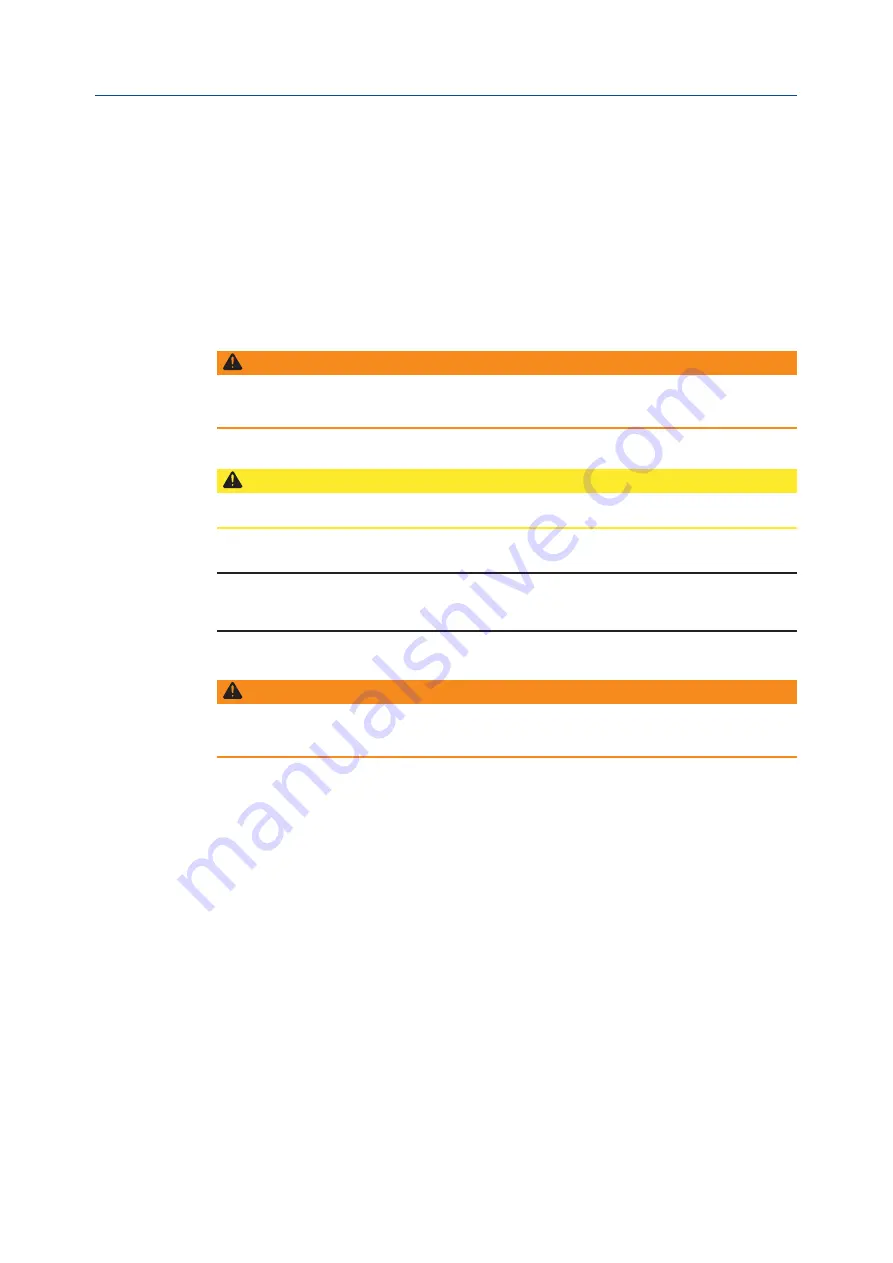
Installation, Operation and Maintenance Manual
MAN-02-05-62-0742-EN Rev. 0
December 2019
Safety
Section 2: Safety
2.1
Warning Levels used in Manuals
The following warning levels are used in the documentation of Bettis for the safety of
people and equipment.
WARNING
Indicates a potentially hazardous situation which, if not avoided, could result in death or
serious injury.
CAUTION
Indicates a potentially hazardous situation which, if not avoided, may result in property damage.
NOTE:
Indicates important information regarding the product.
WARNING
All personnel that handles Bettis actuators shall take part of and understand the
following information prior to handling the system. See warnings on following page.
4
Section 2: Safety