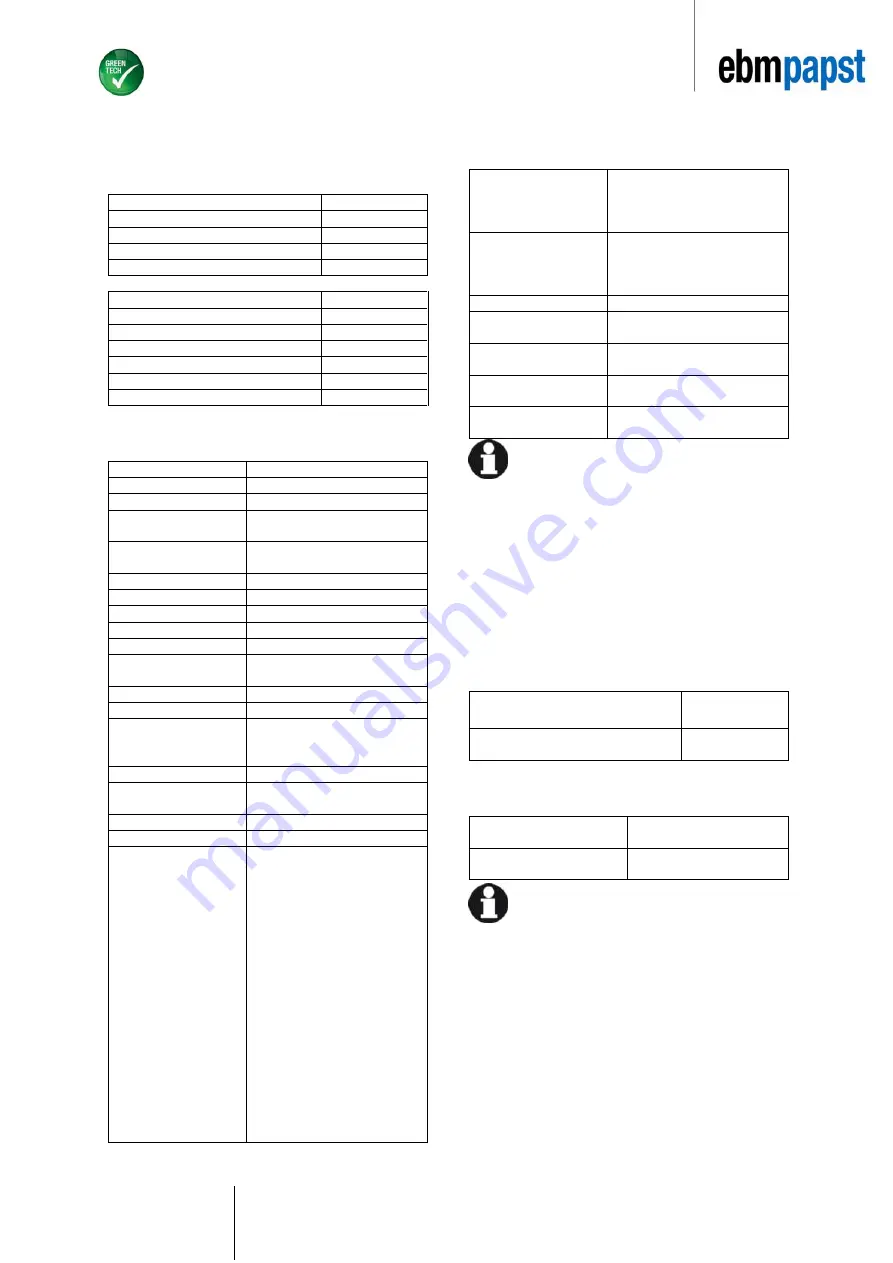
Part Number
Operating Instructions
Item no. LS-122.
