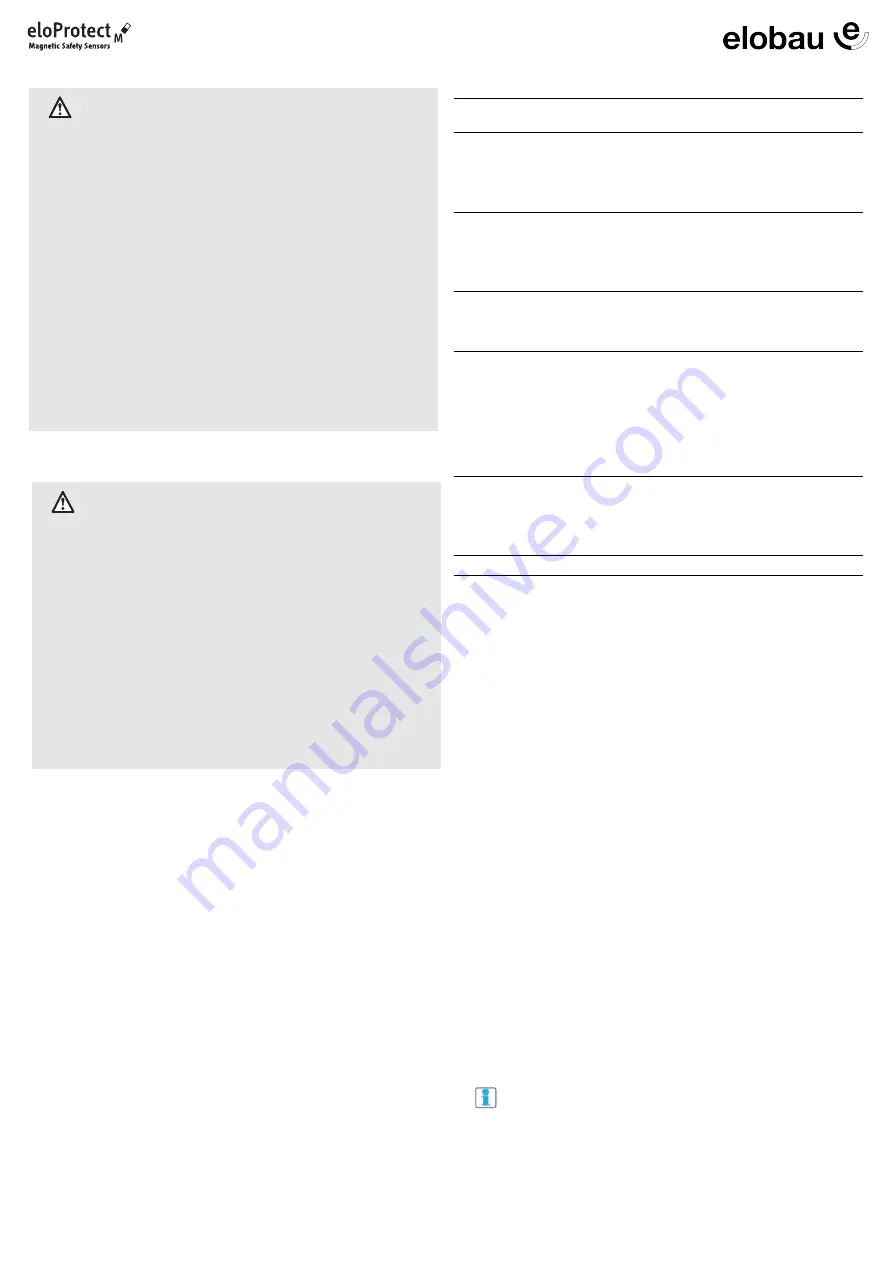
Art.-Nr./Art. No./Réf./N° art/N° art.: 9010002B01M
Version:
1.1
Date:
11.04.2016
2/1
1
4
Safety instructions
5
Warning against misuse
6
Exclusion of liability
No liability shall be accepted for any damage or operational faults caused by a
failure to observe these operating instructions. All further liability of the
manufacturer is excluded in the case of damage caused by the use of
replacement and accessory parts that have not been authorized by the
manufacturer.
