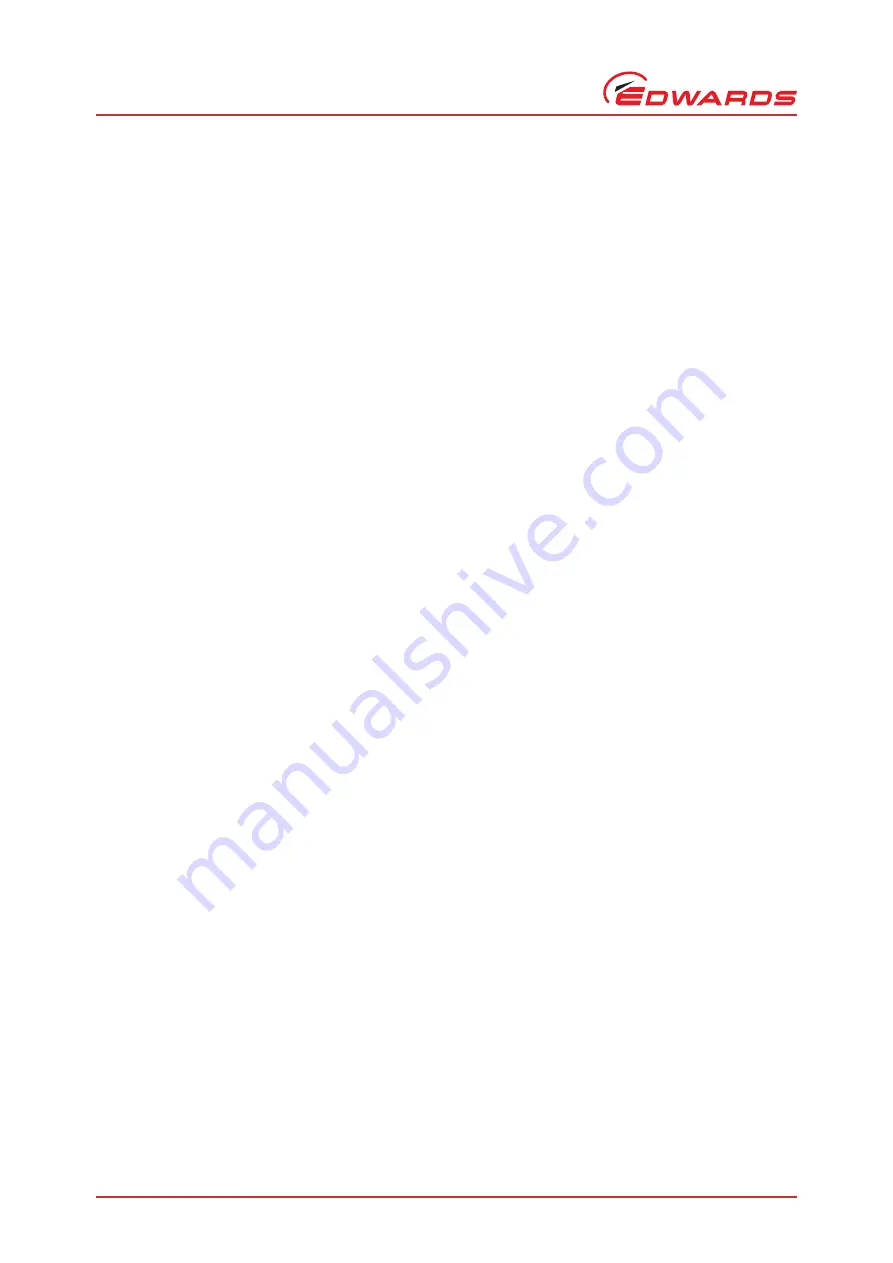
B722-20-880 Issue D
Page 2
© Edwards Limited 2008. All rights reserved.
Edwards and the Edwards logo are trademarks of Edwards Limited.