Revision 002
Release 18/02/2016
Page 5 of 12
ebm-papst A&NZ Pty Ltd
10 Oxford Road · Laverton North VIC 3026 · Phone +61 (03) 9360 6400 · Fax +61 (03) 9360 6464
ABN 33 115 927 556
NSW Phone +61 (02) 9827 6400 · NSW Fax +61 (02) 9827 6464 · NZ Phone +64 (09) 525 0245 · NZ Fax +64 (09) 525 0246
[email protected] · www.ebmpapst.com.au
AF1250-001
AFFB1250-00
3.2
Nominal data
Motor
M3G150-NA
Phase
3~
Nominal Voltage / VAC
400
Nominal voltage range / VAC
380 .. 480
Frequency / Hz
50/60
Method of obtaining data
maximum load
Speed / min
-1
548
Power consumption / W
1800
Current draw / A
2.6
Max. Back pressure / Pa
78
Min. ambient temperature / °C
-25
Max. ambient temperature / °C
60
Subject to change
3.3
Technical description
Mass
118 kg
Size
1250 mm
Rotor surface
Painted black
Electronics housing
material
Die-cast aluminium, painted
black
Blade material
Die-cast aluminium, painted
black
Housing material
Galvanised steel
Guard grille material
Steel phosphate
Number of blades
3
Blade pitch
0º
Airflow direction
“A”
Direction of rotation
Counter clockwise, viewed
toward rotor
Degree of protection
IP 55
Insulation class
“F”
Moisture (F) /
Environmental (H)
protection class
F5
Installation position
Shaft horizontal or rotor on top
Condensate drainage
holes
On stator side
Mode
S1
Motor bearing
Ball bearing
Technical features
-
Output 10 VDC, max. 10 mA
-
Output 20 VDC, max. 50 mA
-
Output for slave 0-10 V
-
Input for sensor 0-10 V or 4-20
mA
-
External 24V input (parameter
setting)
-
External release input
-
Alarm relay
-
Integrated PID controller
-
Power limiter
-
Motor current limitation
-
PFC, passive
-
RS-485 MODBUS-RTU
-
Soft start
-
Control input 0-10 VDC/PWM
-
Control interface with SELV
potential safely disconnected
from the mains
-
Thermal overload protection for
electronics/motor
-
Line under voltage / phase
failure detection
Touch current
according to IEC 60990
(measuring circuit Fig.
4, TN system)
<= 3.5 mA
Electrical hook-up
Via terminal box
Motor protection
Reverse polarity and locked-rotor
protection
Protection class
I (with customer connection of
protective earth)
Conformity with
standards
EN 61800-5-1, CE
Approval
EAC; UL 1004-7 + 60730; C22
No.77 + CAN/CSA-E60730-1
With regard to cyclic speed loads, note that the
rotating parts of the device are designed for a
maximum of one million load cycles. If you have
specific questions, consult ebm-papst A&NZ for
support.
3.4
Mounting data
Secure the screws against unintentional loosening (e.g. use
self-locking screws).
Any further mounting data required can be taken from the
product drawing.
3.5
Transport and storage conditions
Use the device in accordance with its degree of protection.
Max. permissible ambient temp. for
motor (transport/storage)
+ 80 °C
Min. permissible ambient temp. for
motor (transport/storage)
- 40 °C
3.6
Electromagnetic compatibility
EMC immunity to
interference
According to EN 61000-6-2
(industrial environment)
EMC interference emission
According to EN 61000-6-4
(industrial environment)
If several devices are switched in parallel on the
supply side so that the line current of the
arrangement is in the range of 16 – 75 A, then this
arrangement conforms to IEC 61000-3-12 provided
that the short-circuit power S
sc
at the connection point
of the customer system to the public power system is
greater than or equal to 120 times the rated output of
the arrangement. It is the responsibility of the
installation engineer or operator/owner of the device
to ensure, if necessary after a consultation with the
network operator, that this device is only connected to
a connection point with a S
sc
value that is greater
than or equal to 120 times the rated output of the
arrangement.