No unauthorized repairs, conversions or modifications are permitted for reasons
of safety and the manufacturer shall not be liable for any damage resulting
therefrom.
7
Function
A coded magnetic safety sensor with a non-contact activation through a coded
actuator.
(Type 4; low coding level according to EN ISO 14119)
An elobau safety control unit or similar safety processing unit / safety controller
analyses the switching state of the safety sensor. PDF-M and PDF-S is
achieved only in combination with the elobau safety control units listed below or
comparable safety control units / safety controllers.
The safety sensors are suitable for the following elobau safety control units:
- Ensure that the safety sensors are only mounted and put into
operation by specially-trained and authorised personnel.
- Only install and put the device into operation once you have
read and understood the operating instructions and are familiar
with the applicable regulations on occupational safety and
accident prevention.
- The safety sensor may only be activated by a correctly mounted
actuator on the safety device. Actuation by a spare actuator that
is not mounted to the safety device is prohibited.
- The safety sensors may only be operated in a perfect function-
ing condition.
- Ensure that the safety sensors are exclusively used to protect
against risks.
- Ensure that all of the valid safety regulations for the respective
machine are complied with.
- Ensure that all of the valid laws and directives are complied with.
- Connecting safety sensors in series can, under certain
circumstances, reduce their performance level according to
EN ISO 13849-1 standards due to a lower detection of errors.
- There are no known residual risks, if all of the information
contained in these operating instructions is complied with.
- In case of incorrect or unintended use or manipulation, the use
of the safety sensors does not exclude risks to persons or
damage to machine or system components.
Please also observe the relevant information stipulated in
EN ISO 14119.
- Please ensure that when using safety control units that have not
been supplied by elobau, no current or voltage peaks which are
higher than the specified electrical data of the safety sensor are
generated by these devices. Current or voltage peaks are
produced, for example, by capacitive or inductive loads.
- The safety sensor is not short-circuit proof.
- An exceeding of the electrical data of the safety sensor (e.g. in
the event of incorrect wiring or short-circuits) may cause
irreparable damage to the sensor.
- The safety sensor may only be activated in the approved control
options (see Technical specifications).
Non-compliance with this information may result in reduced
service life of the safety sensor.
PDF-M according to EN 60947-5-3:1999 + A1:2005
(corresponds to PLe /Cat.4) for:
470...
470EFR3E11K_
470EFR3E12K_
471...
471M41H31
471EFR3E11K_
471EFR3E12K_
471EFR3E13K_
471EFR3E14K_
eloProg
485EPB
485EPE08A02
485EPE08
4854EPE12
485EPE16
PDF-S according to EN 60947-5-3:1999 + A1:2005
(corresponds to PLd /Cat.3) for:
463...
463111B1
463111B2
463114B1
463114B2
463111B101
463114B101
463121B1
463124B1
470...
470111B1
470115B1
470121B1
470125B1
470EFR2D12K_
471...
471EFR2D14K_
8
Technical specifications
See Technical specifications beginning on page page 14.
9
Installation
- Safety sensor and actuator
do not use as end stops
do not install in strong magnetic fields
do not expose to any strong shocks or vibrations
keep away from iron filings
- The safety sensor and the accompanying actuators may only be mounted in
a voltage-free state.
- Ensure that all safety sensor and actuator markings are congruently
opposed to one another.
- The installation position is arbitrary. The safety sensor and actuator must
however be mounted in parallel, facing each other.
- Please note the specified installation tolerances and the approved control
options.
- Since the safety sensor is a non-embeddable proximity switch (in
accordance with EN 60947-5-2), the safety sensor and the actuator should
be mounted on non-ferromagnetic material. A free zone of 25 mm is required
in the event that this cannot be avoided.
- Where possible, the safety sensor and actuator should not be mounted on
ferromagnetic material. Changes to the switching distances are to be
expected. A non-ferromagnetic spacer with a thickness of at least 10 mm
must be used in order to avoid influencing the switching distances. The
above-mentioned free zone still applies to the safety sensor and actuator.
- The mounting distance between two safety sensor and actuator systems
must be at least 50 mm.
- Tightly fasten the safety sensor and actuator to the safety device.
Suitable spacer plates for the safety sensor and actuator are
available from elobau under order number 350008.