Introduction
1.2
General description
The EXT70H 24 V, EXT70Hi 24 V, EXT255H 24 V and EXT255Hi 24 V pumps are compound vacuum pumps that combine
a turbomolecular pump and a drag pump on a single shaft. The turbomolecular pump is made from a multi-stage axial-
flow turbine which is optimised for operation in molecular flow conditions. The drag pump is designed for operation
at higher pressures than conventional turbomolecular pumps.
The angled blades of the turbomolecular pump are machined from a single piece of material. For the blades to be
effective, their speed must be close to the thermal velocity of the gas. The rotor of the EXT70H/Hi 24 V therefore
rotates at up to 90000 r min
-1
, and the rotor of the EXT255H/Hi 24 V rotates at up to 60000 r min
-1
.
Gas from the inlet is compressed through each of the bladed stages of the turbomolecular pump and transferred to
the drag pump. In the drag pump stages the gas is further compressed.
The rotating assembly is supported at the inlet end by a frictionless magnetic bearing and by a precision ceramic ball
bearing at the outlet end. The ball bearing is lubricated from an oil reservoir and wick mechanism.
The EXT pump is supplied with an inlet-screen fitted in the bore of the inlet-flange. The EXT255Hi 24 V pump is also
supplied with an inlet-strainer which fits in the interstage-port. The inlet-screen and inlet-strainer protect the pump
against damage which would be caused by debris entering the pump. The inlet-screen also serves to protect the user
against injury from the sharp blades in the pump.
The EXT pump has a vent-port for venting the pump and vacuum system to atmospheric pressure. The pump is
supplied with a manual vent-valve fitted to the vent-port. As described in
, the manual vent-valve can be
replaced with a TAV5 or TAV6 solenoid-operated vent-valve (available as an accessory: see
).
The EXT255H 24 V and EXT255Hi 24 V pumps have a purge-port in the motor and bearing housing chamber. An inert
purge gas can be introduced through the purge port in order to protect these parts from corrosion or the bearing
lubricant from oxidisation. An optional vent-port adaptor and purge restrictor can be fitted to the purge-port to
control the flow rate of the purge gas and to filter the gas supply (see
).
The EXT255Hi 24 V pump has an interstage-port between the turbomolecular and drag stages. If required, an
interstage-port accessory can be fitted to an EXT70H/ISO63 24 V pump to upgrade it to an EXT70Hi 24 V pump (see
). The interstage-port on EXT70Hi 24 V and EXT255Hi 24 V pumps can be used to pump a separate chamber
of the vacuum system or to back another turbomolecular pump.
If the EXT70Hi 24 V pump operates with an outlet pressure of less than 5 mbar (500 Pa) and an interstage inlet flow
of less than 100 sccm (1.69 mbar l s
-1
, 169 Pa l s
-1
) the vacuum performance at the turbomolecular pump-inlet is
independent of the interstage operating conditions.
If the EXT255Hi 24 V pump operates with an outlet pressure of less than 5 mbar (500 Pa) and an interstage inlet flow
of less than 70 sccm (1.17 mbar l s
-1
, 117 Pa l s
-1
), the vacuum performance at the turbomolecular pump-inlet is
independent of the interstage operating conditions.
An EXDC 24 V Drive Module is used to control the EXT 24 V pump. The EXDC 24 V Drive Module is fitted directly to the
19-way connector on the pump.
The pump may be cooled using air-cooled or water-cooled optional accessories. Refer to
for guidance on
applications and cooling requirements. Pumps with a Conflat flange are supplied with a water-cooler.
All EXT pumps have thermal sensors to monitor the motor and pump-body temperature.
1.3
Vent options and vent control
To maintain the cleanliness of the vacuum system, it is recommended that, whenever the pump is switched off, the
pump (or vacuum system) is vented when the speed of the EXT pump is between full rotational speed and 50% of full
rotational speed. At and above 50% of full rotational speed, the rotor spins fast enough to suppress any backstreaming
of hydrocarbon oil from your backing pump.
However, if the pump is vented when it is at full rotational speed and the rate of pressure rise is too high, the pump
life may be reduced. It is therefore recommended that either the rate of pressure rise is limited (see
), or
that the vent-valve is only opened after the EXT pump speed has fallen to 50% of full rotational speed.