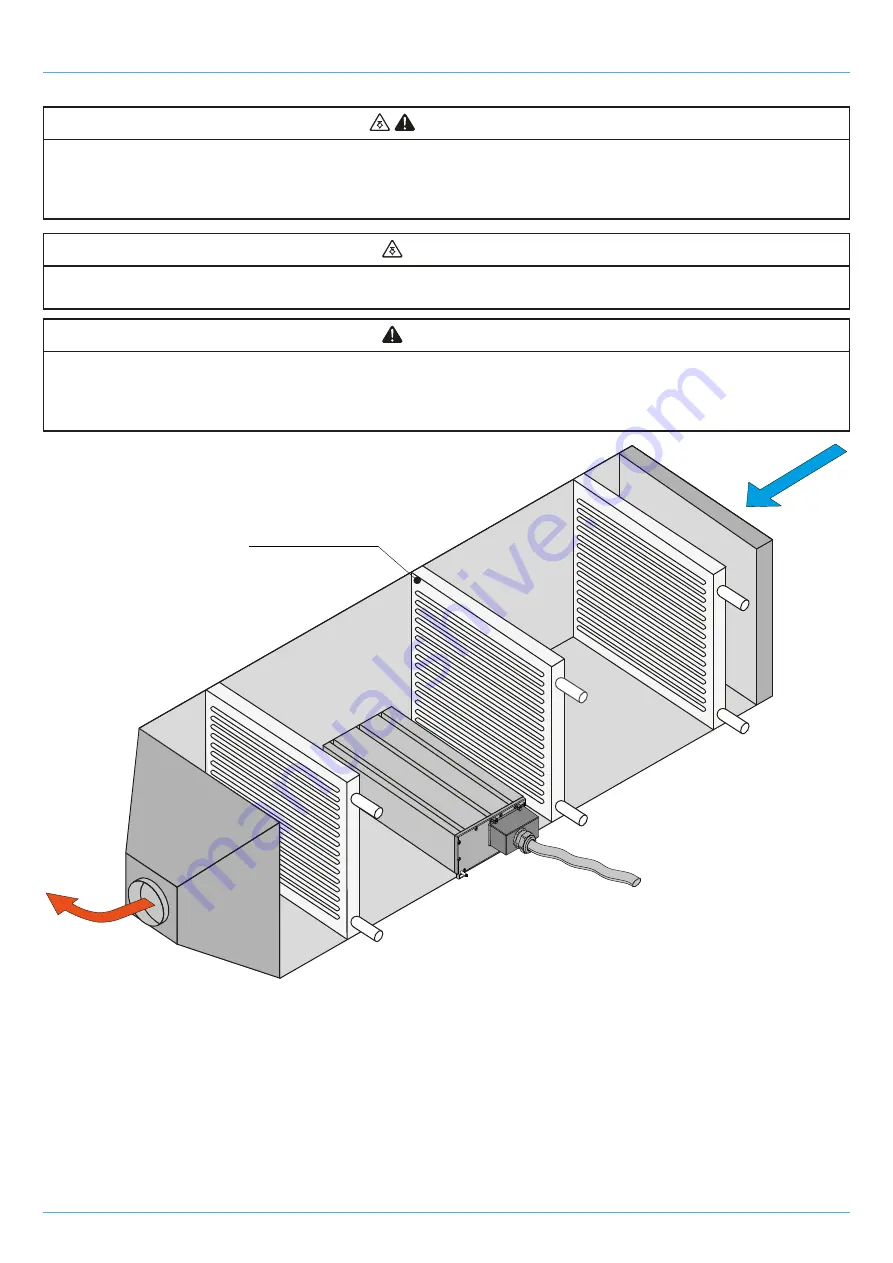
924VHE4.02 -
VEH
series humidifiers
02/2022
|19|
5.4 Steam distribution in the AHU
WARNING
RISK OF BURNS
• The hydraulic unit must be installed so that it cannot be accessed by unauthorised persons.
• The inside of the air treatment unit (where the hydraulic unit is installed) must only be accessed by qualified personnel using
a tool (e.g. a spanner).
WARNING
HOT WATER VAPOUR
Do not touch the equipment while it is running.
WARNING
MALFUNCTIONING OF THE EQUIPMENT
• Install the equipment in a position which ensures the minimum distances from all adjacent structures and equipment as
indicated in this document.
• Install all equipment in compliance with the technical specifications indicated in the relevant documentation.
Cooling
coil
Fig. 9.
Positioning the hydraulic unit in the AHU
NOTE
:inambienttemperatureconditionswhichmayleadtotheformationofice,itiswisetotakeallnecessaryprecautionsto
prevent the supply water and the drain water from freezing and causing the humidifier to malfunction.