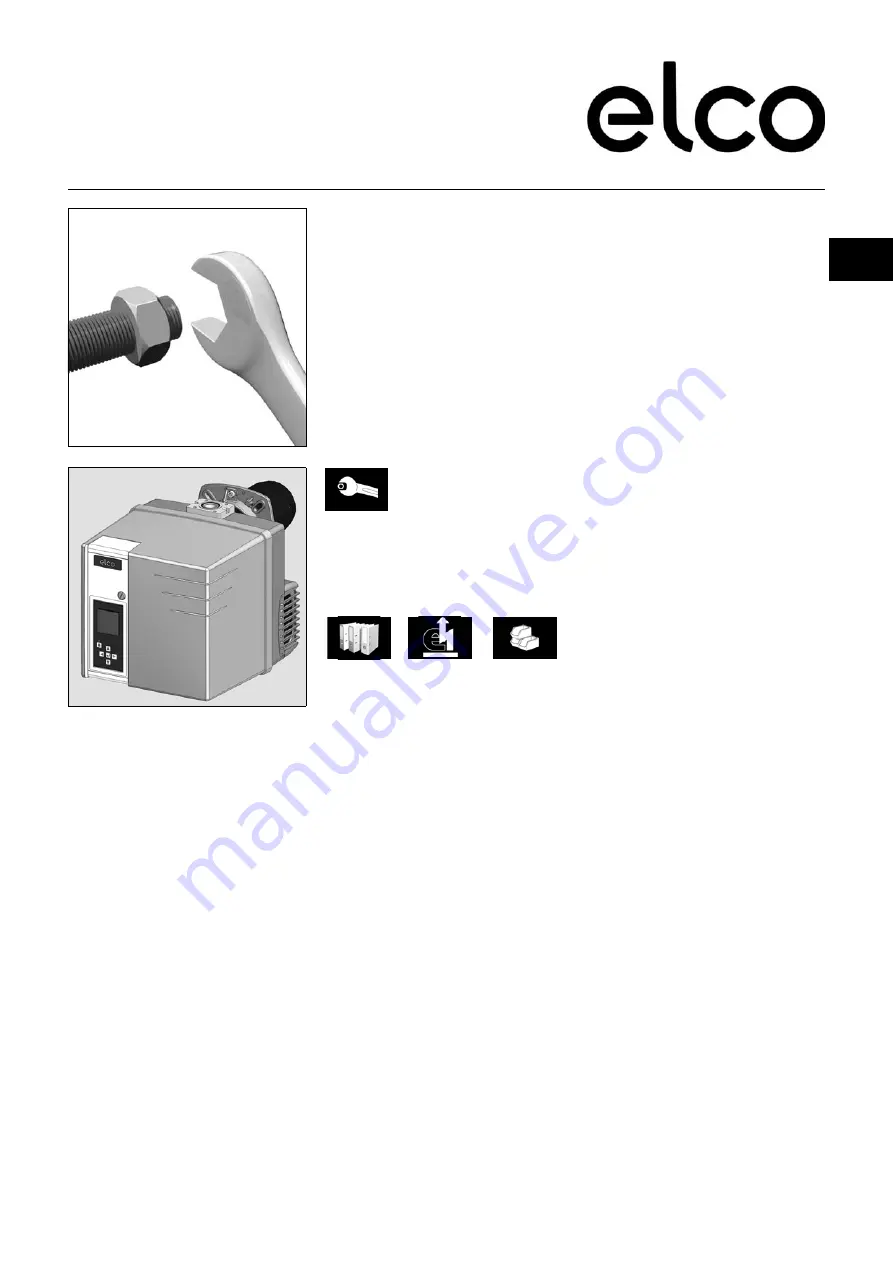
09/2014 - Art. Nr. 4200 1038 2700A
Original operating instructions
For authorised specialist engineers
Gas burners ........................................... 2-31
en
VG2.120 M/TC
VG2.160 M/TC
VG2.210 M/TC
de, fr..................................... 4200 1038 2500
it, nl ...................................... 4200 1038 2600
............................................. 4200 1038 2400