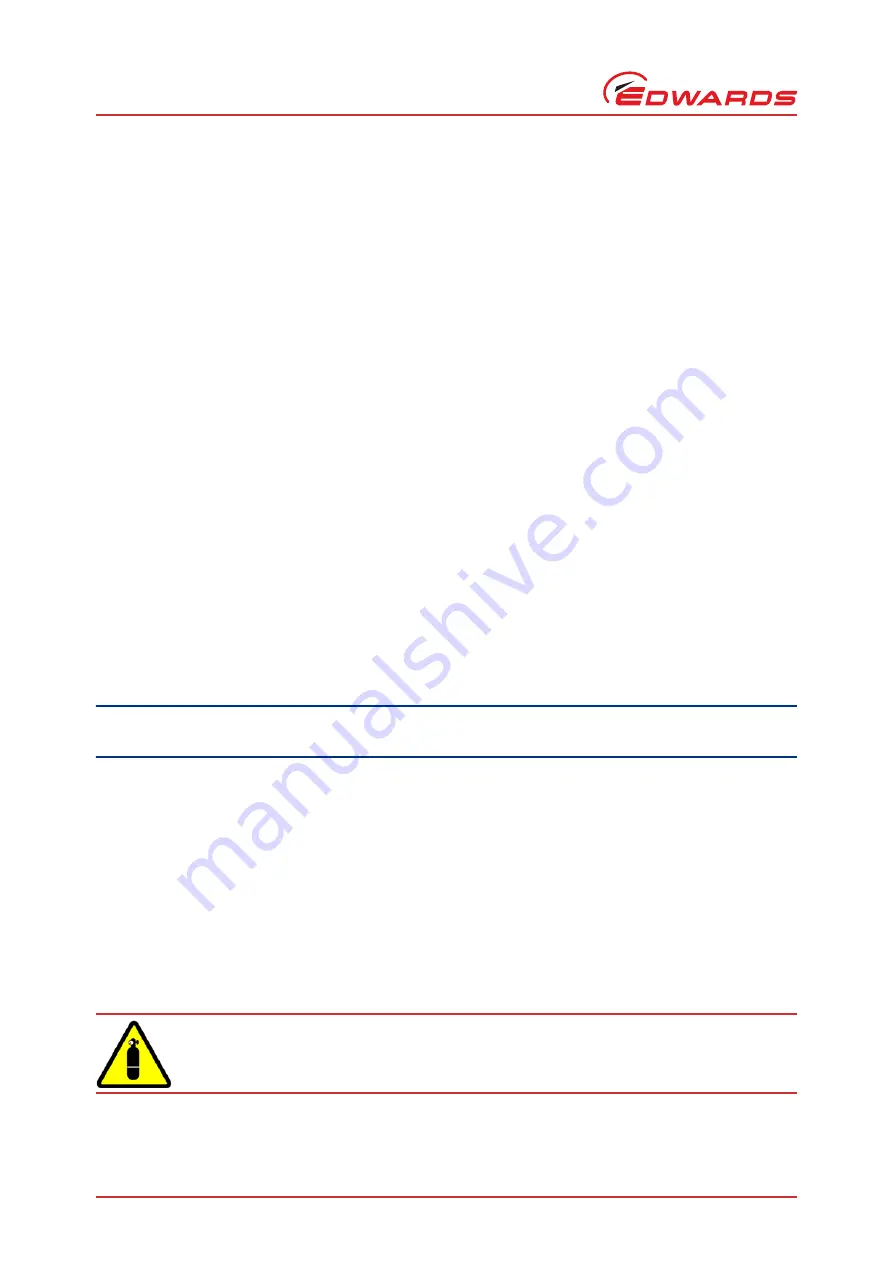
A732-01-880 Issue A
Page 16
© Edwards Limited 2010. All rights reserved.
Edwards and the Edwards logo are trademarks of Edwards Limited.
Operation
4.5
Implication of ATEX directive
4.5.1
Introduction
This equipment is designed to meet the requirements of Group II Category 3 equipment in accordance with Directive
94/9/EC of the European Parliament and the Council of 23rd March 1994 on the approximation of the laws of the
Member States concerning equipment and protective systems intended for use in potentially explosive atmospheres.
(The ATEX Directive).
The ATEX Category 3 applies in respect of potential ignition sources internal to the equipment. An ATEX Category has
not been assigned in respect of potential ignition sources on the outside of the equipment as the equipment has not
been designed for use where there is an external potentially explosive atmosphere.
There is no potential source of ignition within the pump during normal operation but there may be potential sources
of ignition under conditions of foreseeable and rare malfunction as defined in the Directive. Accordingly, although
the pump is designed to pump flammable materials and mixtures, operating procedures should ensure that under all
normal and reasonably foreseeable conditions, these materials and mixtures are not within explosive limits.
4.5.2
Flammable/pyrophoric materials
When flammable or pyrophoric materials are present within the equipment you must:
z
Not allow air to enter the equipment.
z
Ensure the system is leak tight.
z
Dilute and flammable gases or vapours by using an inert purge (such as N
2
) to the pump inlet and or gas purge
of the primary pump backing the XDS100B. Concentration levels of the gas or vapour within the pumps and
exhaust lines should be reduced to less than one quarter of their published lower limits (LEL).
4.5.3
Gas purges
CAUTION
The following actions must be taken to ensure that the gas being pumped stays out of the flammable range.
The inert gas purge into the pump inlet or gas purge of the primary pump backing the XDS100B should be switched
on to remove air from the pump and exhaust before the process starts. The purge flow can be switched off at the
end of the process only after any remaining flammable gases or vapours have been purged from the pump and exhaust
line.
If liquids that produce flammable vapours could be present in the pump foreline then the inert gas purge to the
XDS100B should be left on all the time this liquid is present. Flammable liquids could be present in the foreline as a
result of condensation or may be carried over from the process.
When calculating the flow rate of inert gas required for dilution, consider the maximum flow rate for the flammable
gases/vapours that could occur. For example, if a mass flow controller is being used to supply flammable gases to
the process, you should assume a flow rate for flammable gases that could arise if the mass flow controller is fully
open. The inert gas purge flow rate should be continually measured and if the flow rate falls below that required,
then the flow of flammable gases or vapours to the pump must be stopped.
We recommend you obtain and read Vacuum Pump and Vacuum System Safety publication no P300-20-000
available from Edwards or your supplier.
WARNING
If you use a purge to dilute dangerous gases to a safe level, ensure that the system shuts down if
the purge gas supply fails.