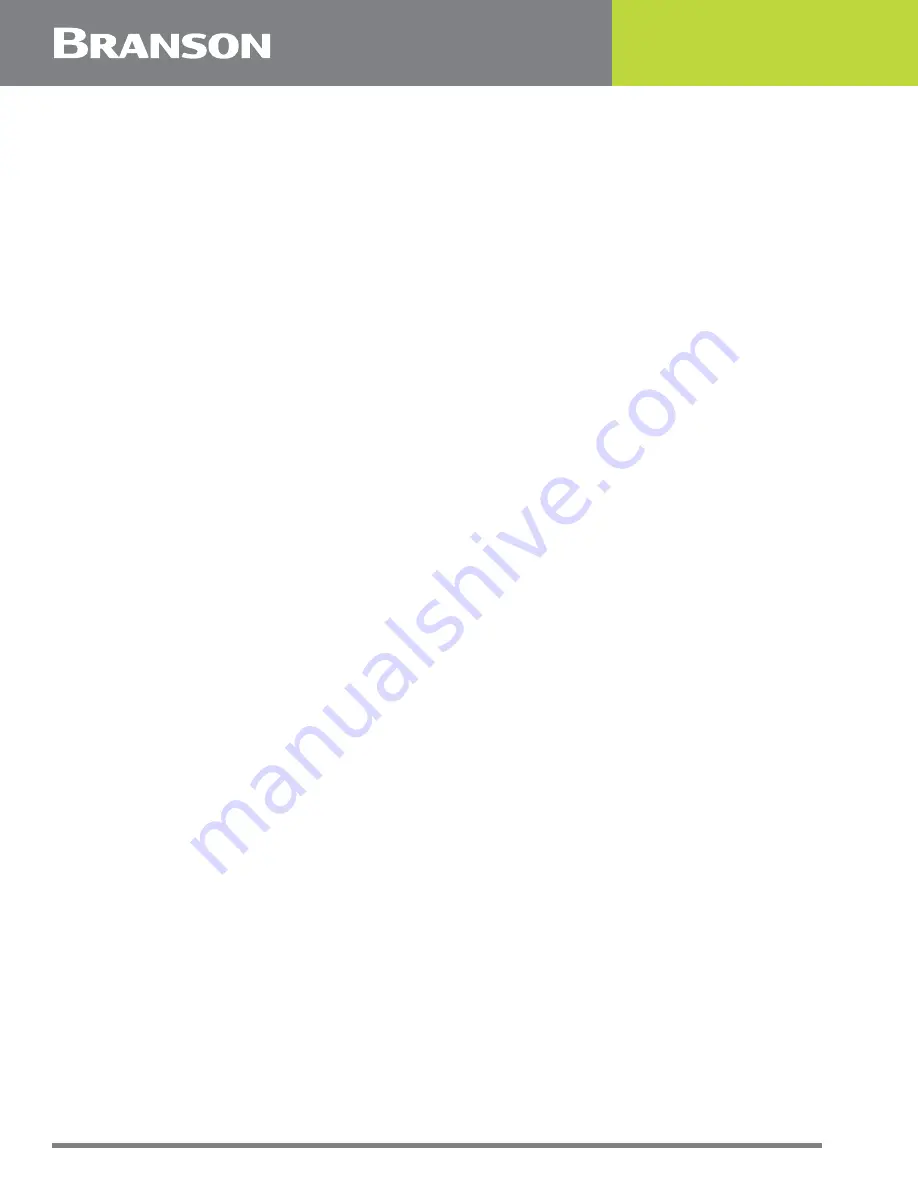
2
100-214-294 REV. 05
1.1
Safety Requirements and Warnings
This chapter contains an explanation of the different Safety Notice symbols and icons
found both in this manual and on the product itself and provides additional safety
information for ultrasonic welding. This chapter also describes how to contact Branson for
assistance.
Summary of Contents for Branson CPX1800
Page 4: ...iv 100 214 294 REV 05 ...
Page 6: ...vi 100 214 294 REV 05 ...
Page 8: ...viii 100 214 294 REV 05 ...
Page 21: ...100 214 294 REV 05 11 Chapter 3 Delivery and Handling 3 1 Unpacking Your Unit 12 ...
Page 35: ...100 214 294 REV 05 27 Chapter 5 Installation and Setup 5 1 Installing Your Unit 28 ...
Page 76: ...72 100 214 294 REV 05 ...