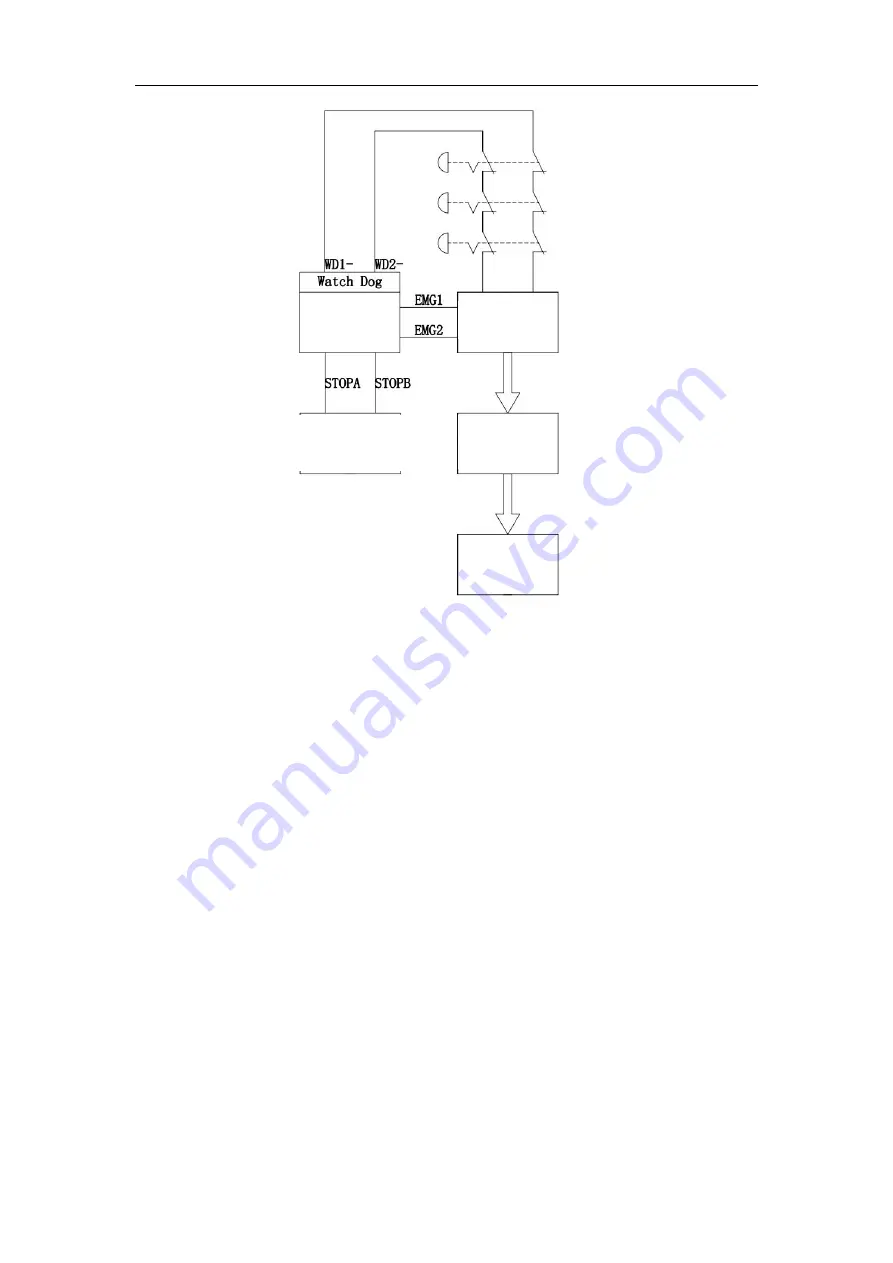
Electrical Operation and Maintenance Manual for ER15-1400 Industrial Robot
40
Fig. 3-19 Block Diagram of the Safety Control Loop
3.4.1 Electrical Hardware
The safety loop adopts dual loop redundancy design, and the signal source type is test pulse.
The signal output by the safety relay S11
、
S21 first passes the controller WD signal
(commonly known as "watchdog"; this signal is disconnected when the controller has an error, and
the emergency stop is triggered), then passes through the teach pendant emergency stop double
circuit, and series the emergency stop on the panel of the electric cabinet, the user emergency stop,
and finally the circuit returns to the safety relay S12
、
S22 to realize the control of the safety
circuit.
The output adopts a dual-circuit design that takes into account both hardware and software.
In terms of hardware, the safety relay output controls the servo drive STO. When an emergency
stop is photographed, the STO signal is directly cut off, an emergency stop instruction is issued to
make the robot stop urgently, and the motor brake is closed at the same time.
The stopping mode adopted by this robot product is to stop category 1.
3.4.2 Software
In terms of software control, when the emergency stop is pressed, the software will receive
dual-loop signals of emg1 and emg2 powered by the safety circuit. Any action will cause the
emergency stop signal to be triggered. The dual-loop watch dog communicates with the robot
controller. When the robot software error occurs, the watch dog (equivalent to the normally closed
the motion
controller
external security
door signal
the emergency stop of the teach pendant
the emergency stop of the control cabinet
the external emergency stop
safety relay
servo
drives
servo
motor