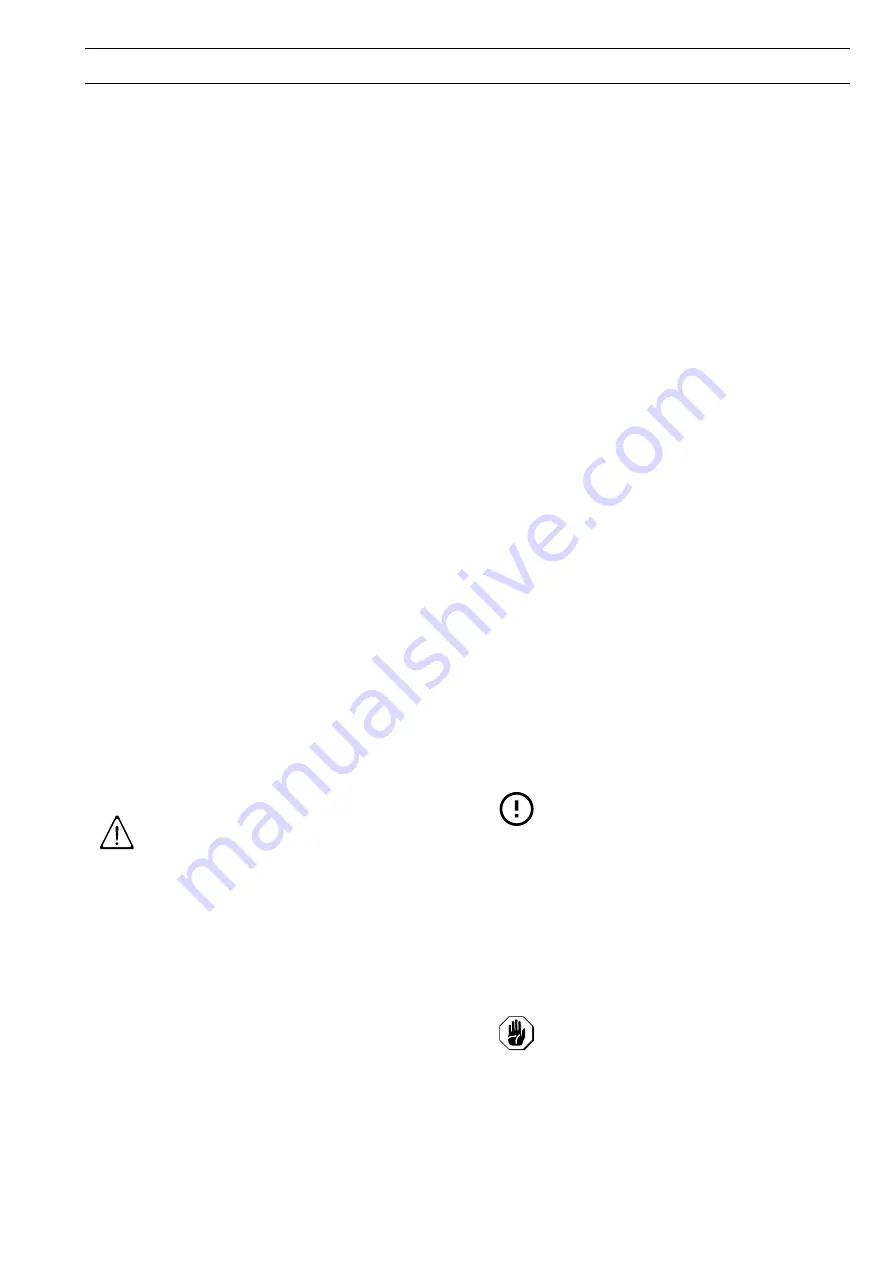
27
H
GAS INSTALLATION
H.1
Gas, electricity, water and other
connections (if present, depending on
the appliance and/or model)
• Any installation work or maintenance to the supply system
(gas, electricity, water and/or steam, if present) must only
be carried out by the utility company or an authorised
installation technician.
• Refer to the appliance dataplate for the product code.
• See the installation diagram for the type and position of
appliance connections.
