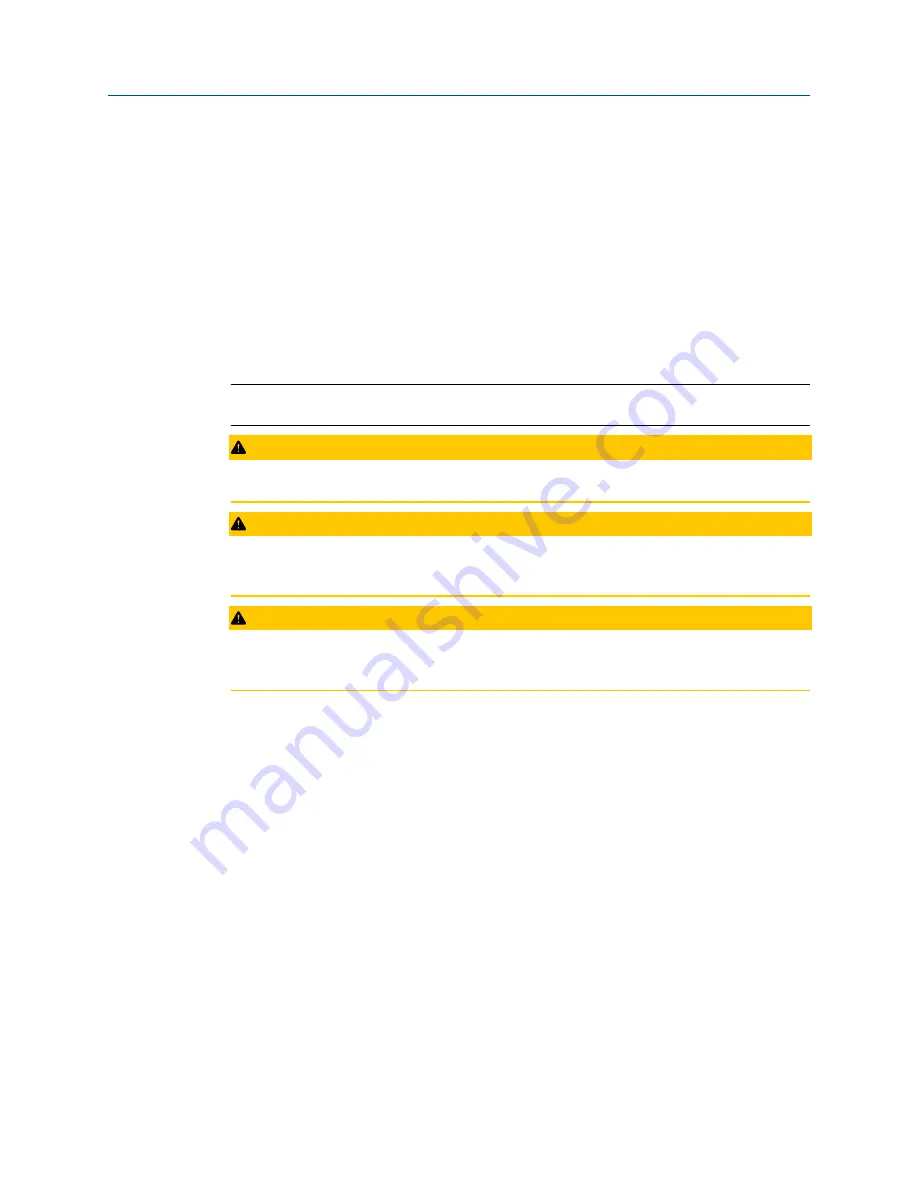
3
Installation
3.1
Device handling
Before beginning the installation process:
Install the Emerson Wireless Gateway and ensure it functions properly before you activate
the AMS Wireless Vibration Monitor or any other wireless devices. Power up wireless
devices in order of proximity from the Emerson Wireless Gateway, beginning with the
closest. This will result in a simpler and faster network installation.
Note
The device requires a standard 1/4–28-inch mounting location.
CAUTION
Do not drop, hammer, or impact the device housing before, during, or after installation.
CAUTION
When installing the device in hazardous locations, ensure that the device is grounded to
the machine case.
CAUTION
If the equipment is used in a manner not specified by the manufacturer or contrary to the
instructions in this manual, the protection provided by the equipment may be impaired.
3.2
Mounting tools and supplies
Mounting tools
•
Drill
•
Spot face or end mill tool
The spot face tool attaches to a standard electric drill and provides a machined surface
that is at least 1.1 times greater than the diameter of the sensor. The spot face tool also
drills a pilot hole that can then be tapped for a stud mounted sensor.
You can purchase the spot face tool from Emerson (MHM P/N 88101), or you can
substitute a spot face tool with similar characteristics as required. Contact your local sales
representative for assistance.
User Guide
Installation
MHM-97927-PBF
August 2020
MHM-97927-PBF, Rev 1
43
Summary of Contents for AMS Wireless Vibration Monitor
Page 1: ...User Guide MHM 97927 PBF Rev 1 August 2020 AMS Wireless Vibration Monitor User Guide ...
Page 42: ...Configuration User Guide August 2020 MHM 97927 PBF 42 MHM 97927 PBF Rev 1 ...
Page 50: ...Installation User Guide August 2020 MHM 97927 PBF 50 MHM 97927 PBF Rev 1 ...
Page 80: ...Product certifications User Guide August 2020 MHM 97927 PBF 80 MHM 97927 PBF Rev 1 ...
Page 82: ...Third party licenses User Guide August 2020 MHM 97927 PBF 82 MHM 97927 PBF Rev 1 ...
Page 85: ...User Guide MHM 97927 PBF August 2020 MHM 97927 PBF Rev 1 85 ...