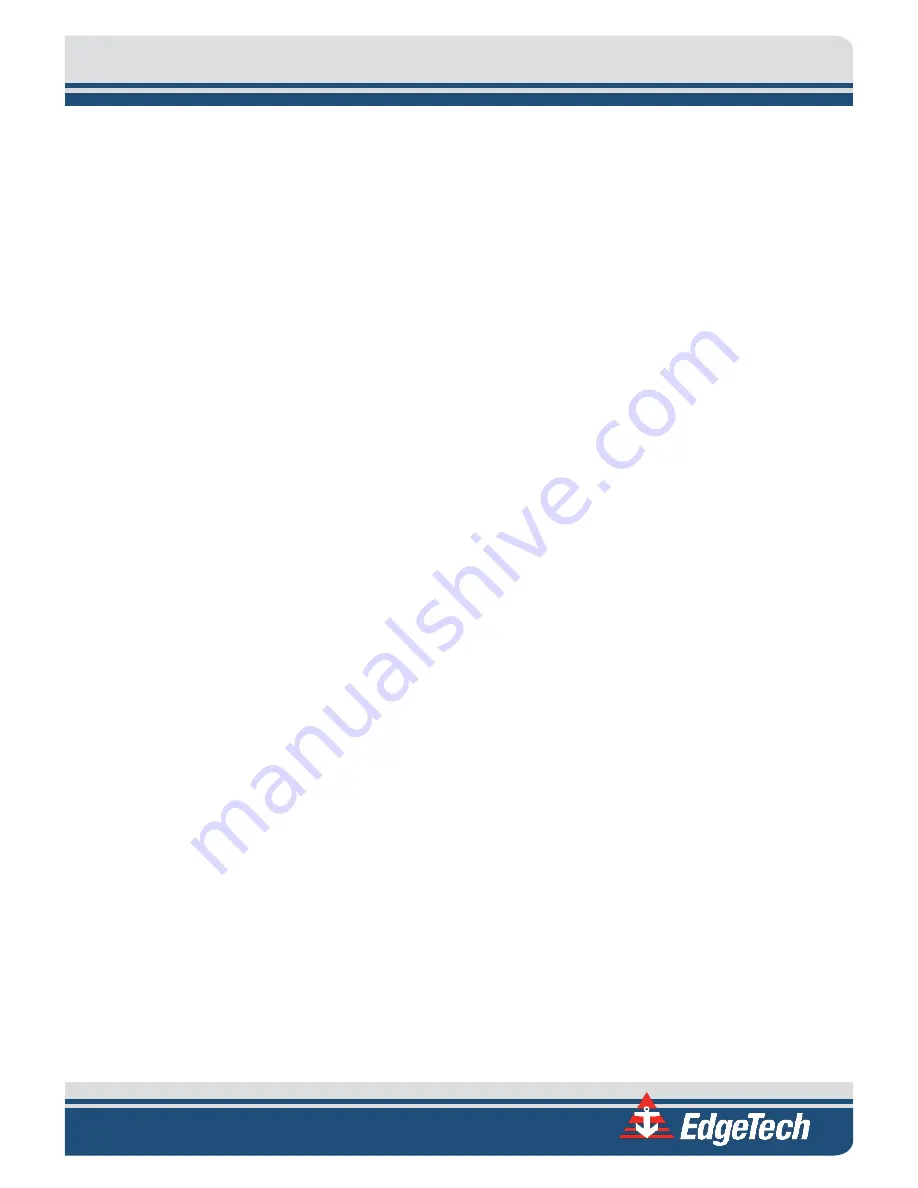
6-5
The main objective is to get the basic system working. It is therefore good practice to disengage any option
circuit cards installed in the unit and optional external system components now to reduce the number of
possible trouble sources.
6.3.1
Equipment Required
Except for the topside processor/power unit, only common laboratory test equipment and tools are
required for field troubleshooting. No special equipment is necessary. Typical test equipment includes:
•
Digital multi-meter, Fluke or equivalent
•
Oscilloscope
•
Hi-pot tester
•
Capacitance meter
6.3.2
Transmission Verification
The 512C and 670D Tow Vehicles are different than that of conventional side scan sonars used for many
years. The early sonars were driven with a high-powered energy burst similar to hitting a bell with a
hammer. The transducers are driven with a smooth rising lower power signal that matches the transducer
response. Because of this, there is no pronounced clicking noise emanating from the transducers when
they are firing. Therefore, the ‘listen for the clicking noise’ test cannot be used to verify sonar transmission
during bench or on-deck testing.
Sniffing with an oscilloscope can be used as a substitute to check transducer firing. One way is to attach
the scope probe’s ground to the tow vehicle body and hold the open probe next to the transducer under
test. Set to about 20 to 50mV /Div.
A second method is to connect a several-turn wire loop across the scope probe and move it over the
transducer face. Electrical pickup should be noticed on the scope screen at each transmission burst.
Remember that the transducers and elements within the transducer may be firing together or in
sequence. One must make sure that the electrical pickup is not from an adjacent string.
6.3.3
Sonar Processor and Data Link
It is assumed that the sonar processor is up and working to complete system test and troubleshooting.
Refer to the sonar processor’s manual for its troubleshooting and diagnostic information.
The other thing is that the high-speed data must be up and running so that the topside and sub-sea units
are communicating with each other. If the tow vehicle boots up correctly and passes its internal self-test,
there will be a smooth sequence of rising tones going from 2 to 3.9 kHz. A set of tones jumping from 2 to
3 kHz means that self-test has failed. These tones are generated in software in the tow vehicle and
replicated on the surface when an EdgeTech topside processor is used to access the Tow vehicle computer
subsystem using the Remote Desktop application. The Self-Test PASS tones repeat until data linkup has
Summary of Contents for 2000-DSS
Page 20: ......
Page 56: ...Figure 4 2 2000 Digital Telemetry Link Electronics Block Diagram...
Page 57: ...Figure 4 3 2000 Digital Telemetry Link Wiring Diagram...
Page 59: ...Figure 4 4 Tow Vehicle Electronic Block Diagram...
Page 60: ...Figure 4 5 Tow Vehicle Interconnect Drawing...
Page 63: ...Figure 4 6 Armored Cable PMI Grip Unterminated Topside...
Page 64: ...Figure 4 7 Test Cable...
Page 77: ...5 13 Figure 5 16 Magnetic Declination Estimated Value Screen...
Page 79: ...5 15 getDeclination CR Figure 5 18...
Page 80: ......
Page 94: ......
Page 96: ......
Page 98: ......