H.2
Mains connection
The following regulations must be obeyed when installing
testing and adjusting the equipment:
• The legal regulations in force;
• In absence of local codes, the installation must be confirm
with the National Fuel Gas code, ANSI Z223.1 / NFPA 54, or
the Natural Gas and Propane Installation Code, CSA
B149.1, as applicable, including
– The appliance and its individual shutoff valve must be
disconnected from the gas supply piping system during any
pressure testing of that system at test pressures in excess
of ½ psi (3.5 kPa)
– The appliance must be isolated from the gas supply piping
system by closing its individual manual shutoff valve during
any pressure testing of the gas supply piping system a test
pressures equal to or less than ½ psi (3.5 kPa).
• State building regulations and fire regulations;
• DVGW work sheet G 600 (TRGI) “Technical regulations for
gas installations“;
• TRF “Technical regulations for liquid gas“;
• DVGW work sheet G 631;
• Accident prevention regulations in force;
• Gas supply company conditions;
• SVGW guidelines;
• State and local regulations.
The appliance must not be installed on flammable walls; the
installation area and the contact surface must be tiled or made
of an equivalent material that is temperature resistant and
thermally insulated.
If the appliance is set up next to temperaure-sensitive furniture
or similar, a safety gap should be maintained; the paragraph F
shows the exact gap required.
WARNING
• No inflammable materials or fuels must be stored in the
vicinity of the appliance.
• Kitchens and associated areas must be ventilated by
ventilation equipment so that the ambient air is polluted as
little as possible with unpleasant odours, gaseous combus-
tion products (such as exhaust gas).
• Ventilation systems must not be covered with anything.
• Do not obstruct the flow of combustion.
• Assure adequate clearance for air openings into the
combustion chamber.
• Gas feed parts (such as screwed-on gas pipes) on gas
consuming devices must be so firmly sealed that under test
conditions specific leak rates are not exceeded.
• Only sealing material that has been approved by the
relevant test centres for use with all types of gas must be
used.
• Clean dust, dirt and deposits that could prevent the gas
supply flow from the connection pipes; we recommend that
a dirt filter is installed in the gas pipe at the customer’s.
• The gas supply line must ensure the gas flow necessary for
full operation of all the appliances connected to the system.
A supply line with insufficient flow will affect correct
operation of the appliances connected to it.
• If the gas feed pipe (flow, diameter, etc.) and/or upstream
gas valve are not designed correctly this may adversely
affect the gas combustion by the burner system and the
operation and operational safety of the appliance; consid-
erable risk of misuse;
When the unit is delivered, it is already set to the gas type
specified when ordering; the pressure and gas type are
indicated on the data plate.
Compare the information on the data plate with the gas data of
the installation location.
H.3
Conversion to another type of gas
Nozzle table (spare parts catalogue or service manual) gives
the type of nozzles to be used when replacing those installed
by the manufacturer (the number is engraved on the nozzle
body).
At the end of the procedure, carry out the following check-list:
1. burner nozzle/s replacement
2. correct adjustment of primary air supply to burner/s
3. pilot nozzle/s replacement
4. minimum flame screw/s replacement
5. correct adjustment pilot/s if necessary
6. correct adjustment of supply pressure (see technical data/
gas nozzles table)
7. apply sticker (supplied) with data of new gas type used
8. check if the date of the changing is visible
H.4
Fume exhaust
The appliances are all type A1.
We never use direct exhaust gas flues that need connecting to
a system; hence there is no need for a category B type flue.
However, if a category B flue is expressly requested, this type
of connection requires its own certification.
Combustion air and combustion products are extracted in the
installation area.
According to the definition of Technical Installation Regulations
DVGW G631: March 2012, these appliances have to be
positioned under an extraction hood to ensure removal of
fumes and steam produced by cooking.
IMPORTANT
• If the overall output of all appliances in the room
exceeds 14 kW, in addition to the shut-off and
safety devices required by DVGW G600, the
exhaust flue must be fitted with a monitoring
system. This means that the gas can only be
released to the burners if it is released because
the ventilation system is in use.
• You must also ensure combustion air is supplied
when the total load exceeds 14 kW. In spaces
without openings to the outside, there must be
an air-conditioning system in accordance with
VDI 2052 to ensure pressure between the
kitchen and adjacent rooms is equalized.
CAUTION
• Never block the extractor;
• Never apply structural changes or
modifications to the chimney (refer to
A.11
Reasonably foreseeable improper
H.5
Before connecting
Make sure the appliance is arranged for the type of gas to be
used.