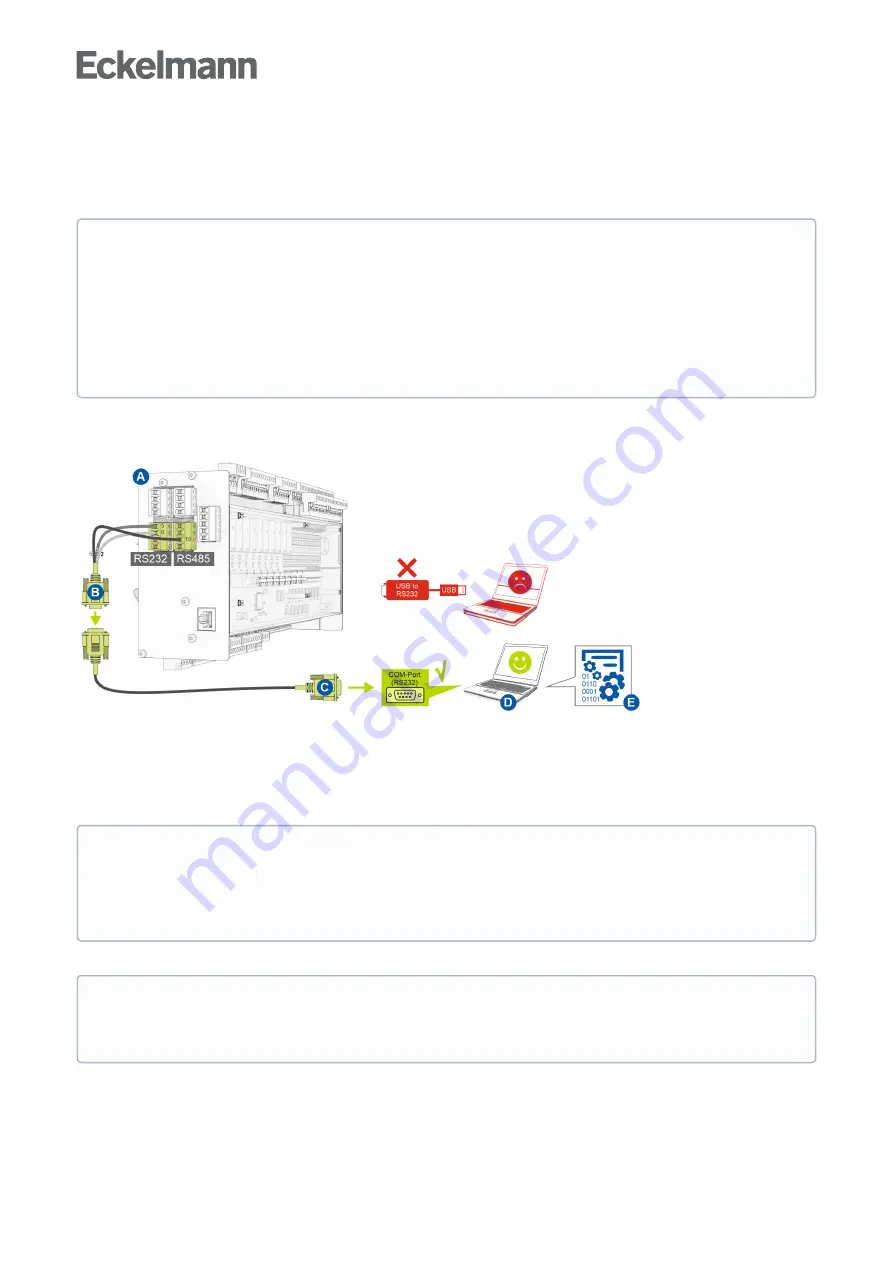
Firmware: V2.18 / V--
26.10.2022
85/119
9.5 Firmware Update
The controller is delivered with the current firmware, ready for operation. Future software releases (e.g. with
extended range of functions) can be loaded via a firmware update to update the controller.
9.5.1 Requirements for firmware update
The following requirements are necessary for a firmware update:
(A)
Controller
(B)
Flash cable, part number KABLINDAD1
(C)
Null modem cable, part number PCZKABSER2
(D)
Notebook with COM port interface (RS232)
(E)
File for the firmware update.
The current file for the firmware update is available in the EDP under
https://edp.eckelmann.de/edp/lds/
ATTENTION
Damage to the installation and stock loss! Before
the firmware update, the affected system
component or the system must be brought into a safe state as the shutdown of the controller during the
firmware update can have undesired effects on the system component and/or the system.
Caution: data loss!
When changing the firmware version, all adjusted setpoint values are lost. As a
precaution, the settings
should
therefore be backed up by saving them using the LDSWin PC software
before
the firmware update. After the firmware update, the saved settings can be reloaded into the
controller from LDSWin.
If no RS232 interface is available on the notebook (or PC), this must be equipped with an
RS232
interface
:
Notebook
: PCMCIA COM port adapter
PC
: PCI COM port card
IMPORTANT:
A USB COM port adapter is expressly
not
recommended!
ATTENTION
It must
strictly
be ensured that the appropriate firmware update version for the controller is used!
Note:
If necessary, it must be unpacked from the ZIP archive
before
use.