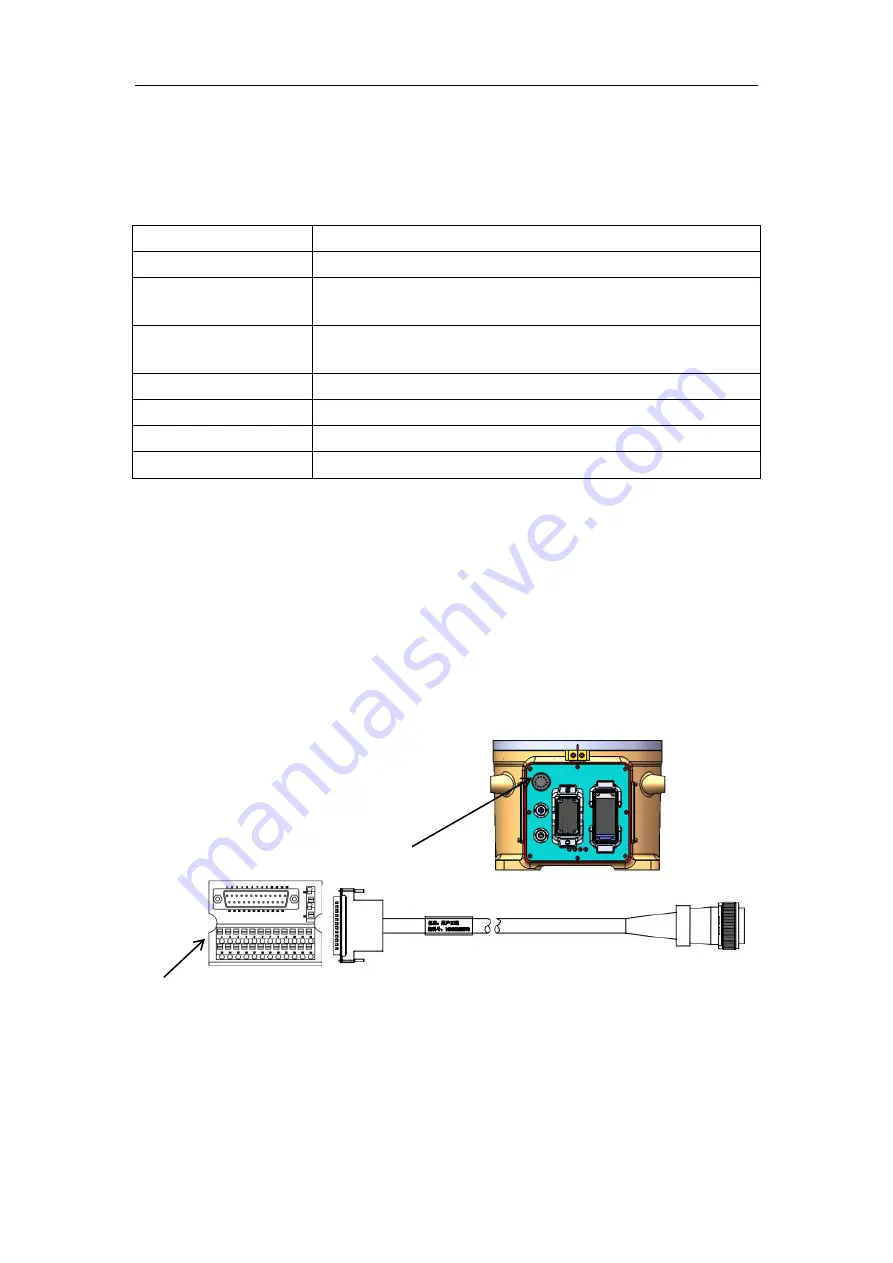
Electrical Operation and Maintenance Manual for ER15-1400 Industrial Robot
20
body side
electric cabinet side
Fig.2-5 Interface position diagram
Table2-6 Description of Various Cables
Cable Type
Description
power supply cable
provide AC 220V for the control cabinet
robot power and brake
cable
transfer the driving power from the driving device in the control
cabinet to the robot motor
robot encoder cable
transmit the encoder data to the drive serial measurement circuit
board
teach pendant cable
exchange signals between teach pendants
brake release cable
connect brake release unit and control cabinet
Robot grounding cable
connect the robot body with the equipotential control cabinet
Φ10 air pipe
two Φ10 air pipes, supply power to the fixture
The left side of the control cabinet is equipped with an M25*1.5 cable lock, which has been
sealed with sealing plug before delivery. Users must ensure its sealing when using, otherwise the
overall sealing of the control cabinet will be damaged.
2.4.3
The IO cable of the robot body base
The IO cable of the robot body base is the signal cable inside the body, the external input of
the harness is DB25 core plug, which can be connected to the DB25 extension terminal block.
This signal can be connected to the PLC, and also can be connected to our IO extension terminal
block, which can realize the flexible control mode of signal source. The body side is 25 core round
connector.
Fig. 3-4 Diagram of IO cable connection at the user base
IO wire harness is built into the robot body, and the number of cores is 25. The following
figure shows the pin definition of IO wire harness:
Grounding
bolts
body IO signal expansion
terminal block
IO cable port on
the body side